Novel Approaches to Improve Scratch and Abrasion Resistance in UV Coatings

Prefer the magazine experience? Subscribe to our digital edition here.
As UV coatings continue to be applied to a broader range of substrates, the demand for scratch and abrasion resistance continues to grow. This is especially true with thin-film applications over flexible, semi-porous or hard substrates with varying types of gloss or haptic properties. There are a variety of ways in which damage can occur due to various geometries and forces of the objects scraping over the coating surfaces. There are many factors, such as resin composition, surface uniformity and irregularities, etc., that will influence the scratch and abrasion resistance performance of the coating. Different test methods highlight different aspects of a coating’s integrity, and often there is not consensus across test methods in regards to consistent performance. All these variables combined can result in a wide performance response from slight deformation, which may not be visually observable, to fractal failure of the polymer itself that leaves visually apparent damages.
To obtain continual improvements in scratch- and abrasion-resistant coatings, a variety of additive technologies have been developed to address this issue. In this study, the article examines additive technologies ranging from surface-active siloxanes and nanocomposite technology to synthetic amorphous silica and co-binders. These technologies are then evaluated side-by-side in a urethane UV-curable coating. The study will look at compatibility of these products in the coating formulation and provide relative ratings of their impact on scratch resistance. The scratch and abrasion resistance are measured using several common test methods. The results will provide a comparable overview of how these various technologies perform in improving scratch and abrasion resistance of the UV coating, and the variations that can occur across testing methods.
Additive Technologies
Surface slip agents can markedly lower the damage to a coating by increasing its surface slip. These additives allow objects to slip off rather than penetrate the coating matrix. They affect the surface tension of the coating, resulting in a smoother/higher slip surface, with an improved capability to deflect force across the surface, avoiding a scratch. These additives are surface-active siloxanes that exhibit weak interactions with each other and with other materials. The modified polysiloxanes migrate to the surface of the coating during cure, reducing the slip resistance of the cured film and making it possible for solid objects scraping across the surface to slide easier. The general structure of these additives is illustrated in Figure 1.
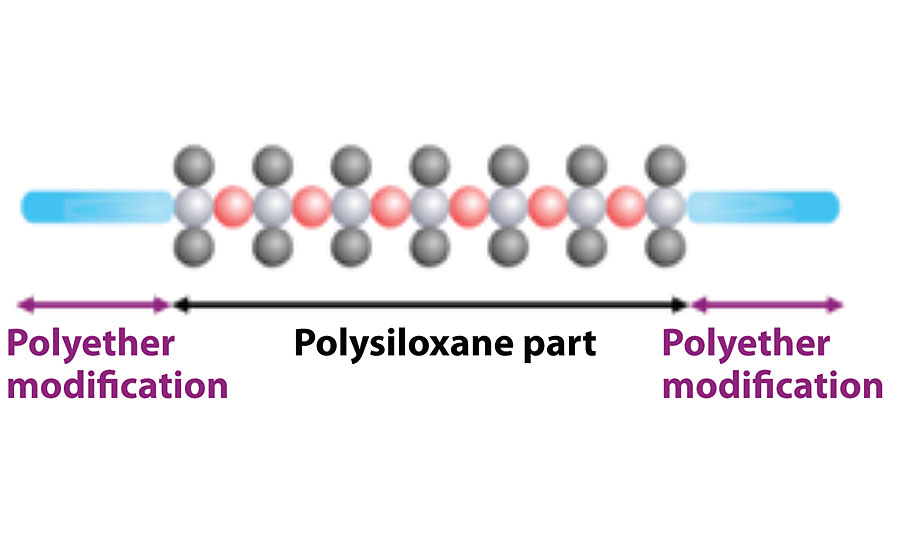
These slip agents can by modified with hydrophilic-hydrophobic polyether to control its compatibility in the coating and the behavior of the polysiloxanes. Other functionalities in the chemistry of the slip agent help with anti-cratering effects, and these liquid-based technologies can be formulated for varying ranges of recoatability.
Synthetic, amorphous silicas are produced with varying wet and high-
temperature-based processes that yield similar chemical compositions but significantly different particle types and morphologies, with a wide range of physical-chemical properties. The three types of silica used in this study are shown relative to the overall synthetic amorphous silica market in Figure 2. Fumed silica is derived from a high-temperature process. Whereas, both precipitated and colloidal silica are derived from a wet process.

