Bio-Fouling/Hull Efficiency: Dilemma for the 21st Century
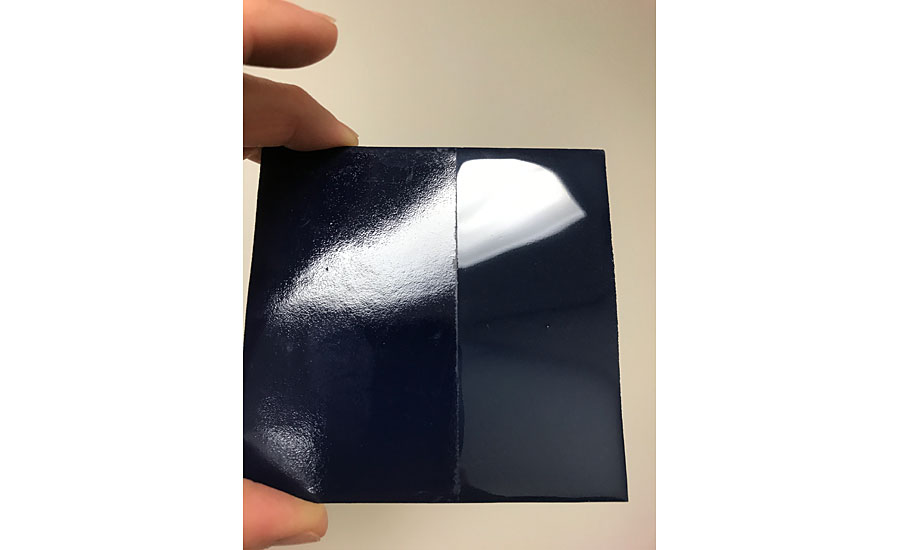
The shipping industry is feeling the increased impact of fouling on the bottom line. Ship owners and fleet managers are under growing pressure to improve operational performance and profitability while trying to comply with increasingly stricter environmental regulations and limitations in the forthcoming decade. Many countries in Europe, as well as Australia, NZ, Canada, Scandinavia and states in the U.S. are leading the way.
According to the Clean Shipping Coalition, fouled hulls cost the shipping industry upwards of $30 billion per year in aggregate and countless tonnes of excess carbon emissions being discharged in our atmosphere. The impact of bio-fouling on ship fuel consumption and emissions has and will continue to come under global scrutiny.
The maritime industry has traditionally employed reactive hull cleaning to maintain clean hulls and control invasive species distribution. Due to the new IMO bio-fouling management protocols and a global focus on the ecosystems, the industry is transitioning to a more preemptive approach to control the fouling development. Hull cleaning companies are developing new techniques and solutions to remove fouling and mitigate the invasive species distribution. These new solutions also must extract the toxic hull paint and biocides from the water stream before it is re-introduced into the oceans. These new systems add additional costs to the process.
Some in the maritime industry say its more about hull performance than coatings. The answer of keeping a ship’s hull continuously clean and efficient is as difficult as the task of bio-fouling management for two main reasons: 1. There is great variation in vessel design, operating profile and trading routes. 2. Existing toxic SPC and CDP coatings will be phased out in the coming decade due to the impact on the ecosystems and lack of sustainable hull efficiency over their respective lifecycles.
New emerging technologies such as hull air lubrication and ultrasonic devices are coming into play in some sectors.
New Technology
Innovation for the future has arrived. This key innovation helps to address the aforementioned major operational/environmental issues pointed out. Seacoat has long been at the forefront in developing sustainable solutions that address the problem from the ship owners’ perspective and exceeds requirements/expectations of port/regulatory authorities globally. Seacoat’s newest hull coating release, SEA-SPEED V 10 X ULTRA, helps curb marine organism fouling on the front end and makes any hull cleaning operations much easier and less expensive than conventional hull coatings, all with zero negative environmental impact due to its non-toxic chemistry on the back end of the equation.
SEA-SPEED V 10 X ULTRA CLEAR is a clear, thin-film coating that utilizes fouling release technology rather than cuprous oxide and or biocidal toxins. We have also incorporated our proprietary VMT (Valence modification technology), thereby making the surface less attractive for biofilm and organisms under operating conditions.
It is comprised of a proprietary silane – siloxane base with a nano component that cures to an extremely hard glass, smooth finish. It is exceptionally abrasion and impact resistant, while remaining flexible. The photo below shows the SEA-SPEED V 10 X UC on a Q panel that has been bent 90 degrees without any cracking, peeling or chipping. The test panel was cured 7 days at ambient temperature and post cured at 250 °F for 72 hours. The surface is glassy smooth (Less than 5 microns surface roughness per IMG 5534 attached) and provides a non- stick, easy-clean surface.

