Room Temperature-Cured Corrosion Protection of Metals
with Novel 2K Waterborne Organofunctional Silane Pretreatments

Corrosion is by far one of the most damaging and costly natural phenomena mankind faces across the globe, significantly impacting the aerospace, automotive, construction and electronic industries year after year. While there are many different methods to protecting metals from corrosion, chromate treatment has been one of the most well-established, inexpensive methods used across the globe over the past several decades. Although the performance, efficiency and affordability of chromate treatment has benefited the corrosion protection industry for years now, governmental regulations and public awareness of the hazards associated with chromate treatment has never been higher.
Since 2013, hexavalent chromium has been classified as a carcinogen and mutagen by the European Union. Furthermore, Europe’s Registration, Evaluation, Authorization & Restriction of Chemicals (REACH) regulations have restricted the use of hexavalent chromium in almost every industry across Europe. Although the European Chemical Agency (ECHA) has approved some Authorization Applications covering the use of hexavalent chromium in aerospace metal pretreatments and aerospace coatings, all these decisions have not yet been approved by the European Commission. Due to potentially serious consequences of corrosion-related structural failure and the long qualification periods required for new aerospace-related products, the topic of environmentally friendly corrosion protection alternatives has been a major interest to manufacturers, governments and raw material suppliers of the aerospace industry over the past several years.
One viable alternative to these hazardous corrosion protection technologies is organofunctional silane technology. The mechanism of corrosion protection from organofunctional silane pretreatments is best described by the ability of the highly crosslinked silicon-based network to act as a barrier when applied on a metal surface. 1 As organofunctional alkoxysilanes generate volatile organic compounds (VOCs) upon undergoing hydrolysis in a metal pretreatment application, the introduction of volatile solvents into environmentally friendly systems is counterintuitive. For this reason, waterborne, VOC-free silane technology is attractive for these types of environmentally friendly corrosion protection applications, as it offers excellent corrosion resistance performance without having to deal with the harmful exposure of hazardous pretreatments, volatile solvents or heavy metals.
Organofunctional alkoxysilanes contain hydrolyzable alkoxysilane functional groups that can form covalent bonds with inorganic surfaces that contain hydroxyl groups, such as metals. In this work, the organofunctional silanes used have silicon functional groups comprising of methoxy or ethoxy groups. Organofunctional silanes also consist of an organofunctional group that can react with organic polymers, resins or the surrounding environment. The simultaneous reaction of the silicon functional groups and organofunctional groups allow organofunctional alkoxysilanes to act as a coupling agent between inorganic surfaces and organic systems. For an organofunctional alkoxysilane to sufficiently adhere to an inorganic surface, hydrolysis must first take place at the alkoxy sites in the presence of water, which leads to the formation of silanol groups as alcohol is liberated as a byproduct. Organofunctional alkoxysilanes with methoxy groups typically liberate methanol during this hydrolysis process, while organofunctional alkoxysilane with ethoxy groups typically liberate ethanol in the same process.
When silanol groups on a hydrolyzed alkoxysilane come into contact with an inorganic surface, the silanol groups will initially form hydrogen bonds with the hydroxyl groups present on the inorganic surface. These hydrogen bonds can form siloxane bonds between the organofunctional alkoxysilane network and the inorganic surface when the condensation rate is sufficiently high, which is achieved by several methods including removing moisture from the system or shifting the pH of the system. These siloxane bonds provide the strong adhesion characteristics that organofunctional alkoxysilanes are typically known for. With proper surface preparation, organofunctional alkoxysilane-based pretreatments can form siloxane bonds through condensation to many sites on the inorganic surface, eventually forming a highly crosslinked organofunctional siloxane network (Figure 1). This organofunctional alkoxysilane film can passivate the surface of a metal substrate, providing a barrier to keep water and salts from penetrating the underlying metal surface. Furthermore, the organofunctional groups can provide additional hydrophobicity and adhesion promotion to any subsequent organic topcoats that may be applied for further corrosion protection of the metal surface.

As one of the main driving forces of silanol condensation is the removal of moisture from the system, waterborne silane metal pretreatments are typically subject to an elevated temperature cure (ranging from 80 °C – 200°C) after application to achieve sufficient curing. As these elevated temperature cures limit the efficiency and affordability of these applications across many industries, there are other factors worth exploring that influence the rate of silanol condensation in similar systems. By adding a specialty amine-functional silane oligomer that comprises of methoxy groups into a waterborne system, the crosslinking density is increased due to the rapid hydrolysis of methoxy groups and condensation of silanol groups in the presence of water. 2 Additionally, the amine functionality of this specialty amine-functional silane oligomer shifts the pH of a waterborne system from acidic or neutral to basic. As basic pH environments have been shown to increase the condensation rate of amine-functional alkoxysilanes compared to an acidic pH environment, this pH shift could also be responsible for increasing the crosslinking density of a waterborne system without the need for an elevated-temperature curing procedure. 3
Part of the organofunctional group on this specialty amine-functional silane oligomer is hydrophobic. Although hydrophobic silane oligomers are commonly used in high solids and solvent-based systems, this particular silane oligomer is stable in waterborne systems for a sufficient amount of time to be used for metal treatment applications. This is partly due to the hydrophilic amine group on this silane oligomer, allowing improved solubility in waterborne systems compared to a hydrophobic silane oligomer without amine functionality. The waterborne organofunctional silanol system with functionalized colloidal silica used in this work contains only a trace amount of volatile organic constituents, typically less than one percent by weight. While this waterborne pretreatment can provide sufficient corrosion resistance on its own depending on the metal substrate of choice and the surrounding environment, the addition of a specialty amine-functional silane oligomer into the system will be investigated in this work to better understand how to improve the performance of this novel technology.
When Part B is added into Part A of the commercially available heavy metal-free sol-gel pretreatment system, the 3-trimethoxysilylpropyl glycidyl ether undergoes hydrolysis and condensation in the presence of water and the zirconium n-propoxide. 4 As metal alkoxides, such as zirconium n-propoxide, are highly reactive, epoxide ring opening may also be occurring when 3-trimethoxysilylpropyl glycidyl ether comes into contact with zirconium n-propoxide. 5 Several companies within the aerospace industry have approved this commercially available heavy metal-free sol-gel pretreatment system to this day.
In this work, we demonstrate that a room temperature-cured two-component system based on a waterborne organofunctional silanol system with functionalized colloidal silica and a specialty amine-functional silane oligomer provides superior corrosion resistance and overall protection when compared to commercial benchmarks, therefore expanding the applicability of this technology to applications where an extensive thermal curing procedure is not feasible.
Experimental Methods
Materials
Waterborne organofunctional silanol system with functionalized colloidal silica (Dynasylan ® SIVO 110), alkaline neutralization agent (Dynasylan SIVO 111) and the specialty amine-functional silane oligomer are available from Evonik Industries AG. Commercially available heavy metal-free sol-gel pretreatment (3M™ Surface Pre-treatment AC-130-2) was purchased by Pacific Coast Composites. Sodium hydroxide 99.99% purity and ethyl alcohol 99.5% purity were purchased from Sigma Aldrich. Bulk Kleen 737G was purchased from Bulk Chemicals. Deionized (DI) water was obtained with a water purification system (WaterPro ® Plus) originally purchased from LabConco Corporation. Aluminum 2024T3, and cold rolled steel substrates were purchased from ACT Test Panels LLC. Chrome Hazard-Free Epoxy Flexible Primer CM0483790 was purchased from Sherwin Williams. Water-Reducible High-Performance Epoxy Primer 44GN098 was purchased from PPG Aerospace.
Pretreatment Formulation Preparation
The waterborne pretreatments evaluated in this article were formulated in 150 mL glass beakers (Table 1). The waterborne pretreatments WB1 and WB3 did not require any induction time after formulating the system. For the waterborne pretreatments WB2 and WB4, the specialty amine-functional silane oligomer is added into the DI water and waterborne organofunctional silanol system with functionalized colloidal silica mixture and is allowed to mix for ~ 20 minutes before application. This induction time is required to allow for the organofunctional silane molecules in the formulation to hydrolyze and condense in the presence of water. In this work, the waterborne pretreatments WB2 and WB4 were used within an 8-hour time frame before gelling starts to occur. The waterborne pretreatment, WB5, is a two-component system where approximately 2 grams of liquid part B is added into approximately 98 grams of liquid part A and mixed for the induction time of ~ 30 min. This induction time is required to allow for the 3-trimethoxysilylpropyl glycidyl ether component in part B to undergo hydrolysis and condensation in the presence of the water and zirconium n-propoxide that are present in part A. As specified in the technical data sheet of this product, application of the system must take place within the ~ 10-hour pot life for optimal performance.

