A Study of How CNSL Blends Affect Coating Properties
Synthesis and Studies of Corrosion-Resistant, Low-Cost, Water-Based Coatings for Steel Surfaces

Water-based coatings have been in use for decades, as they eliminate or reduce the use of petroleum-based solvents, which increase levels of VOCs, toxic substances and energy consumption. The coatings industry is focusing on four major techniques in the area of eco-friendly technologies: water-soluble, powder, radiation-curable and high-solids coatings. 1 In this regard, aqueous, cashew nut shell liquid (CNSL)-based coatings have received increased attention because of the availability of agro-based CNSL.
The CNSL constituents have two reactive units: phenolic OH, which is the hydrophilic part of the molecules, and the long C-15 side chain having an average of two double bonds (i.e., the hydrophobic part that contributes to crosslinking and gives gradual and satisfactory drying and baking properties). 2 The long hydrocarbon chain imparts great flexibility to its aldehyde condensate in the various drying oils. CNSL exhibits the following unique properties: agro-based, excellent water resistance, corrosion resistance, satisfactory chemical resistance, better flexibility and drying than other oils, very cheap, sufficient reactive sites.
In spite of having these properties, CNSL also suffers from some drawbacks like lack of hardness, lack of toughness and poor adhesion. These problems can be overcome by modifying CNSL with epoxy resins, which impart adhesion, toughness, improved film hardness and resistance to chemicals. 3 Currently, blending aims at securing sets of specific properties required for an envisaged application. This present study assessed the advantages of blending CNSL with maleinized epoxy ester resins with respect to coating properties, especially corrosion resistance, humidity and blistering.
Materials and Methods
Materials Used
The basic raw materials/chemicals used in this research included the following:
- Cashew nut shell liquid. Lovibond ® color tintometer values: R=10, Y=14, B=3.9; specific gravity at 30 °C: 0.96; iodine value (wijs): 210; refractive index at 30 °C: 1.51; viscosity at 30 °C (by Ford cup viscometer no. 4): 47 sec.
- Rice bran oil fatty acids. Lovibond color tintometer values: R=5, Y=3; acid value: 177 mg KOH/g; iodine value (wijs): 90; refractive index at 32 °C: 1.46; viscosity at 30 °C (by Ford cup viscometer no. 4): 55 sec.
- Epichlorohydrin LR. MW: 92.53%, assay (ex cl): 98%, boiling range: 114 to 118 °C, wt. per mL at 20 °C: 1.180-1.183 g.; S D Fine-Chem Ltd.
- Bisphenol A. LR. MW: 228.29; MP: 153 °C; Indian Drugs & Pharmaceuticals Ltd.
- Maleic anhydride. MW: 98.06%; minimum assay (acidimetric): 97%; MP: 52-55 °C; S D Fine-Chem Ltd.
- Ethyl alcohol. MW: 46; bp: 78 to 79 °C, distilled in the laboratory.
- Phenolphthalein LR. MW: 318.33, pH range: 8.3 to 10.0; MP: 258 to 261 °C; BDH Chemicals.
- Potassium hydrogen phthalate. minimum assay: 99.9%; MW: 204; Ranbaxy Laboratories.
- Potassium hydroxide, LR. MW: 56.11; minimum assay: 85.0%; Ranbaxy Laboratories.
- Sodium thiosulphate. MW: 248.18, minimum assay: 99%; Qualigens Fine Chemicals.
- Sodium hydroxide, Pellets, LR. MW: 40.00; minimum assay: 96.0%; Samir Tech-Chem.
- Starch. S D Fine-Chem Ltd.
- Triethyl amine. MW: 101.19; assay: 98-101%: wt. per mL at 20 °C: 0.726-0.728; Qualigens Fine Chemicals.
Methods Employed
A number of techniques were employed for the analysis of raw materials and synthesized maleinized rice bran fatty acids.
Color
Color was determined by Lovibond tintometer 4 using 1/4” Lovibond cell. The color of the sample was reported using the following relationship:
Color reading (1/4”cell) = ( aY + 5bR)
Where a = the sum total of the various yellow (Y) slides used, and b = the sum total of the various red (R) slides used.
