Impact of Traditional vs New Biobased Rust-Preventive Temporary Coatings

Temporary corrosion protection of metal components and surfaces during shipment, storage and/or in between manufacturing processes is critical to a variety of industries worldwide. A common example of this is automotive components, which may require temporary corrosion protection for a few days, weeks or months. Rust-preventative liquids are regularly used to accomplish this task.
When choosing a temporary rust-preventative product, multiple considerations must be made. In addition to effective corrosion protection, the product should provide little to no interference with the function of the metal part or surface, and should also be safe and friendly to the environment and the workers using it. Finally, ease of removal needs to be considered. Traditionally, oil- and solvent-based products have been used for the preservation of metals during shipment, storage or between processes. While these products may offer sufficient corrosion protection, they often contain hazardous ingredients and are not readily biodegradable.1,2 As environmental and disposal regulations become more and more stringent, the desire for “green” corrosion inhibitors is increasing.3 Recently, the use of biobased products, derived from vegetable oils and their esters, has been found to offer equal or better corrosion protection properties, when compared to their petroleum-derived counterparts.2
There are three main requirements of effective temporary rust preventative. First, the substance must bind itself to the metal surface. Second, the rust preventative should provide a barrier against moisture. Finally, the rust preventative should effectively and evenly cover the metal surface. Traditional temporary rust preventatives utilize oils that contain organic compounds such as fatty acids. These compounds form a physical barrier between the metal substrate and the corrosive environment.4 The fatty acid molecules have a long water-repelling hydrocarbon tail and a head that has a strong affinity for the metal surface.5,6 However, over time, moisture will diffuse through the oil layer to the metal surface. To combat this, more recent formulations of rust preventatives will form a layer and prolong the rust protection period. Rust preventatives provide corrosion protection of the metal, while the carrier ensures the efficient spread over the complete metal surface.7
Different approaches can be used to create an environmentally friendly rust preventative system. The most common method is to replace solvent- or oil-based carriers in formulations with water-based technology. The second option is to replace petroleum-based carriers with solvents manufactured from environmentally friendly renewable resources. This has been accomplished by combining vapor corrosion inhibitors (VCIs) with soy-derived and canola oils, creating anticorrosion product formulations for many different applications. The last method is to utilize biodegradable VCI chemistry building blocks in conventional solvent carriers.2
This article will focus on the first approach. Laboratory test results, as well as economic and environmental impact of traditional rust preventatives, will be compared to a novel water/biobased product. The goal of this research is to show that biobased products may inhibit corrosion as well as their traditional oil- and solvent-based counterparts, without any of the negative environmental considerations.
Economical Study
In 2015 an estimated 300,000 tons of rust-preventative fluids were used around the world - comprising approximately 12% of the total market for metalworking fluids. Asia uses about half of the world’s supply of rust preventatives, driven in a large part by the enormous metal parts exporting industry in China. The remainder of the market is split about evenly between the Americas and Europe. European markets, where environmental regulations can be more stringent, use a higher percentage (about 40%) of water-based rust preventatives. Asian markets use solvent-based or oil-based protective fluids almost exclusively. These fluids also dominate in American markets, representing about 80% of market share.8
Table 1 shows economic analysis, taking into consideration the total cost of biobased and solvent-based products that are commercially available, collected from product data sheets.

TABLE 1 » Rust preventative total cost per liter.
The cost analysis is performed according to:
- Market price of the product;
- Disposal cost, based on product classification waste number;
- Transport cost, based on 100 liters of product;
- Warehousing cost.
Economic analysis showed that calculated total cost, including cost per liter, disposal, transportation and warehousing is lowest for rust preventative INH1, and highest for rust preventative INH4. It should be noted that INH1 is biobased, while INH4 is solvent-based. Biobased rust preventative INH1 shows lower total cost compared to four tested solvent-based products (INH2, INH3, INH4, INH5), which makes it stand out as the most cost-effective temporary corrosion protection product, while also being the most environmentally friendly.