The specialty amine-functional silane oligomer is 100% active solids, while the waterborne organofunctional silanol system with functionalized colloidal silica is 36% active solids and the commercially available heavy metal-free sol-gel pretreatment is ~ 2% active solids. The final wt% solids of the waterborne pretreatment formulations in this work were optimized to obtain clear films that do not impart any negative optical characteristics to the metal surfaces after the pretreatment is applied. As the optimal silane concentration in a waterborne silane pretreatment depends on the surface roughness of the metal substrate, different silane concentrations were used on aluminum substrates compared to cold rolled steel substrates.
Primer Formulation Preparation
To prepare the Chrome Hazard-Free Epoxy Flexible Primer CM0483790 primer (henceforth referred to as “solventborne 2K epoxy primer”), the entire adduct (200 mL) and reducer (200 mL of acetone) was added into the base component (600 mL) and shaken in a paint shaker for exactly 15 min. This paint was filtered using a paint strainer before being applied within the 3-hr pot life onto the pretreated metal substrates. These preparation instructions are readily available on the technical data sheet and paint can of this product.
To prepare the Water-Reducible High-Performance Epoxy Primer 44GN098 (henceforth referred to as “waterborne 2K epoxy primer”), the entire catalyst component (126 mL) was mixed into the base component (251 mL) and DI water was added (568 mL). This paint was then shaken in a paint shaker for exactly 5 min, being applied within the 4-hr pot life onto the pretreated metal substrates. These preparation instructions are also readily available on the technical data sheet and paint can of this product.
Cleaning and Application Procedures
Metal Surface Cleaning Procedure
Before applying the waterborne silane pretreatments, the metal substrates are cleaned to achieve optimal surface wetting properties. The metal substrates are first wiped twice with an ethyl alcohol-soaked paper towel, then dried with a compressed air gun and placed in an alkaline washing solution for approximately 3 min at 140 °F – 150 °F. This alkaline solution is prepared by adding 150 grams of Bulk Kleen 737G into 10 liters of DI water and stirring for several hours. The metal substrates are then rinsed with DI water and finally dried with a compressed air gun.
Pretreatment Application Procedure
After the metal substrates are properly cleaned and the waterborne coating formulations have been prepared, the pretreatments are applied via a dip coating procedure. The metal substrates are fully immersed in the waterborne silane formulations for 60 sec at 23 °C. After the 60-sec immersion, the metal panels are then removed from the pretreatment bath and hung vertically for 10 min to allow for excess liquid to drip off the metal surfaces.
Primer Application Procedure
Both primers were applied with an HVLP spray gun (Jaguar SLP). A tip size of 1.3 mm was used, with the pot and tip pressure kept at approximately 10 psi. During the application procedure, the temperature of the surrounding environment was ~ 68 F, and the humidity was kept at ~ 40%. These were within the recommended conditions for both primers as specified by the respective technical data sheets. The dry film thickness for all the primed substrates fell within 1.0 – 1.2 mils.
Pretreatment Curing Procedure
After air drying at 23 °C for ~ 10 min following the dip coat procedure, the pretreated metal substrates are left to air dry at 23 °C to cure for an additional 24 hrs or are placed in an oven for 30 min at 180 °C. Although the commercially available heavy metal-free sol-gel pretreatment requires a minimum of 60 min of room temperature curing, the WB5-pretreated metal substrates were cured at room temperature for 24 hrs to ensure full curing.
Primer Curing Procedure
After applying the primers on the blank or pretreated metal substrates, the primed substrates were left to dry at room temperature and approximately 40% relative humidity for a minimum of 14 days.
Testing Procedures
Contact Angle Measurement Procedure
After applying and curing the pretreated aluminum 2024T3 substrates, a goniometer (Ramé-Hart Inc.) is used to measure the static contact angle of DI water on the substrates. Each measurement reported in this article is the average of 10 measurements. Pictures were also taken of static water droplets on the various surfaces.
Neutral Salt Spray Testing Procedure
Before evaluating the pretreated metal substrates in a neutral salt spray test, wax was used to coat the edges of the metal substrates. The pretreated metal substrates were evaluated with a Q-Fog Cyclic Corrosion Tester (The Q-Panel Company) according to ASTM B117. The primed metal substrates were also evaluated with this test procedure in further studies.
Alkaline Resistance Testing Procedure
A solution containing 10 wt% sodium hydroxide (NaOH) and 90 wt% DI water was formulated and stirred for 60 min at 23 °C until the sodium hydroxide pellets fully dissolved. Although this exothermic reaction increases the temperature of the solution after several minutes of mixing, the solution returned to room temperature after 60 min of mixing. After properly applying and curing the waterborne pretreatments on the aluminum substrates, the substrates were first weighed on three separate scales. The average and standard deviation of these weight measurements were recorded. Following this weighing, the substrates were immersed in the alkaline solution for 10 min at 23 °C. Following this, the pretreated metal substrates were rinsed with DI water and dried with a compressed air gun. The substrates were then weighed on three separate scales to investigate any mass loss that occurred during the test.
Water Immersion Testing Procedure
The uncoated and pretreated cold rolled steel substrates are immersed in DI water for seven days in an oven held at 50 °C. Following this seven-day immersion period, the cold rolled steel substrates are removed from the solution and observed for any signs of corrosion.
Electrochemical Impedance Spectroscopy Testing Procedure
Electrochemical Impedance Spectroscopy (EIS) testing was performed by Matergenics Incorporated. Gamry PCI4/750 potentiostats were used to record the impedance spectra at frequencies of 0.1 cycles/second – 100,000 cycles/second. The pretreated metal substrates were immersed in an aqueous conductive 3.5 wt% NaCl solution during testing. All tests were performed in a grounded Faraday cage at room temperature.
Humidity Testing Procedure
The pretreated metal panels were kept in a humidity chamber (Associated Environmental Systems, Inc.) for 168 hrs at a constant relative humidity of 95% and a constant temperature of 35 °C. Pictures were taken of the pretreated metal panels after this 168-hr exposure in the humidity chamber.
Post Salt Spray Adhesion Testing Procedure
After the primed cold rolled steel substrates were subject to 350 hrs in a neutral salt spray test (in accordance with ASTM B117), the substrates were removed from the salt spray chamber and tested for adhesion. This cross hatch test was performed in accordance with ASTM D3359 using a PA-2000 cross hatch test kit from Gardco.
Results and Discussion
Surface Contact Angle Analysis
The incorporation of a specialty amine-functional silane oligomer into a waterborne organofunctional silanol silane system with functionalized colloidal silica increases the hydrophobicity of the system when applied as a metal pretreatment. The hydrophobic organofunctional group on this specialty amine-functional silane oligomer is non-polar, therefore repelling polar solvents such as water and making the system more hydrophobic. 6 Additionally, the presence of hydrophilic amine groups allows for improved solubility in waterborne systems. Without these polar amine groups, achieving a miscible system in water with an acceptable pot life would be difficult.
While there are several ways of characterizing the hydrophobicity of a metal pretreatment, valuable insight can be gained by observing the wetting properties of water on the surface. Water tends to wet out when placed on a bare aluminum surface, indicating a hydrophilic surface. When water is placed on an aluminum surface that has been made more hydrophobic with a surface pretreatment, the water tends to bead up. In addition to visually observing the wetting properties of water on a metal surface, contact angle measurements of water droplets on the metal surface also provides important information on the hydrophilic or hydrophobic behavior of the surface treatment. The average contact angle of a DI water droplet on uncoated aluminum 2024T3 is 13°. On WB1-pretreated aluminum 2024T3, the average contact angle of a DI water droplet is 17° when the pretreatment is cured at 23 °C and 34° when the pretreatment is cured at 180 °C. On WB2-pretreated aluminum 2024T3, the average contact angle of a DI water droplet is 62° when the pretreatment is cured at 23 °C and 62° when the pretreatment is cured at 180 °C. The average contact angle of a DI water droplet is 27° on WB5-pretreated aluminum 2024T3 cured at 23 °C (Figure 2).