Refractive Index
The refractive index of samples was determined 4 by using an Abbe refractometer. It was calculated at the desired temperature as given below:
R = R’ + K (T’- T)
Where R’ = the reading of the refractometer reduced to the specific temperature, T C, K = constant 0.000365 for fats, and T = the specified temperature.
Acid Value
0.1-0.2 g of sample was weighed in a 250 mL conical flask. To this, 100 mL of ethanol 4 was added in a sample of oil, shaken and warmed if necessary to dissolve, and then this solution was titrated against a standard solution of potassium hydroxide to the pink end point using phenolphthalein as indicator. The acid value was calculated as given below:
Acid value = 56.1V N/w
Where, V = volume in mL of standard alcoholic potassium hydroxide solution used, N = normality of standard potassium hydroxide solution, and w = weight in grams of the material taken for the test.
Iodine Value
The iodine value (wijs) was calculated as: 5
Iodine value = 12.69 (B-S) N/w
Where B = volume in mL of standard sodium thiosulphate solution required for the blank, S = volume in mL of standard sodium thiosulphate solution required for the sample, N = normality of the standard sodium thiosulphate solution, and w = weight in grams of the material taken for the text.
Unreacted Maleic Anhydride Content
The maleic anhydride content was determined 6 by titrating the material with standard sodium hydroxide solution using phenolphthalein as indicator and deducting the maleic anhydride content equivalent to maleic acid content.
Reagent:
1. Potassium hydrogen phthalate (previously dried for 2 hrs at 120 C).
2. Phenolphthalein indicator (0.1 gram per 100 mL ethanol).
3. Standard sodium hydroxide solution (0.5 N) standardized as follows: 4 grams of potassium hydrogen phthalate were weighed and transferred to a 500 mL conical flask. To this, 120 mL of water was added to dissolve by warming on a water bath and titrated hot with standard sodium hydroxide solution (0.5N) to the first pink color using phenolphthalein as indicator. The factor F for 0.5 N standard solution is:
F = M1 / (0.2042xV1)
Where M1 = mass in grams of potassium hydrogen phthalate, and V1 = volume in ml of standard sodium hydroxide solution.
1 gram of sample was weighed accurately into a 250-mL conical flask. To this, 35 mL of standard sodium hydroxide solution from a burette and 35 mL of water was added and warmed gently to dissolve the sample. Then this solution was completely neutralized with standard sodium hydroxide solution using phenolphthalein as an indicator until the pink color was obtained.
Calculation:
Unreacted maleic anhydride content = 4.902 V x F/ M - 0.845A
Where V = volume in mL of standard sodium hydroxide solution, F = Factor for standard sodium hydroxide solution, A = Maleic acid content, present by mass, and M = Mass in grams of the material taken for the test.
Epoxy Equivalent
The term epoxide equivalent (epoxy equivalent per epoxy, WPE) 7 is defined as the weight per resin in grams that contains one gram equivalent of epoxy group.
Reagent:
1. Pyridinium chloride (16 ml. conc. HCl per liter of distilled pyridine).
2. Standardized 0.5 methanolic NaOH (20 g NaOH per liter of methanol).
3. Phenolphthalein indicator (0.1 g per 100 ethanol).
4. Methanol, reagent grade.
The 0.5 g of epoxy resin was placed into a round bottom flask, and 25 mL of pyridinium chloride solution was added. In another 250 mL round bottom flask, 25 mL of pyridinium chloride solution was added, and was used as a blank throughout the procedure. The solution was swirled until all the sample had been dissolved on a magnetic stirrer cum heater. The mixture was refluxed for 25 min in a fitted water condenser, cooled to room temperature, and 50 mL methanol was added through the condenser in both the flasks. The condenser was removed, 12-13 drops of phenolphthalein indicator was added to the solution and both the sample and blank were titrated with 0.5 methanolic sodium hydroxide solution to the pink end point.
Epoxide equivalent = 16 × (wt. of sample)/(B-S) × N × 0.016
Where B = volume of methanolic sodium hydroxide consumed for blank, S = volume of methanolic sodium hydroxide consumed for sample, and N = normality of methanolic sodium hydroxide 0.016 = milliequivalent weight of oxygen in grams.