Experimental Study
In the experimental study, a series of analyses were conducted to evaluate both biobased and petroleum-based rust preventatives. The first experimental analysis was accelerated corrosion testing using a humidity chamber, in an effort to simulate conditions experienced during transport and shipping. Second, each rust preventative was evaluated for cleanability. Easy removal ensures treated metal components can be quickly used, minimizing downtime and maximizing production output. The last analysis was electrochemical testing by means of polarization techniques, which determines efficiency of corrosion inhibition.
Materials and Sample Preparation
Five types of ready-to-use rust preventatives were evaluated: one biobased that combines film-forming additives with vapor phase corrosion inhibitors (VpCI) and four conventional solvent- and oil-based products, which leave a temporary waxy protective film on metal surfaces. The properties of tested rust preventatives are given in Table 2.

TABLE 2 » Tested rust preventatives with properties taken from product data sheets.
The carbon steel samples, dimensions 60x100x1 mm, were polished with sandpaper (240 grit), immersed in methanol for 5 min, dipped in rust preventatives for 30 min, and then allowed to air dry for 24 hrs before testing.
Humidity Chamber Testing
Humidity chamber testing was conducted according to ISO 6270-2 (modified ASTM D 1748), for a duration of 600 hrs. The goal of this testing is to determine the resistance of different rust preventatives to an atmosphere of constant condensing humidity, RH 100% and 40 ± 3 °C, representing warehouse and/or transport environment. The testing was conducted in a C&W Humidity Cabinet, model AB5. Table 3 shows the film thickness measurement results using gravimetric method of applied rust preventatives after drying. The biggest film thickness around 10 µm was measured for rust preventative INH2, whereas other rust preventatives left much lower film thickness, up to 2 µm.

TABLE 3 » Thickness measurement of rust preventatives.
Cleanability
After the rust-preventative film has served its purpose, it has to be removed, commonly using alkaline degreasing cleaners. Clean removal of the rust preventative is essential to the performance of subsequent processing steps like painting, phosphating or galvanizing, or welding.8 Evaluation of cleanability of rust preventatives was conducted by The Lubrizol Corp. in-house cleaning test. Panels coated with rust preventative are allowed to dry completely, and then immersed halfway in a 5% alkaline cleaning solution for 7.5 min at 45 °C. Afterward, the panels are rinsed with water and dipped into a copper sulphate plating solution. Successful removal of the rust preventative allows for more uniform copper plating on the panel surface. Harder-to-clean rust preventatives show gaps in the plating, indicating that the rust preventative was not well removed by the cleaner.
Electrochemical Study
An electrochemical study of rust preventatives was conducted according to ASTM G-94. Treated samples were immersed in fresh water, for 1 hr and 5 days, respectively, at (23±2) °C. Measurements were carried out in a standard three electrode test cell in relation to the reference saturated calomel electrode (SCE) with known interaction potential of +0,242 V versus standard hydrogen electrode (SHE). Polarization curves were registered after 30 min of exposure to aqueous solution, in order to allow corrosion potential (Ecorr) stabilization. During the potentiodynamic measurements, the working electrode was polarized to the potential of ± 250 mV relative to the corrosion potential and the current response was measured. The inhibitor efficiency was calculated from measured corrosion rate of unprotected and protected carbon steel samples.
Results and Discussion
Resistance to Constant-Humidity Condensation Atmosphere
During and after 600 hrs of humidity chamber testing, the treated panels were evaluated for pass/fail in accordance to ASTM D 1748. The standard states that a test surface shall pass if it contains no more than three dots of corrosion, no one of which is larger than 1 mm in diameter, whereas, a test surface shall fail if it contains one or more dots of rust larger than 1 mm in diameter or if it contains four or more dots of any size. Corrosion occurring within 1/8” from the sides of the panel, or within 1/8” below the hanging holes is not counted. The humidity testing result are given in Figure 1.

FIGURE 1 » Resistance evaluation of different rust preventatives to a constant-humidity condensation atmosphere.
