Optimized Processing to Reduce Crystalline Silica in Ground Calcium Carbonate

Over the past several years, there has been a murmur in the coatings industry with regards to the concentration and levels of crystalline silica within various paint formulations, particularly architectural coatings. While there are countless architectural coating formulations, commonly the largest component on a volume basis is calcium carbonate. The combination of the regulatory focus on crystalline silica, in conjunction with the impact calcium carbonate can have on a formulation’s crystalline silica levels, inspired Imerys to both re-evaluate and optimize the processing of calcium carbonate to support paint formulators to continue to drive down the crystalline silica levels in their products.
Before a deep dive into the optimization process, it is important to understand the differences between crystalline silica and “respirable” crystalline silica, as well as the dangers posed to both employees and consumers from respirable crystalline silica. Crystalline silica (Figure 1) is a basic component of sand, soil and other minerals, and comes in three forms - cristobalite, tridymite and quartz - with quartz being the most common. The primary EHS concern with crystalline silica arises when small particles (typically less than 10 micron) are strewn into the air and become inhaled by either production workers or consumers. Some activities that can cause crystalline silica to become respirable include manufacturing of paints, pouring/handling powders, abrasive blasting, sanding of joint compound, sanding paints, manufacturing brinks and hydraulic fracturing.

Breathing crystalline silica dust can cause silicosis, which in severe cases can be debilitating or even fatal. The respirable silica dust enters the lungs and causes the formation of scar tissue, reducing the lungs’ ability to take in oxygen. There is no cure for silicosis, and since silicosis affects lung function, it makes one more susceptible to lung infections like tuberculosis. Crystalline silica regulations are governed by OSHA 29 CFR 1910.1053, which was upgraded in 2016 to set the Permissible Exposure Limit (PEL) of 50 µg/m 3 averaged over an eight-hour day.
How Crystalline Silica is Processed
Now that potential risks have been identified with inhaling respirable crystalline silica, the question becomes, “How can these risks be reduced during the processing and handling of calcium carbonate?” To best understand the optimized process identified by Imerys, a basic understanding of the process from mine to plant is necessary.
The mining process begins with a mining plan, using core samples that are extracted and undergo various testing, including CaCO 3 concentration, color, quartz levels and other analytical testing. Once the core samples have been extracted, a 3D model (Figure 2) of the mineral deposit is built, which enables the mine planners and engineers to plan the best way to extract the minerals to achieve the desired properties. Identifying parts of the mineral deposit with low quartz concentrations to begin with theoretically reduces the amount of respirable particles that can be generated during processing.
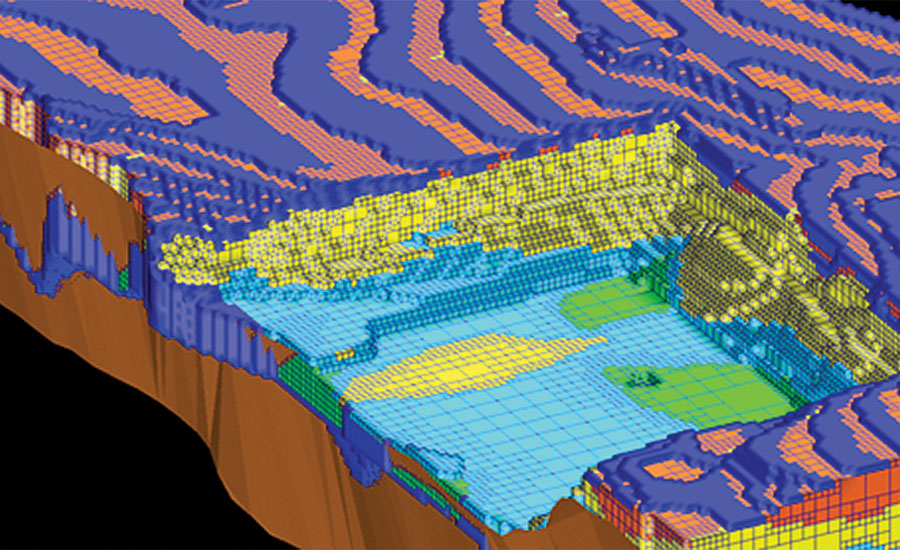
The next two steps of the process are washing and optical sorting. It is here where the mineral ore is rinsed of impurities and dust that may have collected up to that point. Both washing and optical sorting help to both improve the quality and color of the product feed. Various grinding and milling then takes place.
The final and most influential step in the mineral process to help enable the reduction of crystalline silica in calcium carbonate products is flotation. Flotation is a mineral separation process that takes place in a water/mineral slurry. In the flotation process, chemical reagents are introduced to the water/mineral slurry, in addition to agitation, used to promote interactions between the hydrophobic particles and air bubbles in order to achieve separation of mineral particles. The chemical reagents attach themselves to impurities exposed, in this case quartz, on the surface of the mineral particles to help drive these particles to the surface. The froth, which is now dense in particles containing impurities, is removed from the surface of the flotation cell.
There are several types of mineral flotation technologies and chemical reagents available on the market, including mechanical flotation cells (Figure 3), flotation columns and pneumatic flotation cells. Each technology has pros and cons, although the most adapted technology for calcium carbonate is mechanical flotation.

Optimized Processing
Through years of mineral processing know-how, Imerys has been able to optimize the calcium carbonate processing at each step of the mine-to-plant process to enable the reduction of crystalline silica in the final products. Within the floatation process, a proprietary method has been developed to optimize both the type and concentration of the chemical reagents, additional additives and level of agitation to push the industry forward in offering low total crystalline silica products. This optimization has proven to reduce the total crystalline silica in the ore feed by as much as 90%.
In working with third-party verification labs, it has been possible to introduce products to the market that have an undetectable level of total crystalline silica (below 0.1%). Third-party testing of total crystalline silica is done using both X-ray diffraction and computer-controlled scanning electron microscopy.
This new line of calcium carbonate products, which can be surface treated if needed, and called XCS-Carb, allows coatings formulators to increase the carbonate loading levels in their formulation without the concern of increasing the crystalline silica concentration in their final formulation. It is important to note that the data on optimized processing demonstrates a reduction in the concentration of total crystalline silica, but the exact amount of respirable crystalline silica workers may be exposed to is unique to each work environment, and all individuals with regular exposure to respirable powders are encouraged to use all necessary personal protective equipment.
Data has also shown that reducing total crystalline silica not only increases individual safety, but also reduces the wear and tear on processing equipment at paint facilities. While calcium carbonate has a Mohs hardness of 3, quartz has a hardness of 7. By being able to reduce the concentration of these harder impurities, all the piping equipment, silos and mixers will no longer be exposed to the damage these hard particles can cause.
The introduction of these products, and the internal initiatives within Imerys to optimize the calcium carbonate processing to reduce the levels of total crystalline silica, demonstrate the organization’s commitment to corporate social responsibility and maintain the push to continue to introduce both sustainable and safer products to market.
Looking for a reprint of this article?
From high-res PDFs to custom plaques, order your copy today!