Under ambient curing conditions (24 hrs at 23 °C), adding the specialty amine-functional silane oligomer into the waterborne organofunctional silanol system with functionalized colloidal silica increased the contact angle of DI water on the aluminum 2024T3 pretreated surface by 264% from ~ 17° to ~ 62°. Under elevated curing conditions (30 min at 180 °C), adding the specialty amine-functional silane oligomer into the waterborne organofunctional silanol system with functionalized colloidal silica increased the contact angle of DI water on the aluminum 2024T3 pretreated surface by 82% from ~ 34° to ~ 62°. Compared to the contact angle of water droplets on aluminum 2024T3 substrates pretreated with the commercially available heavy metal-free sol-gel pretreatment, water droplets on the aluminum 2024T3 substrates pretreated with the specialty amine-functional silane oligomer-containing solutions exhibited a 130% increase in contact angle from ~ 27° to ~ 62°. This was true regardless of the curing procedure for the WB2-pretreated aluminum 2024T3 substrates.
It is important to note the impact the curing procedure has on the metal pretreatments described above. For the waterborne organofunctional silanol system with functionalized colloidal silica pretreatment cured at 23 °C, the average contact angle of DI water on the surface is 17°. When the waterborne organofunctional silanol system with functionalized colloidal silica pretreatment is cured at 180 °C, the average contact angle of DI water on the surface increases to 34°. This is likely due to the increased crosslinking density of the system and the reduction of hydroxyl groups on the metal surface as these hydrophilic hydroxyl groups have likely undergone more condensation with alkoxy sites in an elevated temperature environment.
While exposing the WB1-pretreated aluminum 2024T3 substrates to elevated temperatures reduced the hydrophilicity of the surface compared to identical pretreatments cured at room temperature, this was not the case for the WB2-pretreated aluminum 2024T3 pretreatments. As the specialty amine-functional silane oligomer contains methoxy groups that rapidly hydrolyze and condense in the presence of water, this increased crosslinking density may be occurring without the need for an elevated temperature cure. Additionally, the hydrophobic organofunctional group present on the specialty amine-functional silane oligomer does not require any elevated temperature exposure to act as a hydrophobic, non-polar moiety to prevent water from wetting out on the metal surface.
As confirmed by the contact angle measurements of DI water droplets on aluminum 2024T3 surfaces, the incorporation of a specialty amine-functional silane oligomer into the waterborne organofunctional silanol system with functionalized colloidal silica increases the contact angle of DI water on the metal surface. This is likely due to the hydrophobic organofunctional group on the specialty amine-functional silane oligomer, as it is a nonpolar group and prevents water from wetting out on the surface. Although the commercially available heavy metal-free sol-gel metal pretreatment on aluminum 2024T3 may provide a highly crosslinked silane network on the surface of the metal, it exhibits hydrophilic properties on the metal surface. This may be attributed to the hydrophilicity of the diol groups present in the system when the epoxy rings break open in the presence of water and zirconium n-propoxide. The reduction in hydrophilicity from the presence of the specialty amine-functional silane oligomer helps prevent water in the surrounding environment from efficiently wetting out on the metal surface and coming into contact with the underlying metal. This reduced contact between water and the underlying metal surface can lead a reduction in surface corrosion, which will be further investigated with other testing methods to confirm this hypothesis.
Neutral Salt Spray Testing
While there are many standardized testing procedures available to investigate the corrosion resistance of a metal pretreatment, neutral salt spray testing has been an industry standard for decades now. However, the corrosion mechanisms occurring on the metal surface in a salt spray chamber are fundamentally different than corrosion mechanisms out in the field. For this reason, these neutral salt spray test results should be analyzed as only part of the full scope of protection these waterborne metal pretreatments provide.
After pretreating the metal substrates with the WB1, WB2, WB3, WB4 and WB5 pretreatments, curing procedures varying from 23 °C for 24 hrs to 180 °C for 30 min were carried out. As previously mentioned, organofunctional silane-based materials typically require moisture to be driven out of the system for the silanol groups to effectively condensate onto an inorganic substrate. Without the presence of a specialty amine-functional silane oligomer or an elevated temperature curing procedure, a lack of corrosion resistance is expected due to the low rate of condensation between the silanol groups in the system, which prevents the pretreatment from efficiently passivating the metal surface. These low rates of condensation also typically result in poor adhesion between the pretreatment and the metal surface.
By incorporating a specialty amine-functional silane oligomer into the waterborne organofunctional silanol system with functionalized colloidal silica, the shift from acidic pH to basic pH should increase the rate of condensation between silanol groups in the system after hydrolysis occurs, leading to an improved surface passivation of the metal surface. Additionally, this influx of silanol groups in the system should also increase the rate of condensation between the silanol groups in the system and the hydroxyl groups on the metal surface, resulting in better adhesion to the metal, thus improving the corrosion resistance of the metal pretreatment over time. These hypotheses are supported by the superior corrosion resistance demonstrated by the waterborne organofunctional silanol system with functionalized colloidal silica and a specialty amine-functional silane oligomer in the system on both aluminum 2024T3 and cold rolled steel (Figure 3, figure 5 and figure 6).