Compared to the petroleum-derived products, the biobased rust preventative showed excellent corrosion protection, after 600 hrs in modified ASTM D 1748 testing. Rust preventative INH2, although thicker, didn’t pass the testing, due to significant localized corrosion observed after 100 hrs of testing in humidity chamber.
Cleanability Evaluation
Cleanability testing was performed to determine the efficiency by which each rust preventative could be removed from a metal surface. A rust-preventative film that is difficult to remove does not necessarily correlate with the best corrosion protection.8 Increased removal time and effort leads to increased cost and lost time. Figure 2 shows an evaluation of cleanability test results. Rust preventatives INH1 and INH4 showed effective cleanability, while rust preventative INH2 showed moderate cleanability. Conversely, rust preventatives INH3 and INH5 showed insufficient cleanability, which meant the cleaning process had to be repeated. Evaluation was conducted based on pass/fail criteria.
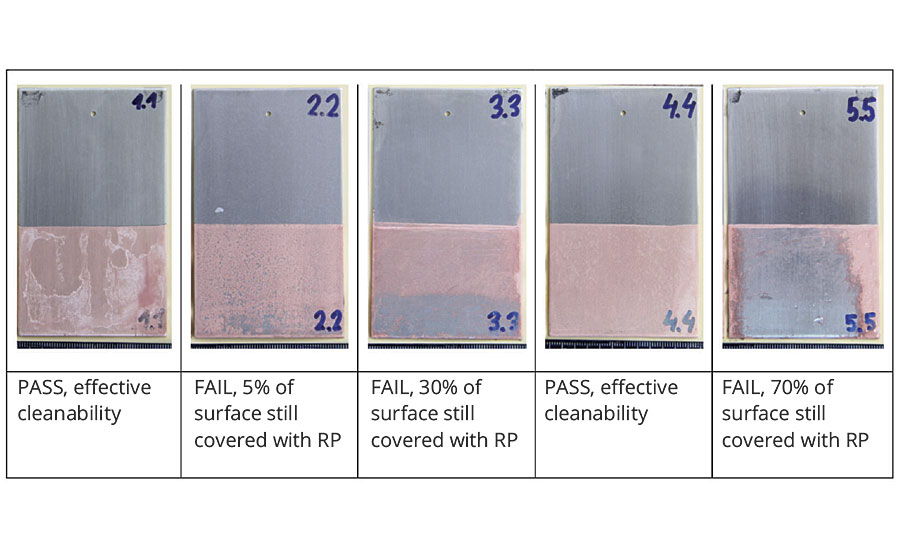
FIGURE 2 » Evaluation of the cleanability of rust preventatives.
Polarization Measurements
Figures 3 and 4 show the potentiodynamic polarization curves (Tafel diagrams) of unprotected carbon steel, alongside five rust preventatives, after 1 hr and after 120 hrs in fresh water. Polarization measurements provide important information about the kinetics of anodic and cathodic reactions.9 The corrosion parameters, namely corrosion potential (Ecorr), corrosion current density (jcorr), corrosion rate (vcorr), anodic and cathodic Tafel slopes (ba, bc) are listed in Table 4 and 5.
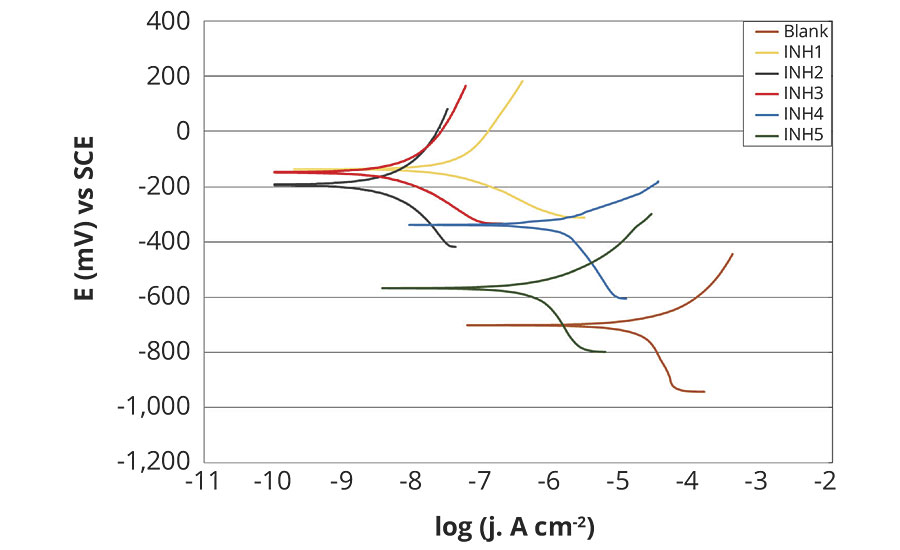
FIGURE 3 » Polarization curves of tested rust preventatives, compared to unprotected carbon steel after 1 hr testing in fresh water.