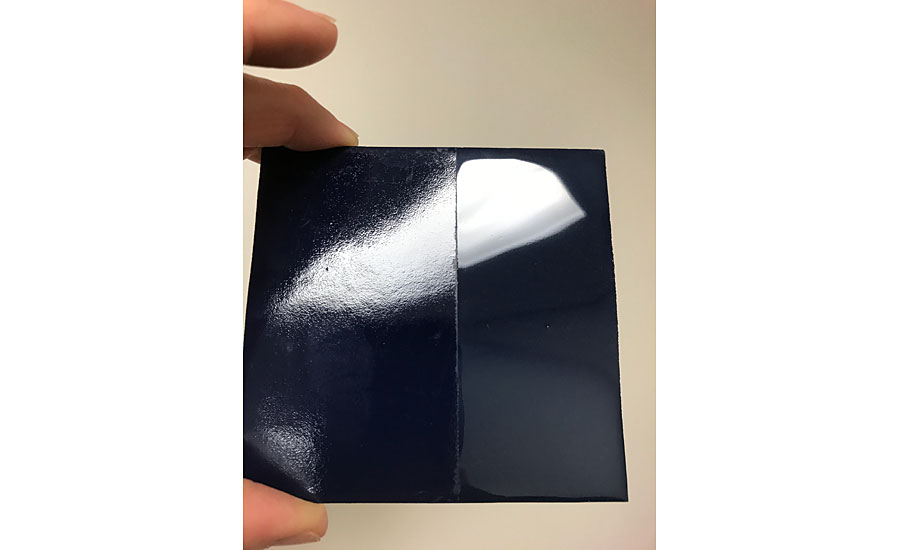
Originally designed for the leisure craft market, the technology is finding its way into commercial marine for all types of vessels due to the improved hull efficiency, 10-15 year lifecycle, durability and the fact it is 100 % non-toxic.
Results
The bottom left quadrant was wiped at 3 months. The top left quadrant was inspected at the six-month mark and was cleaned completely when these photos were taken. They are labeled A, B and C for before, during and after wiping with a fingertip.



The following photo is also a six- month inspection from another location approximately 4,000 miles from the previous location. Both locations are in the moderate fouling category. This was cleaned with one swipe of a sponge.

This last set of photos are also a six-month inspection but from a very aggressive fouling environment in the Coral Sea. Roughly 10,000 miles from the other test sites. A is upon retrieval and B is after a finger wipe. All the panels have been static immersion for 180 days From June 1 – December 1 of 2019.


Hull and propeller performance go hand in hand with coatings. The ability to maintain a clean hull is highly dependent on vessel design, operating profile and trading routes. The coating system is an integral part of the equation. The variables change constantly based on management options and the state of global economic conditions whether they are up or down. The long-term variable in the equation is the choice of hull coating system that the ship owner must live with for 3-5 years without changing. Dr. V. Bertram of DNVGL is correct in stating that yesterday’s recipe will not work in the future. Non-biocidal technologies are a must! Mechanical systems such as hull air lubrication are very costly to install, operate and maintain. Ultrasonic devices have merit but need to be compatible with the proper type of hull coating to yield long-term (>5 years) efficacy.
Coatings based on new chemistry types that deliver more in terms of improved hull performance, operational and maintenance savings and are truly sustainable for ten to 15 year lifecycles are required in the maritime industry. Seacoat’s new ULTRA technology is the only solution that meets these challenges now and for the foreseeable future. ULTRA performance at a lower lifecycle cost than what ship owners are paying today, whether you own a pleasure boat or a fleet of commercial ships.
For more information, visit www.seacoat.com.
Looking for a reprint of this article?
From high-res PDFs to custom plaques, order your copy today!