Fourier Transform Infrared Spectroscopy (FTIR) 8
Fourier Transform Infrared Spectra ( max in cm -1 ) were recorded on a Bruker Vector 22 spectrophotometer. Samples were examined as thin films, obtained by squeezing a drop between a pair of infrared transmitting plates or as solution in solvent that is reasonably transparent to infrared radiation and has good solvating properties.
Experimental
Synthesis of Water-Based CNSL-Modified Resins
The following steps were adopted for the synthesis of water-based CNSL-modified resins.
Step 1: Synthesis of Epoxy Resins
For the synthesis of epoxy resins, a calculated amount of epichlorohydrin and bisphenol were put in a three-necked flask fitted with a reflux condenser, thermometer pocket having thermometer, dropping funnel, Dien-Stark and mechanical stirrer. The reaction mixture was heated to 60 C with gentle stirring and then an aqueous sodium hydroxide solution (20% w/v) was slowly added through the dropping funnel with continuous stirring. Finally, the resin solution was distilled off under reduced pressure to get a transparent form of epoxy resin.
Step 2: Synthesis of Maleinized Fatty Acids
A weighed quantity of RBO fatty acid was put in a three-neck round bottom flask, fitted with a thermometer pocket having thermometer, mechanical stirrer and water condenser. It was heated to 90 C with constant stirring. The 8% of maleic anhydride was added slowly within 20-30 min. After the complete addition of maleic anhydride, the temperature was raised to 200-210 C. The temperature was maintained until the desired acid value was obtained and hydration was carried out by boiling maleinized fatty acids in water for about 1 hr. The excess unreacted water was then distilled off under reduced pressure.
Step 3: Synthesis of Maleinized Fatty Acid Epoxy Ester Resins
A weighed quantity of maleinized fatty acids was put in a three-necked flask fitted with a reflux condenser, thermometer pocket having thermometer and mechanical stirrer. The temperature was raised to 100-110 C with continuous stirring. The maleinized fatty acids were reacted with the addition of 30% of epoxy resin at 145 C. The samples were withdrawn from the reaction mixture and the acid value was checked.
Step 4: Synthesis of CNSL-Modified Resins
For the synthesis of water-based CNSL-modified resins, a calculated amount of maleinized fatty acid epoxy ester resins was put in a three-necked round bottom flask. To this, 5 to 25% of CNSL was added on the basis of maleinized fatty acids at 110-115 C. The samples were withdrawn from the reaction mixture to check the acid value. The co-solvent ethylene glycol monopropyl ether was added at around 80 C to the final resin.
Preparation of Water-Based Coatings and Application of Panels
Resins were neutralized with trimethylamine and solubilized in distilled water to get the desired application viscosity. Surface preparation of the panels was carried out by using Emery paper, xylene, mineral turpentine oil, detergent and water. 9 For the application of panels, appropriate quantities of diluted resins were applied over mild steel and glass panels. The resins were cured at 120 C for 30 min.
Films were also tested against acid resistance, alkali resistance, corrosion scratch test, adhesion and hardness as per standard test methods. For corrosion scratch test, an artificial sea water sample was prepared by dissolving chemicals in 1 liter of water (Table 1).

Corrosion Scratch Test
The 5 cm x 10 cm x 1 mm-thick mild steel panels were degreased, sanded and coated. The coated panels were left for 1 week (7 days) in the laboratory at room temperature for complete curing. They were edged with wax, and one face of each panel was scratched to the substrate with a sharp blade. The panels were exposed to artificial (synthetic) sea water for 400 hrs and washed with distilled water. Dried panels were observed for rusting. The specimens were periodically inspected in order to evaluate rusting and blistering.
Humidity Test
Cold rolled mild steel panels without visible rust were used. One side of the specimen was contaminated using 200 and 700 mg/m 2 of Cl - , SO 4 -2 and NO 3 - . Uncontaminated steel panels were used as controls. Sodium chloride, sodium sulphate and sodium nitrate solutions were prepared by using reagent grades and distilled water. The above prepared coatings were applied, and the coated specimens were left for 1 week in the laboratory at room temperature for complete curing. After, the uncontaminated reverse side of the specimens was protected by a strippable coating. The edges were sealed with wax. The coating was applied at a thickness 50 µm. The exposure times were 100 and 400 hrs.