As the commercially available heavy metal-free sol-gel pretreatment is acidic, flash rusting occurs upon application of the WB5 pretreatment on cold rolled steel, limiting the use of the commercially available heavy metal-free sol-gel pretreatment to just aluminum 2024T3 substrates for this work (Figure 4). As WB3 and WB4 both are neutral or alkaline, no flash rusting occurs on the WB3-pretreated or WB4-pretreated cold rolled steel. The neutral/alkaline pH of these pretreatments are due to the alkaline neutralization agent for the WB3 pretreatment or the alkaline specialty amine-functional silane oligomer for the WB4 pretreatment.

While these neutral salt spray testing results offer a promising glimpse into performance improvements obtained with the addition of a specialty amine-functional silane oligomer into waterborne pretreatments, other corrosion-related testing procedures are crucial in determining the full scope of the corrosion resistance performance for these systems. This includes alkaline resistance, water immersion, outdoor weatherability and electrochemical impedance spectroscopy testing to provide a more complete picture of the overall protection these waterborne metal pretreatments provide.
Alkaline Resistance Testing
In addition to the corrosion resistance of a metal pretreatment, the alkaline resistance of metal pretreatments are just as important to the automotive industry. As pretreated metal panels are often subject to repeated wash cycles with alkaline-based car wash fluids and detergents in the automotive industry, alkaline resistance of the entire coating system is a crucial performance criteria. Aluminum 2024T3 in particular is well-suited for the automotive industry given the high strength and fatigue resistance of this aluminum alloy. 7 Aluminum 2024T3 is most commonly used in rotors, wheel spokes and structural components within an automobile, all of which require significant resistance to alkaline media over the lifetime of the automobile. As previously hypothesized, the addition of a specialty amine-functional silane oligomer into a waterborne organofunctional silanol system with functionalized colloidal silica increases the crosslinking density and hydrophobicity of the system, which can in turn lead to improved resistance to aqueous alkaline media.
As detailed above, this alkaline solution exhibits a pH of ~ 14. Within minutes of immersing the pretreated metal substrates that don’t contain the specialty amine-functional silane oligomer (including WB1 and WB5), violent bubbling of the alkaline solution was observed (Figure 7). These bubbles are likely hydrogen gas, which is generated when bare aluminum in the zero oxidation state comes into direct contact with water (Scheme 1). If the waterborne organofunctional silanol system with functionalized colloidal silica-based pretreatment and aluminum oxide surface layer on the bare aluminum are removed by the high concentration of OH- groups within the alkaline solution, this reaction can take place. 8


The addition of a specialty amine-functional silane oligomer into the waterborne organofunctional silanol system with functionalized colloidal silica significantly reduced the amount of observable bubbling on the surface of the aluminum substrates. The protective aluminum oxide layer and bare reactive aluminum surface likely had less exposure to the alkaline media with this surface pretreatment due to the additional crosslinking and hydrophobicity provided by the specialty amine-functional silane oligomer (Fig 7).
After immersing the pretreated aluminum 2024T3 substrates in the 10 wt% NaOH aqueous solution for 10 min, the visual appearance of the aluminum 2024T3 was compared among pretreatment types. Regardless of the curing procedure, the uncoated aluminum 2024T3 and WB1-pretreated aluminum 2024T3 panels appeared significantly blacker after the test. The WB2-pretreated aluminum 2024T3 substrates on the other hand did show some surface defects and visible darkening after the test, but not nearly as significant a change as the untreated aluminum 2024T3 and WB1-pretreated aluminum 2024T3 substrates. The WB5-pretreated aluminum 2024T3 substrates also exhibited significant surface defects after the test (Figure 8).