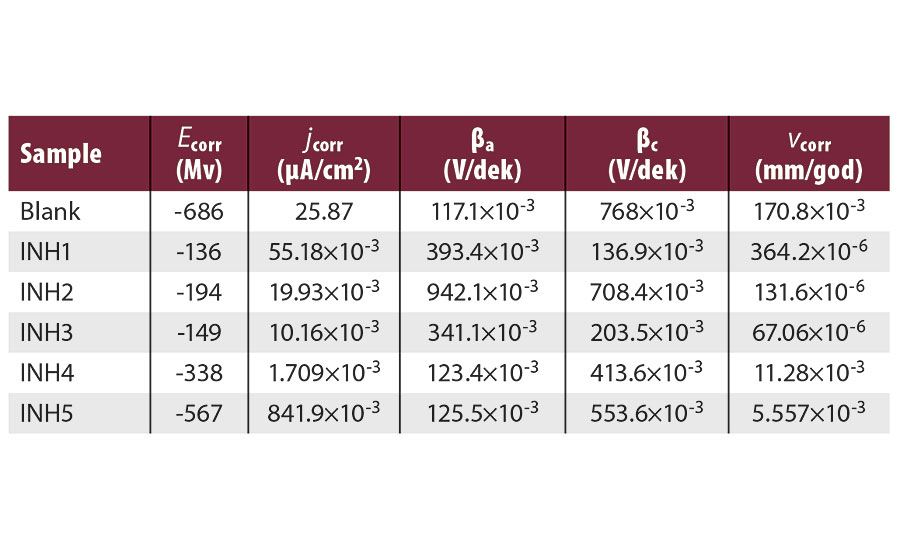
TABLE 4 » Polarization test results after 1 hr in fresh water, at a temperature (23±2) °C.

TABLE 5 » Polarization test results after 120 hrs in fresh water, at a temperature (23±2) °C.
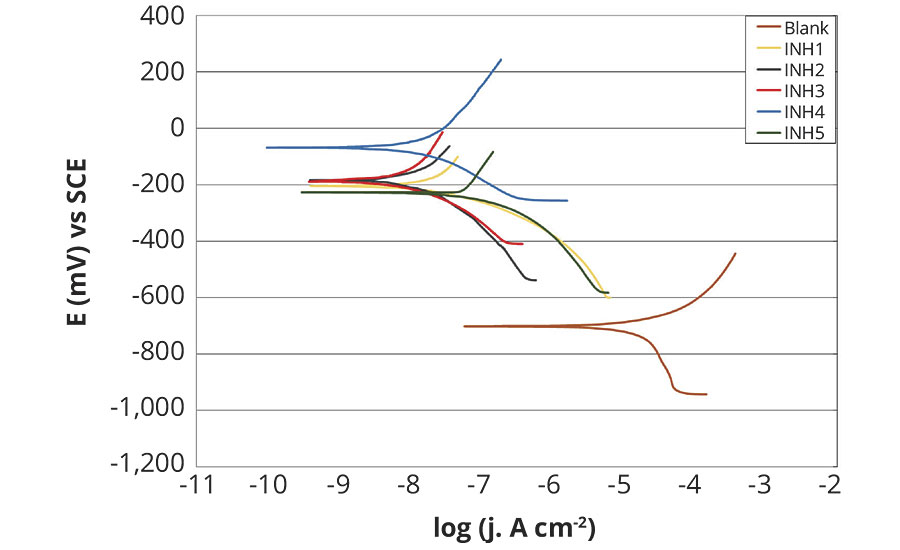
FIGURE 4 » Polarization curves of tested rust preventatives compared to unprotected carbon steel after 120 hrs testing in fresh water.