The specimens were carefully observed during the test for rusting and blistering according to ASTM D610 and D714 specifications, respectively. The under-film corrosion rate was determined gravimetrically by weighing the specimens before the application of the contaminants, and after the test and removal of the coating and corrosion products.
Results and Discussion
The above synthesized products were characterized for their physical and chemical characteristics (Table 2). Apart from these analysis, FTIR spectroscopy was also employed to establish the presence of various groups in the resin backbone. FTIR spectra of epoxy resin (Figure 1) shows the presence of peaks at 913 cm -1 and 830 cm -1 , attributed to the epoxide group. In the FTIR spectra (Figure 2) of maleinized RBO fatty acids, the peaks at 1,786 cm -1 and 1,282 cm -1 confirm the incorporation of an anhydride group. Figure 3 represents the spectra of maleinized fatty acid epoxy ester resin. Peaks at 1,175 cm -1 , 1,121 cm -1 and 1,042 cm -1 are attributed to the ester group, O-C-C stretching and C-C(=O)-O stretching vibration of the ester group respectively.

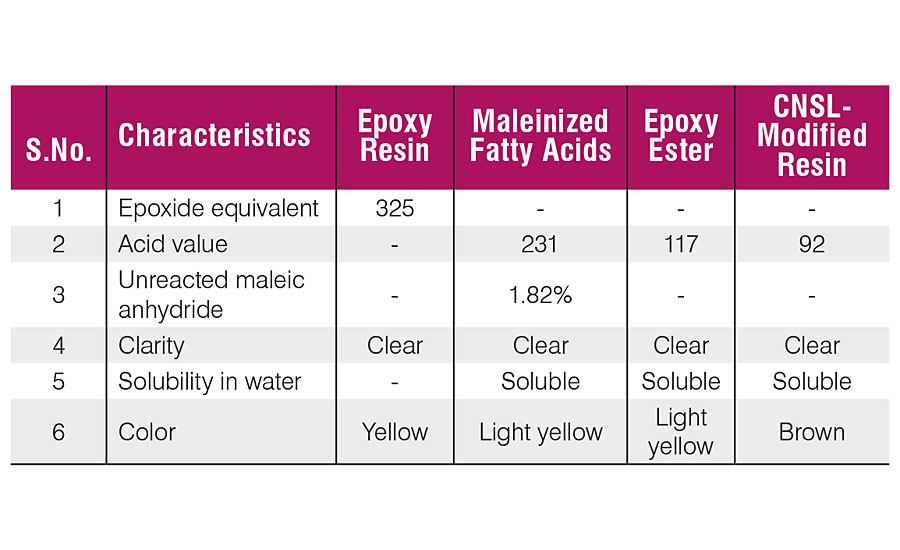


Figure 4 shows the FTIR spectra of CNSL-modified resins, and the increase in intensity at 1,260 cm -1 corresponds to ether linkages. The absence of a peak at 3,352 cm -1 attributed to the phenolic group confirms the formation of ether linkages between CNSL and maleinized fatty acid epoxy ester resin. The peaks at 1,607 cm -1 , 1,508 cm -1 and 1,462 cm -1 indicate the presence of an aromatic ring. Peaks at 1,181 cm -1 indicate ether linkage at resin backbone.

Regarding the solubility in water and clarity of solutions, the CNSL-modified resins are soluble in water and solutions are clear due to sufficient polarity with the resin. The cured samples derived from CNSL-based waterborne resins (Table 3) have been coded as S 1 , S 2 , S 3 , S 4 and S 5 . Films of all the samples appeared glossy, clear, transparent but brownish yellow due to dark brown color of the cashew nut shell liquid.