In addition to visually observing the aluminum 2024T3 substrates before and after the alkaline immersion test, the weight of the substrates was recorded before and after the test as well. Across all the different metal pretreatment methods, the average weight of the pretreated aluminum 2024T3 substrates was 34.1 g. The uncoated aluminum 2024T3 weighed 31.5 g after the alkaline immersion test, indicating a ~ 7.62% weight loss. The WB1-pretreated aluminum 2024T3 cured at 23 °C weighed 30.6 g after the alkaline immersion test, indicating a ~ 10.26% weight loss. The WB1-pretreated aluminum 2024T3 cured at 180 °C weighed 30.6 g after the alkaline immersion test, indicating a ~ 13.20% weight loss. The WB2-pretreated aluminum 2024T3 cured at 23 °C weighed 33.05 g after the alkaline immersion test, indicating a ~ 3.08% weight loss. The WB2-pretreated aluminum 2024T3 cured at 180 °C weighed 33.95 g after the alkaline immersion test, indicating a ~ 0.29% weight loss. Lastly, the WB5-pretreated aluminum 2024T3 cured at 23 °C weighed 29.91 g after the alkaline immersion test, indicating a ~ 12.29% weight loss (Figure 9).
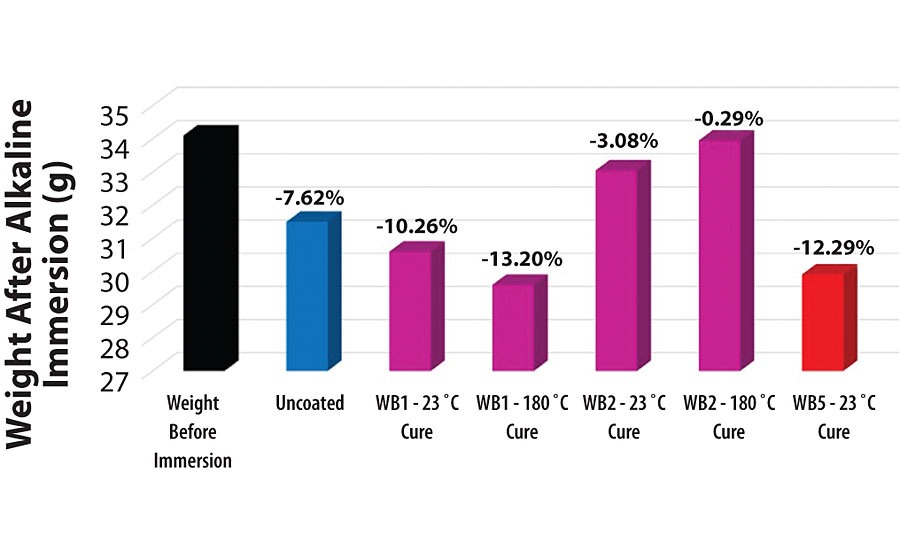
As described in Scheme 1, water reacting with bare aluminum in the zero oxidation state liberates aluminum hydroxide and hydrogen gas in the process. This aluminum hydroxide is soluble in the aqueous alkaline solution, and is likely the main contributor to the weight loss on the aluminum 2024T3 substrates during the alkaline immersion test. The more water that reacts with the exposed aluminum in the zero oxidation state, the more aluminum hydroxide is removed from the aluminum 2024T3 substrate, leading to a decrease in mass of the substrate.
The pretreatments containing the specialty amine-functional silane oligomer (WB2) likely have higher crosslinking densities than the same pretreatments without the specialty amine-functional silane oligomer (WB1). If the crosslinking density of the metal pretreatment is greater, the alkaline solution will have a more difficult time penetrating the pretreatment and reacting with the aluminum oxide protective layer and bare aluminum surface. Additionally, as this was an aqueous solution containing 90% DI water, the hydrophobic organofunctional group on the specialty amine-functional silane oligomer likely helped prevent the aqueous alkaline solution from penetrating the pretreatment surface. Although the WB2-pretreated aluminum 2024T3 substrates likely contain a highly crosslinked network on the surface when cured at 23 °C, this crosslinking density is likely further increased with the elevated curing temperature. This would explain the decrease in weight loss percentage for the WB2-pretreated aluminum 2024T3 substrates cured at 180 °C compared to the curing procedure at 23 °C. As the WB5-pretreated aluminum 2024T3 substrates also lost more weight than the WB2-pretreated aluminum 2024T3 substrates after this test, this could be indicative of a lower degree of crosslinking and less hydrophobicity with the commercially available heavy metal-free sol-gel pretreatment system.
Water Immersion Testing
While neutral salt spray testing often provides a good indication of how well a metal pretreatment provides corrosion resistance in the presence of an electrolytic mist, such as near the ocean, the test is not always indicative of corrosion protection performance in different environments. A solution of DI water has a lower concentration of H+ and OH- ions compared to a neutral salt spray mist and does not contain significant concentrations of sodium and chloride ions that are also present in the neutral salt spray mist. This reduction in the ionic strength of the DI water solution may cause some organic metal pretreatments to allow for moisture permeability in this type of environment if the surface of the organic metal pretreatment is similar in ionic nature to the DI water surrounding the system. This is often a possible explanation for why some metal pretreatments perform excellent in neutral salt spray testing environments but may fail DI water immersion tests. 9 The coatings on boat hulls are specifically developed for either freshwater or saltwater boats for this reason. After immersing the various cold rolled steel substrates in DI water for 7 days at 50 °C, the substrates were removed (Figure 10).

After immersing the uncoated and pretreated cold rolled steel substrates in DI water for 7 days in an oven held at 50 °C, different forms of corrosion were observed. The uncoated cold rolled steel and WB3-pretreated cold rolled steel (either cured at 23 °C or 180 °C) showed significant signs of general surface corrosion and a higher corrosion coverage, while the WB4-pretreated cold rolled steel (either cured at 23 °C or 180 °C) showed little general surface corrosion, lower corrosion coverage and visible signs of pitting corrosion. It is important to note that pitting corrosion occurred on all of the uncoated and pretreated cold rolled steel panels during this water immersion test and was the first sign of corrosion for all the substrates as well. However, as the substrates were continuously exposed to water throughout the duration of the test, general surface corrosion likely occurred alongside the pitting corrosion, eventually covering evidence of pitting corrosion in the uncoated cold rolled steel and WB3-pretreated cold rolled steel substrates (Figure 11). 10 By adding the specialty amine-functional silane oligomer into the waterborne pretreatments, the general surface corrosion and overall corrosion coverage was reduced, as seen by the select areas on the WB4-pretreated cold rolled steel substrates without any visible general surface or pitting corrosion. A deeper investigation into the corrosion process of each metal pretreatment in this water immersion test is ongoing, including observations of the substrates at multiple times during the seven-day period.

Outdoor Weatherability
When unprotected cold rolled steel is left outdoors in the presence of air and moisture, corrosion tends to take place rather quickly. This rate of corrosion depends on the direct exposure of the cold rolled steel surface to the oxygen, moisture and any other elements in the surrounding environment. As corrosion takes place, a protective layer of oxidation will form on the surface of the cold rolled steel, acting as a barrier to the surrounding environment and slowing down the corrosion rate over time. 11 Although this protective layer of oxidation slows down the rate of corrosion, it is typically a porous layer and allows moisture to further penetrate the cold rolled steel surface. This underlying moisture may cause the protective oxidation layer to de-adhere over time, re-exposing the bare metal surface and leading to a cyclic, destructive corrosion cycle over time. 12
The use of protective cold rolled steel pretreatments is a common practice of manufacturers to prevent any corrosion from occurring on the cold rolled steel during shipping and transport to customers across a wide variety of environments. Waterborne silane technology can be an efficient, environmentally friendly alternative to the typical conversion coatings (such as chromate treatment) that are used to protect cold rolled steel during this shipping and transport period. This protection stems from the highly crosslinked network on the surface of the cold rolled steel, as well as the presence of hydrophobic organofunctional group for some of these pretreatments. After being left outdoors and exposed to the natural environment in Piscataway, NJ, for just 30 days, uncoated and pretreated cold rolled steel substrates showed significant, but varying degrees of corrosion (Figure 12).