A typical function for most amorphous silica is to improve the overall hardness and reinforcement of the coating. Structure-modified fumed silica is manufactured using the high-temperature flame hydrolysis that produces primary particles that are irreversibly fused to form sub-micron aggregates. These aggregates are then processed to form structure-modified particles. The wet process produces precipitated and colloidal silica. The precipitated silica is a unique, spherical particle that differs from conventional precipitated silica. The colloidal silica is functionalized to provide better compatibility in coating formulations while maintaining excellent dispersion stability in water. The colloidal silica in water is designated nanocomposites in this study.
Fumed silica TEM photos in Figure 3 show the conventional structure of fumed silica on the left and the structure-modified fumed silica on the right. This silica has higher bulk density and more compact structure, allowing for higher loading level without adversely affecting viscosity.

Figure 4 shows a new spherical precipitated silica in the center surrounded by TEM images of other conventional precipitated silica, as well as other similar products on the market such as natural ground silica, diatomaceous silica and synthetic microspheres. The particle porosity and sphericity of the novel precipitated silica is controlled by the manufacturing process, resulting in linseed oil absorption of 40 mL/100 g silica and BET surface area of <15 m 2 /g.
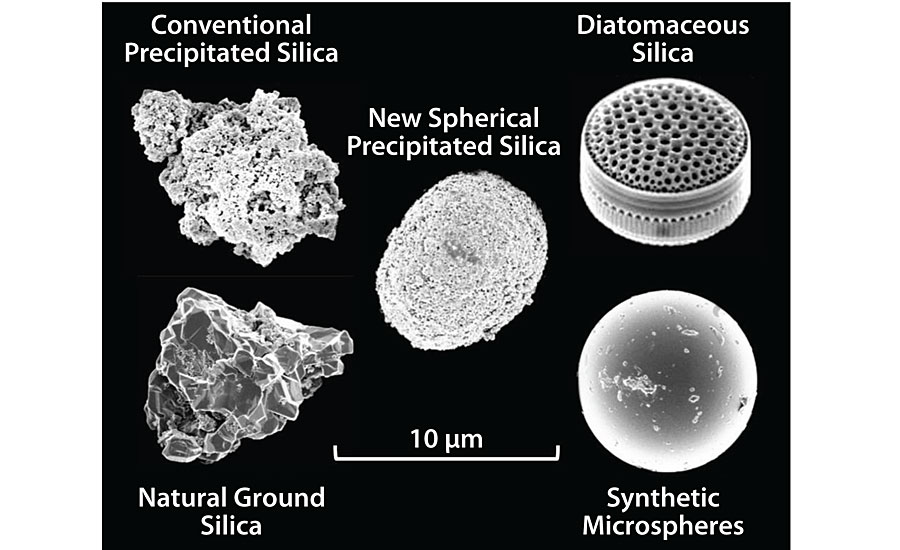
The nanocomposites are aqueous dispersions of colloidal silica. Like the fumed and precipitated silica, the colloidal silica improves the overall hardness of the coating while providing improved mechanical properties among other attributes, and due to its very small size, achieves very high clarity. Figure 5 is an example of mono-dispersed, discrete silica nano-particles of 20 nm distributed uniformly throughout a cured film. These particles are functionalized and stabilized in the aqueous dispersion. For UV-curable systems, dispersions in various monomers are also available. Particle-based dispersions in solvent and water are also available.

The last group of property enhancers are co-binders that can improve the overall hardness of the coating by increasing the overall glass transition temperature (Tg) when combined with the main resins in the final coating. Here, two co-binders are included – a high-Tg polyester and high-Tg ketone resin, shown in Figure 6. The Tg of both the polyester and ketone resin co-binders are at 90 °C.

Test Formulation
The test formulation is shown in Table 1. The additives were added at 0.1-10.0% on formulation. The silica content was added at 10.0% above the total formulation.

Sample Preparations
Wet samples were prepared by weighing 100 grams of test formulation into a beaker, then incorporating various levels of the additives, then mixing for 3 min at 1,000 rpm using a 30-mm diameter dissolver blade. These samples were then applied on different substrates and cured using UV light at a speed of 20 m/min.
Testing Methods
The scratch and abrasion resistance were tested using various methods listed in Table 2.