According to the data presented, corrosion current density decreased with the introduction of rust preventatives compared to unprotected carbon steel sample. The considerable corrosion potential shift to more noble values is observed with application of all rust preventatives, bio- and petroleum-based, indicating that tested rust preventatives greatly impacted the anodic reaction.10 However, addition of rust preventatives also modified the cathodic polarization curves, indicating that tested rust preventatives exhibited both cathodic and anodic inhibition effects. Therefore, the studied rust preventatives function as a mixed-type inhibitor, showing reduced anodic dissolution and retarded the hydrogen evolution.11,12 In order to evaluate inhibition behavior, an experiment without rust preventative addition was also performed. The blank curve exhibits more cathodic potential and higher current density.
After 120 hrs of exposure in fresh water, all tested rust preventatives showed similar corrosion protection taking equal potential-current position and shape in Tafel diagram, Figure 4. Only rust preventative INH4 showed a slightly higher potential shift. Compared to corrosion behavior at the beginning of exposure, after 120 hrs all tested rust preventatives showed improved inhibition efficiency, which can be attributed to a longer period for film forming on the metal surface.
The corrosion inhibition efficiency (h) after 1 and 120 hrs of testing was calculated using the relation (1):
hi = (Vcorr)ni – (Vcorr)i • 100%
(Vcorr)ni
(1) [3]
where (vcorr)ni and (vcorr)i are uninhibited and inhibited corrosion rates, respectively, obtained from potentiodynamic polarization curves. The increased h values show that the inhibition is more pronounced. Based on measured corrosion rate of unprotected compared to protected carbon steel, inhibition efficiency of tested rust preventatives was calculated and results are given in Figure 5. Maximum inhibition efficiency obtained from potentiodynamic polarization was with rust preventatives INH3, INH2 and INH1 respectively, whereas rust preventatives INH 5 and INH 4 showed something lower inhibition after 1 hr of exposure to fresh water. After 120 hrs, all tested rust preventatives showed over 99% inhibition efficiency. INH1, which is a water/biobased rust preventative, showed constant inhibition efficiency at the beginning and end of test, which demonstrates fast film adsorption properties. The solvent-based rust preventative INH5 showed the lowest improvement in corrosion resistance among all tested rust preventatives. However, corrosion resistance was improved by approximately 1,000 times better, compared to the unprotected sample.
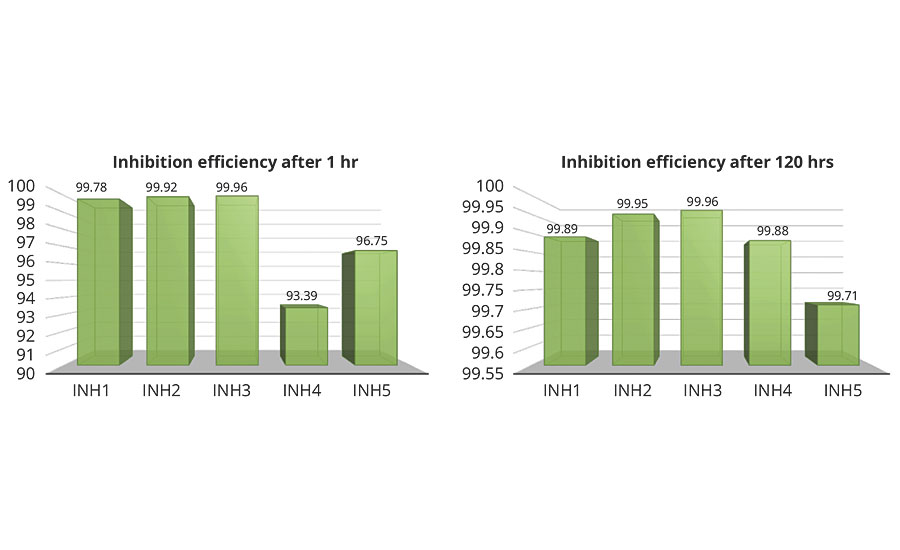
FIGURE 5 » Inhibition efficiency of rust preventatives after 1 hr (left) and 120 hrs (right) in testing solution.