After 30 days of outdoor exposure, the WB4-pretreated cold rolled steel substrates showed visibly less corrosion than the WB3-pretreated cold rolled steel substrates. While an elevated temperature curing procedure typically leads to a higher crosslinked network for a system containing the waterborne organofunctional silanol system with functionalized colloidal silica and a specialty amine-functional silane oligomer, this elevated-temperature curing procedure for the WB4-pretreated cold rolled steel did not lead to improved weatherability in this test. One possible explanation could be the different orientation of the specialty amine-functional silane oligomer on the surface of the cold rolled steel. Previous work has shown that the curing temperature of amine-functional silanes has a significant impact on the molecular orientation of the silane on an inorganic surface. 13 It is possible that the room temperature curing procedure allowed for a greater concentration of the hydrophobic organofunctional groups to be present on the surface of the cold rolled steel, therefore preventing rain, humidity and other moisture-containing elements in the air from wetting out on the metal substrate during the duration of this test. The same cold rolled steel substrates were left outdoors and exposed to the surrounding environment for an additional 30 days then once again removed (Figure 13).

After 60 days of outdoor weathering, the WB4-pretreated cold rolled steel substrates continued to show improved weatherability compared to the WB3-pretreated cold rolled steel substrates. As previously mentioned, the porous oxidation layer on the surface of the uncoated and WB1-pretreated cold rolled steel substrates allowed for water to penetrate the bare metal surface, leading to new corrosion patterns after additional outdoor exposure. Although only 60 days of outdoor weathering was investigated in this work, continuing this test for an additional several months and expanding the test to different regions with varying climates throughout the year would provide additional valuable insight into the weatherability of these pretreatments.
Electrochemical Impedance Spectroscopy
EIS is a widely accepted characterization technique for analyzing the real-time deterioration behavior of pretreated metal substrates immersed in an electrolytic solution. 14 Through the simultaneous measurement of the resistance and capacitance of an organic pretreatment on a metal substrate, the impedance of the system can be calculated. The nonconductive nature of organic pretreatments typically leads to high impedances in the presence of an electrolytic solution. As the barrier efficiency of an organic pretreatment on metal is increased, less electrolytic solution is exposed to the bare metal surface over time, resulting in high impedances of the system. As an organic pretreatment on metal is immersed in an electrolytic solution, the impedance of the system should continuously drop over time as the electrolytic solution eventually penetrates the organic pretreatment surface and reaches the underlying bare metal substrate. 15 One significant benefit of EIS is the ability for this technique to detect microscopic instances of corrosion on the surface that may not be visible to the naked eye in other testing methods. 16 The impedance measurements in this test were carried out over a frequency range of 0.1 Hz to 100,000 Hz, as represented in the Bode plot in Figure 14.

The magnitude of the impedance for each metal pretreatment is correlated with the performance of the pretreatment as a barrier to water and salts in the surrounding environment. While it is always useful to analyze the EIS spectra for each metal pretreatment over the entire range of frequencies in this test, the comparison of the impedance magnitude (in ohms, Ω) for each of these aluminum 2024T3 pretreatments systems at 0.1 Hz is a well-established industry standard for how well a pretreatment will protect a metal surface from corrosion over time (Figure 15). 17

At 0.1 Hz, the impedance of the WB1-pretreated aluminum 2024T3 substrate cured at 180 °C was ~ 54.66 kΩ (54,660 ohms). Upon adding the specialty amine-functional silane oligomer into the system (WB2), the impedance of the pretreatment increased to ~ 69.34 kΩ (69,340 ohms) when cured at 23 °C. The impedance of the WB2-pretreated aluminum 2024T3 substrate was even further increased to 103.37 kΩ (103,370 ohms) when cured at 180 °C. By adding the specialty amine-functional silane oligomer into the waterborne organofunctional silanol system with functionalized colloidal silica, the impedance of the system increased by ~ 26.9% without the need for an elevated-temperature curing procedure. With the elevated-temperature curing procedure in place, the addition of the specialty amine-functional silane oligomer into the waterborne organofunctional silanol system with functionalized colloidal silica increased the impedance of the system by ~ 89.1%. The commercially available heavy metal-free sol-gel pretreatment exhibited the lowest impedance, 51.48 kΩ (51,480 ohms), compared to the other systems tested at 0.1 Hz.
Addition of a specialty amine-functional silane oligomer into the waterborne organofunctional silanol system with functionalized colloidal silica generally increased the impedance of the system. This was true regardless of the curing temperature, which can best be explained by the additional crosslinking introduced into the system by the specialty amine-functional silane oligomer. This additional crosslinking in the system led to increases in the impedance of the pretreatments by making the pretreatments a more efficient barrier to water and salts in the surrounding environment. While contact angle measurements, neutral salt spray testing, alkaline resistance testing, water immersion testing and outdoor weatherability testing all provided observable evidence related to waterborne pretreatment protection of metal surfaces, this EIS data provides valuable measurable data regarding the barrier properties of these waterborne pretreatments. Just as the specialty amine-functional silane oligomer improved the hydrophobicity, alkaline resistance, and salt spray resistance of the waterborne pretreatments, it also improves the barrier properties of these waterborne pretreatments without the need for an elevated-temperature cure.
Humidity Resistance
After 168 hrs in the humidity resistance test, different forms of corrosion were observed on each type of pretreated cold rolled steel (Figure 16). While general surface corrosion was observable on the entirety of the WB3-pretreated cold rolled steel cured at 180 °C and the WB4-pretreated cold rolled steel cured at 180 °C, only a few corrosion spots were observed on the WB3-pretreated cold rolled steel cured at 23 °C. The uncoated cold rolled steel also only showed several corrosion spots instead of general surface corrosion, but did show significantly more corrosion spots than the WB3-pretreated cold rolled steel cured at 23 °C.

