Monitoring Paint Curing Oven Temperature
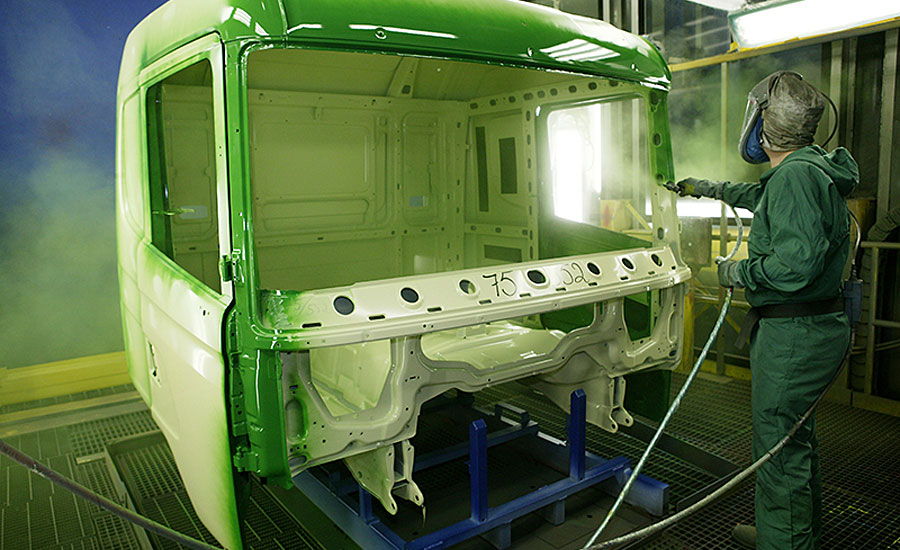
CAS DataLoggers supplied a temperature monitoring solution for an industrial paint curing oven used by a manufacturer of commercial snow removal equipment. This customer was experiencing periodic problems with the quality of their powder-coated parts. Their manufacturing line was designed to be flexible enough to allow for a mix of snowplows, plow frames, frame brackets and other parts to be processed on the same line. A single conveyor moved the parts through a pre-treatment area, a quick changeover coating booth, and then on through the paint curing oven and cooling area. However, in some cases, the finished parts appeared dull, and the company was also experiencing a high rate of field failures where the coatings would peel and flake. All signs indicated that these failures were related to incorrect curing of the powder-coated parts even though a spot check of the paint curing oven indicated that both temperature and time in the oven were within the coating manufacturer’s recommendations. An industrial oven temperature recorder was required to make a more detailed analysis and identify the problem, so management began searching for a complete through process paint curing oven temperature profiling system that was durable, had the appropriate probes and user-friendly data analysis software designed for paint and powder coating application.
Installation
The customer chose a Grant OMK610 Oven Data Logger Kit to perform a more detailed temperature profile of the paint oven and the curing process. The kit included a compact oven temperature data logger along with a stainless steel thermal barrier capable of protecting the data logger at temperatures up to 250 °C (482 °F) for as long as 50 minutes. An optional phase change insert which, when added to the barrier, allowed extended operation at the rated temperature to a full 100 minutes. The six-channel data logger supported standard Type-K thermocouple probes and could sample up to eight time per second to capture even the most rapid temperature change. It also had the ability to store up to 250,000 readings more than enough to capture data from several trips through the paint curing oven. The logger was equipped with a USB communications interface to connect to a PC for setup and download of stored data. A variety of probes, specifically designed for paint and powder coat applications, including models for surface and air temperature with magnetic or clamp attachments could be included in the kit.
Usage
Additionally, the Grant OMK610 oven logger kit included the PaintView setup and data analysis software, a Windows-based software package designed specifically for paint and powder coating applications. PaintView enabled storage of preprogrammed cure data curves and display of calculated cure percentages. It also allowed easy setup and download of recorded data from the logger into a time vs. temperature chart. The paint cure calculation offered a choice of methods between the Grant ‘classic’ cure or area integration cure analysis methods. A database could be built containing different cure curves for multiple paint types from various paint manufacturer. PaintView also provided rapid interpretation of results for advanced paint cure calculations and gave users graphic analysis of historical data along with advanced reporting. Users could easily view and control the logger status from one single screen and save all settings for reuse. Downloaded data exported into Excel™ or as a CSV file for customizable data analysis.
To troubleshoot their paint curing issues, the customer used the kit to monitor multiple batches of different types of parts as they were sent through the curing oven. Once all the data had been collected, a graph of the part temperature against time in the oven immediately revealed the problem: the large moldboards, which had a high thermal mass, had not been in the oven long enough to completely cure the coating, resulting in the dull parts. Also, smaller parts with a lower thermal mass were being over-cured, exceeding the powder coating temperature limit, resulting in coatings that peeled and failed prematurely. The solution was to process the parts in groups so that conveyor speed could be adjusted to get the optimal cure rate based on the mass of the product and the information collected from the data logger for each type of part, entirely alleviating the problem.
Benefits
Using the data collected with the OMK610 kit, the manufacturer’s was able to immediately correct the production of dull parts and high field failure rates, having identified the underlying curing problems. Additionally, the oven temperature profiling system assisted in production quality control and led to lower operating costs, providing everything needed for paint oven temperature profiling and paint cure calculations in one easy to use and convenient kit. The manufacturer consistently met the specified powder coating cure temperature parameters and maintained a specified level of cure to ensure repeatable quality and maximize oven usage and throughput.
For more information, visit www.DataLoggerInc.com.
By CAS DataLoggers
Looking for a reprint of this article?
From high-res PDFs to custom plaques, order your copy today!