Conclusions
Choosing the proper rust preventative is not only based on durability and effectiveness, but also removal and disposal concerns. A proper selection of rust preventative depends on storage and/or transport conditions, protection period, and also their economic and environmental impact.
In this article, the corrosion parameters as well as economic and environmental properties of five different rust preventatives used for temporary corrosion protection were compared. Specifically, water/biobased products were compared to petroleum-based products.
The results of this study are summarized as follows:
- Three of the five rust preventatives passed 600 hrs of high humidity testing. This included the biobased product, along with two of the solvent-based products. The remaining two solvent-based products failed during the test period.
- Higher thickness of rust preventative didn’t provide better corrosion protection. Further, this increased thickness had a negative influence on cleanability.
- In addition to being more environmentally friendly, biobased rust preventatives offer optimal corrosion protection, with no increase in protection cost, compared to petroleum-based and hazardous rust preventatives.
Following the results from this study, biobased preventative is an excellent and environmentally acceptable alternative to petroleum-based products in temporary corrosion protection.
References
1 Boris A. Mikši, FNACE. VpCI Technology Handbook, vol. 1, USA, 2014.
2 Kharshan, M.; Cracauer, C. The New Generation of Rust Preventative Products Based on Renewable Materials and Incorporating Vapor Corrosion Inhibitors, NACE Conference & Expo “Corrosion 2010”, Paper No. 10147.
3 Ivušic, F.; Lahodny-Šarc, O.; Otma i urkovi, H.; Alar, V. Corrosion Science, 98 (2015) 88-97.
4 de Wit, J.H.W.; van der Weijde, D.H.; G. Ferrari, G. Organic Coatings in Corrosion Mechanisms in Theory and Practice, Second Edition, Ed. P. Marcus, Marcel Dekker, Inc., USA (2002) p. 68 -729.
5 Becket, Giles J.P. Corrosion: Causes and Cures in Metalworking Fluids, Second Edition, Ed. J. P. Byers, Taylor & Francis Group, USA (2006) pp. 175-194.
6 Ghanbarzadeh, A.; Akbarinezhad, E. Progress in Organic Coatings, 56 (2006) 39-45.
7 Vitthal Khaire, M.; Nilavan, M.; Jain, A. IOSR Journal of Mechanical and Civil Engineering, 13 (2016) 82-90.
8 Moran, G.; Faber, B. Tribology & Lubrication Technology, 72 (2016) 28-34.
9 Ehsani, A.; Mohammad Shiri, H.; Mahjani, M.G.; Moshrefi, R.; Safari, R. Kovove Mater, 54 (2016) 233-239.
10 Dariva, C.G.; Galio, A.F. Corrosion Inhibitors – Principles, Mechanisms and Applications, in Developments in Corrosion Protection, Ed. M. Aliofkhazraei, InTech, (2014) pp. 365-379.
11 Olivares, O.; Likhanova, N.V.; Gomez, B.; Navarrete, J.; LlanosSerrano, M.E.; Arce, E.; Hallen, J.M. Appl. Surf. Sci., 252 (2006) 2894-2909.
12 `Karthikaiselvi, R.; Subhashini, S. Journal of the Association of Arab Universities for Basic and Applied Sciences, 16 (2014) 74-82.
Looking for a reprint of this article?
From high-res PDFs to custom plaques, order your copy today!