As aluminum 2024T3 is a less reactive substrate than cold rolled steel, all the pretreatments helped protect the bare aluminum 2024T3 surfaces throughout the duration of this 168-hr humidity test (Figure 17). However, the uncoated aluminum 2024T3 substrate showed signs of corrosion wherever water droplets formed on the surface during this test.

While further differences in the humidity resistance of these varying pretreatments on both cold rolled steel and aluminum 2024T3 could arise after several hundred more hours in a high-humidity environment, this has not yet been investigated. From this test, it is apparent that the metal pretreatments containing the specialty amine-functional silane oligomer (WB2 and WB4) and cured at 23 °C demonstrate an observable improvement in the humidity resistance of the metal substrate over time. This can be explained by several previously discussed factors, most notably the increased hydrophobicity of the pretreatments containing the specialty amine-functional silane oligomer, which could subsequently prevent the humidity droplets in the humid environment from wetting out on the metal substrates throughout the duration of this test.
Corrosion Resistance and Adhesion of Primed Silane-Pretreated Metal Substrates
While previous work has shown the significant improvements of this novel 2K waterborne organofunctional silane system compared to the commercially available benchmark, this commercially available benchmark was not initially developed to provide corrosion protection of metal substrates on its own, but rather to act as a chrome-free adhesion promoter for primers onto the metal substrates. To further support the adaptation of this novel 2K waterborne organofunctional silane technology, it is important to evaluate the performance of this system with additional primers and topcoats applied onto the pretreatment. As 2K epoxy primers are one of the most widely used primer types in the aerospace industry, two different chrome-free 2K epoxy primers were applied onto these varying metal pretreatments and evaluated for corrosion protection performance.
After 1,000 hrs in a neutral salt spray test, different types of coating defects were visible on the solventborne 2K epoxy-primed aluminum 2024T3 substrates (Figure 18). Blistering was observed on the primed aluminum 2024T3 substrate with no pretreatment, with the WB1 pretreatment cured at 180 °C, and the WB2 pretreatment cured at both 23 °C and 180 °C. While the degree of blistering varied from substrate to substrate, this form of coating defect is different than the pitting corrosion that was observed on the primed WB5-pretreated aluminum 2024T3 substrate (Figure 19). Pitting corrosion is a particularly catastrophic type of corrosion in aluminum alloys, mainly due to the severe impact pitting corrosion has on the structural integrity of the metal. Although blistering was observed on the primed aluminum 2024T3 substrates with the WB1 and WB2 pretreatments after 1,000 hrs in a neutral salt spray test, no pitting corrosion was observed on these substrates.


After 1,000 hrs in a neutral salt spray test, different types of coating defects were also visible on the waterborne 2K epoxy-primed aluminum 2024T3 substrates (Figure 20). Blistering was observed on the primed aluminum 2024T3 substrate with no pretreatment and the WB2 pretreatment cured at both 23 °C and 180 °C. While the degree of blistering varied from substrate to substrate, this form of coating defect is different than the severe pitting corrosion that was observed on the primed WB1-pretreated and WB5-pretreated aluminum 2024T3 substrates. Although blistering was observed on the primed aluminum 2024T3 substrates with the WB2 pretreatments after 1,000 hrs in a neutral salt spray test, no pitting corrosion was observed.

As cold rolled steel is a much more reactive substrate than aluminum 2024T3, a neutral salt spray test of 225 hrs was sufficient to observe significant differences in the corrosion resistance of the primed cold rolled steel substrates. After 225 hrs in a neutral salt spray test, the WB4-pretreated cold rolled steel showed significantly improved corrosion resistance compared to the WB3-pretreated cold rolled steel and the cold rolled steel with no pretreatment when primed with the solventborne 2K epoxy primer (Figure 21). Furthermore, the primed WB4-pretreated cold rolled steel cured at 23 °C showed less corrosion on the surface than the WB4-pretreated cold rolled steel cured at 180 °C. While general surface corrosion was observed on most of these primed cold rolled steel substrates, it is important to note that pitting corrosion was observed on only the primed WB2-pretreated cold rolled steel substrate.

After 225 hrs in a neutral salt spray test, the WB4-pretreated cold rolled steel cured at 23 °C showed significantly improved corrosion resistance compared to the WB4-pretreated cold rolled steel cured at 180 °C, in addition to the WB3-pretreated cold rolled steel and the cold rolled steel with no pretreatment when primed with the waterborne 2K epoxy primer (Figure 22). While some blistering and general surface corrosion was observable on the primed WB4-pretreated cold rolled steel cured at 23 °C, the magnitude and coverage of this corrosion was significantly less than all the other pretreatment types.

Although investigating the corrosion resistance of these primed metal substrates offers valuable insight into the performance of the underlying metal pretreatment systems, the adhesion of these primers after exposure to these corrosive environments is another important property to look into. For this reason, cross hatch tests were performed on the primed cold rolled steel substrates after 225 hrs in the neutral salt spray test. It is important to note that as these adhesion tests were performed on the substrates after the 225 hrs in a neutral salt spray test, there were several areas on each substrate that had undergone corrosion. In order to improve the reliability of this test, these areas were avoided if possible during the cross hatch test, and several cross hatch tests were performed on each substrate.
It is evident that the WB3-pretreated cold rolled steel primed with the solventborne 2K epoxy primer showed complete adhesion loss, as seen by the full delamination of the primer after the cross hatch test was performed (Figure 23). While the primed cold rolled steel substrate without a pretreatment did not suffer complete adhesion loss, it still lost considerably more primer material after the cross hatch test when compared to the primed WB4-pretreated cold rolled steel substrates. When comparing the primed WB4-pretreated cold rolled steel substrates, it can be seen that the WB4 pretreatment cured at 23 °C exhibited slightly better adhesion than the WB4 pretreatment cured at 180 °C.

The WB3-pretreated cold rolled steel primed with the waterborne 2K epoxy primer also showed complete adhesion loss, as seen by the full delamination of the primer after the cross hatch test was performed (Figure 24). While the primed cold rolled steel substrate without a pretreatment did not suffer complete adhesion loss, it still lost considerably more primer material after the cross hatch test when compared to the primed WB4-pretreated cold rolled steel substrates. The curing temperature of the primed WB4-pretreated cold rolled steel substrates does not appear to significantly impact the adhesion results in this test. It is important to note that for all these primed cold rolled steel substrates, complete adhesion loss was observed over areas where blistering had occurred during the neutral salt spray test.