Results and Discussion
The additives from each of the technology areas chosen for this study are listed in Table 3. When the additives are added and mixed into the formulation, its compatibility to the system is checked.

Some of the additives were incompatible and flocculated in the beaker after a short time. Others showed incompatibility at lower concentrations but incorporated uniformly at higher concentrations. Finally, some resulted in an inflexible film at higher concentrations that cracked and could not be used for testing. Some examples of these are shown in Figure 7.

The formulation for this study was not fully optimized to take into consideration some of the incompatibility or concentration effects. A summary of the test results are listed in Table 4.

In general, the slip additives and co-binders had good compatibility, with the exception of Slip 500 at lower concentrations. The slip additives are surface-active agents, therefore only low dosages are needed. The structure-modified fumed silica (SMF silica) showed incompatibility due to the need to grind these particles in a high-energy mill and pre-stabilized before addition into a coating formulation. Therefore, we were unable to obtain any results with this material in this study. Finally, in regards to the nanocomposites, at higher concentrations some of these property enhancers resulted in inflexible films that could not be used in measuring their scratch and abrasion resistance.
Since the structure-modified fumed silica (SMF silica) was incompatible, it is left out in the following analysis. The remaining blanks in the graphs are because the measurements could not be obtained from the coating applied.
Martens hardness in Figure 8 shows that some additives can reduce the hardness of the coating. This was especially true of the co-binders. The nanocomposites did not form films that were acceptable for measurements, except for the NC 153. However, even this reduced the MH of the coating. Here, the best performance was seen with the Slip 496, where at 0.1%, results were better than the blank coating itself.

The Martindale abrasion test (Figure 9) also showed the best performance was with the slip agents, where both the Slip 410 and 496 both performed well. Here the co-binders gave good performance at the higher loading levels. Of the nanocomposites, the NC 153 had more consistent performance.

When we look at the Crockmeter abrasion results at both 20° and 60° gloss in Figure 10 and Figure 11, the nanocomposites showed best performance, followed closely with Slip 496.


In the TABER® Shear test shown in Figure 12, the slip agents allow for higher weight on the shear arm before it begins to scratch the coating. Here, the best performance is shown with the slip agents, specifically the Slip 410 providing the best performance. Among the nanocomposites, the NC 153 had the best performance.

Finally, when the additive’s impact is evaluated using the TABER abrader test, the best performance is between the Slip 496 and the nanocomposite NC 153, as shown in Figure 13 on the next page.

If we consider lowest dosage for slip additives, due to their surface activity and highest dosage for the silica and nanocomposites, their impact on the coating can be summarized in Figure 14 on the next page.

From these results, the slip additives generally performed best across these tests in this UV-curable coating formulation. The Slip 496 was the best performer among the slip additives. Following the slip additives is the nanocomposite technology, of which the NC 153 offered the best performance.
As stated, this study was to provide an overview of the comparable technologies. However, further developments would be necessary to optimize formulation and incorporation of the various technologies to provide definitive results on performance.
Conclusions
The study provides an overview of comparable technologies to improve scratch and abrasion of UV-curable coatings. The results showed that slip additives perform best in this study, with the Slip 496 giving the best overall performance. Following the slip additives would be the nanocomposites, of which NC 153 had the best performance.
This study also demonstrates that scratch resistance performance can vary significantly depending on which method is used, and often there is not a common improved performance across each and every scratch test.
Further work would be needed to examine the incorporation of additives such as the novel precipitated spherical silica, or the structure-modified fumed silica. In addition, there is a need to optimize nanocomposites to obtain best compatibility and performance.
Acknowledgement
Special thanks to Mr. Marco Heuer, Mr. Roger Reinartz and Ms. Aline Skotarczak for their work in this study.
References
1. Evonik Report PLO2018-03 - Scratch-Resistance UV-System by Mr. Reinartz and Ms. Skotarczak.
2. “Testing of Scratch and Abrasion Resistance of Coating Systems for Permanent Protection of Plastics and Other Substrates” by M. Heuer, A. Skotarczak, M. Schaepermeier, R. Reinartz, and F. Eichenberger; presented January 2020.
For more information, e-mail Bob.Lin@evonik.com.
Looking for a reprint of this article?
From high-res PDFs to custom plaques, order your copy today!