The laboratory tests for water resistance, acid resistance, alkali resistance, impact resistance, corrosion scratch, flexibility/adhesion and hardness were performed on all the samples of cured resins. The results obtained are summarized in Table 4. All the samples showed good water, acid and alkali resistance. All the samples passed the impact and adhesion test due to the presence of the epoxy group, which is well known for having good adhesion due to polar hydroxyl and epoxide groups. The presence of a sufficient amount of fatty acids and cashew nut shell liquid, which act as internal plasticizer too, results in the reduction in cohesive forces and improvement in adhesion, which combined together impart toughness. None of the samples showed any damage or cracks and passed the test. The corrosion scratch test possessed good corrosion protection. The presence of crosslinking points in maleic anhydride provides better hardness to the film. It was also observed that none of the samples showed any kind of detachment of the film from the substrate. Table 5 depicts the humidity test results after 100 and 400 hrs of exposure. The rating of rusting was done visually and compared with the ASTM D-610 specification and also with the results.


Table 6 shows the blister performance at 100 and 400 hrs. Blistering was rated by visual examination and compared with the ASTM D-714 specification. The under-film corrosion rate was determined by gravimetric method after 100 and 400 hrs and is shown in Table 7.


Tables 5 and 6 show that panels coated with resins having a low percentage of CNSL depict stronger rusting and blistering than those coated with a high percentage of CNSL. The results in Tab. 5 show that the water at the coating-metal interface is the basic culprit in the adhesion failure, and agrees with the literature. The coating acts as a semi-permeable membrane and the contaminant forms the blister as the water permeates through the film and lowers the concentration of contaminants. The coating fails due to the blister.
With reference to the Tables 5, 6 and 7, it can be said that 100 hrs are sufficient for water to permeate through the coating and dissolve the contaminants present at the coating-metal interface, but not enough to produce perforation of the coating as a consequence of water accumulation or the growth of rust. 10 The concentration of contaminants at the interface is prone to under-film corrosion and does not much depend upon the type of contaminants. Under-film corrosion is higher in the low-percentage CNSL coatings than samples having a high percentage of CNSL.
Conclusion
Coatings are economical, and have good resistance to water, acid, alkali, chemicals and corrosion. One of the basic properties of coatings is adhesion and impermeability, which is mainly responsible for other performance properties. Most of the corrosion activities play their role at the coating-substrate interface. The availability of oxygen at the interface depends on the permeability of the coating. The thickness of the coating and chemical structure are the common deciding factor of permeability. A highly polar binder has excellent gas barrier properties and is very sensitive to water permeation, whereas for a non-polar binder the reverse is true. It was found that samples having a higher percentage of CNSL showed excellent corrosion scratch properties, and successfully passed the humidity and blistering tests. Analyzing the overall performance of the films derived from each sample, it may be said that all the samples showed good mechanical, chemical and corrosion resistance, keeping cost in mind. These coatings can be used in the chemical and petroleum industries, building maintenance work, etc.
For more information, e-mail:shikha.deepti12@gmail.com.
References
1 Haseebuddin, S. et al. Paint India, vol. LIX-No. 11, 2009, p-61.
2 Gedam, P.H.; Sampathkumaran, P.S. Progress in Organic Coatings , 1986 ,14, p-115-157.
3 Potter, W.G. Uses of Epoxy Resins, First American Edition, 1976, 24-25.
4 Methods of Sampling and Test for Resins and Paints, 1976, IS-548.
5 Methods of Sampling and Test for Oils and Fats, 1964, IS-548.
6 Specification for Maleic Anhydride, Technical, 1977, IS-5149.
7 Lee, H.; Neville, K., Handbook of Epoxy Resins 4-11, Mc Graw Hill, Inc.,1967, 1-2, 4-17.
8 Silverstein, Robert M.; Bassler, G. Clayton and Morrill, Terence C.1981, Spectroscopic Identification of Organic Compound, John Willey & Sons, Inc., Fourth Edition, 1981, 95-124.
9 Methods of Test for Ready Mixed Paints and Enamels,1964, IS - 101.
10 Morcilloo, M. et al., Progress in Organic Coatings 31, 1997 , p- 245-253.
Acknowledgement
The authors are thankful to the Council of Science and Technology, U.P., Lucknow for providing financial support to conduct this research work.
Looking for a reprint of this article?
From high-res PDFs to custom plaques, order your copy today!