While 225 hrs was a sufficient amount of time to observe considerable differences in the corrosion protection of the primed cold rolled steel substrates, the neutral salt spray testing on the aluminum 2024T3 panels will continue past 2,000 hrs in further studies. After this amount of time, adhesion testing will also be performed on the corroded substrates to gain further insight into the adhesion capabilities of the primed aluminum 2024T3 pretreatments.
As previously mentioned, it is important to compare the performance of this novel 2K waterborne organofunctional silane system with additional primers and topcoats to the commercially available benchmark technology. From the neutral salt spray results and adhesion test results above, it is evident that the presence of the hydrophobic amine-functional silane oligomer in the novel 2K waterborne organofunctional silane pretreatments has an observable improvement on these crucial properties. This is true for both a waterborne 2K epoxy primer and solventborne 2K epoxy primer when applied onto these novel metal pretreatments. As the presence of the hydrophobic amine-functional silane oligomer in the novel 2K waterborne organofunctional silane system increases the hydrophobicity of the underlying metal pretreatment, this may slow down the corrosion process at the bare metal surface even when primed with these 2K epoxy primers. Additionally, the novel 2K waterborne organofunctional silane pretreatments may also improve the adhesion of the 2K epoxy primers due to the reduced amount of pitting corrosion and blistering of the primers over time.
Conclusion
As the use of waterborne silane technology continues to gain interest as an environmentally friendly alternative to well-established corrosion protection methods, research into optimizing the performance and cost of these systems is crucial to the growth and commercialization of this technology. By incorporating a specialty amine-functional silane oligomer into existing waterborne silane pretreatments, the need for an elevated curing temperature is effectively eliminated, opening the door to this type of environmentally friendly technology to industries and markets that were previously restricted by this elevated-temperature curing requirement. The novel 2K room temperature-cured waterborne silane pretreatment is not the first commercial heavy metal-free, room temperature-cured sol-gel pretreatment on the market. However, in terms of surface protection and applicability to various metal substrates it is a significant improvement to the commercially available products in the market currently. It is promising that the contact angle measurements, neutral salt spray testing, alkaline resistance testing, outdoor weatherability testing and electrochemical impedance spectroscopy support this claim of increased surface protection with the use of this novel 2K room temperature-cured waterborne silane pretreatment. While these trends generally hold true with various 2K epoxy aerospace primers applied onto these novel 2K room temperature-cured waterborne silane pretreatments, further research is underway to understand the complete scope of this system and its interaction with additional aerospace primers and aerospace topcoats included in these systems. This work is currently underway in hopes of further improving the performance, affordability and attractiveness of waterborne silane pretreatments as environmentally friendly corrosion protection alternatives.
For more information, email jacob.shevrin@evonik.com.
References
1 Zhu, D.; van Ooij, W.J. Corrosion Protection by Water-based Silane Mixtures of Bis-[trimethoxysilylpropyl]amine and Vinyltriacetoxysilane, Progress in Organic Coatings 2004 , 49 (1), 42-53.
2 Issa, A.; Luyt, A. Kinetics of Alkoxysilanes and Organoalkoxysilanes Polymerization: A Review, Polymers 2019 , 11 (3), 537.
3 Paquet, O.; Salon, M-C. B.; Zeno, E.; Belgacem, M.N. Hydrolysis-Condensation Kinetics of 3-(2-amino-ethylamino)propyl-trimethoxysilane, Materials Science and Engineering C 2012 , 32, 487-493.
4 Philipp, G.; Schmidt, H. The Reactivity of TiO2 and ZrO2 in Organically Modified Silicates, Journal of Non-Crystalline Solids 1986 , 82 (1-3), 31-36.
5 Hoebbel, D.; Nacken, M.; Schmidt, H. The Effect of Nanoscaled Metal Oxide Sols on the Structure and Properties of Glycidoxypropyltrimethoxysilane Derived Sols and Gels, Journal of Sol-Gel Science and Technology 2000 , 19 (1-3), 305-309.
6 Murshid, N.; Wang, X. Hydrophobic Effect of Alkyl Groups Stabilizing Self-Assembled Colloids in Water, Journal of Physical Chemistry B 2017 , 121, 6280-6285.
7 Kermanidis, A.; Petroyiannis, P.; Pantelakis, S. Fatigue and Damage Tolerance Behaviour of Corroded 2024 T351 Aircraft Aluminum Alloy, Theoretical and Applied Fracture Mechanics 2005 , 43 (1), 121-132.
8 Zhang, J.; Klasky, M.; Letellier, B.C. The Aluminum Chemistry and Corrosion in Alkaline Solutions, Journal of Nuclear Materials 2009 , 384, 175-189.
9 Poznyak, S.; Zheludkevich, M.; Raps, D.; Gammel, F.; Yasakau, K. Ferreira, M. Preparation and Corrosion Protective Properties of Nanostructured Titania-Containing Hybrid Sol-Gel Coatings on AA2024, Progress in Organic Coatings 2008 , 62 (2), 226-235.
10 Martin, H.; Horstemeyer, M.; Wang, P. Comparison of Corrosion Pitting under Immersion and Salt-Spray Environments on an as-cast AE44 Magnesium Alloy, Corrosion Science 2010 , 52 (11), 3624-3638.
11 Chen, Y.; Tzeng, H.; Wei, L.; Wang, L.; Oung, J.; Shih, H. Corrosion Resistance and Mechanical Properties of Low-Alloy Steels Under Atmospheric Conditions, Corrosion Science 2005 , 47 (4), 1001-1021.
12 Masuda, H. Atmospheric Corrosion of Low Alloy Steels in a High-humidity Seashore Environment, Local Probe Techniques for Corrosion Research 2007, 137-144.
13 Howarter, J.; Youngblood, J. Optimization of Silica Silanization by 3-aminopropyl Triethoxysilane, Langmuir 2006 , 22, 11142-11147.
14 Bierwagen, G.; Tallman, D.; Li, J.; He, L.; and Jeffcoate, C. EIS Studies of Coated Metals in Accelerated Exposure, Progress in Organic Coatings 2003 , 46 (2), 149-158.
15 Sharer, Z.; Sykes, J. Insights into Protection Mechanisms of Organic Coatings from Thermal Testing with EIS, Progress in Organic Coatings 2012 , 74 (2), 405-409.
16 Chico, B.; Galvan, J.C.; de la Fuente, D.; Morcillo, M. Electrochemical Impedance Spectroscopy Study of the Effect of Curing Time on the Early Barrier Properties of Silane Systems Applied on Steel Substrates, Progress in Organic Coatings 2007 , 60 (1), 45-53.
17 Gray, L.; Appleman, B. EIS: Electrochemical Impedance Spectroscopy A Tool to Predict Remaining Coating Life, Journal of Protective Coatings & Linings 2003 , 66.
Looking for a reprint of this article?
From high-res PDFs to custom plaques, order your copy today!