UMass Amherst Researchers Use Nano-Coatings to Create Electrically Heated Textiles
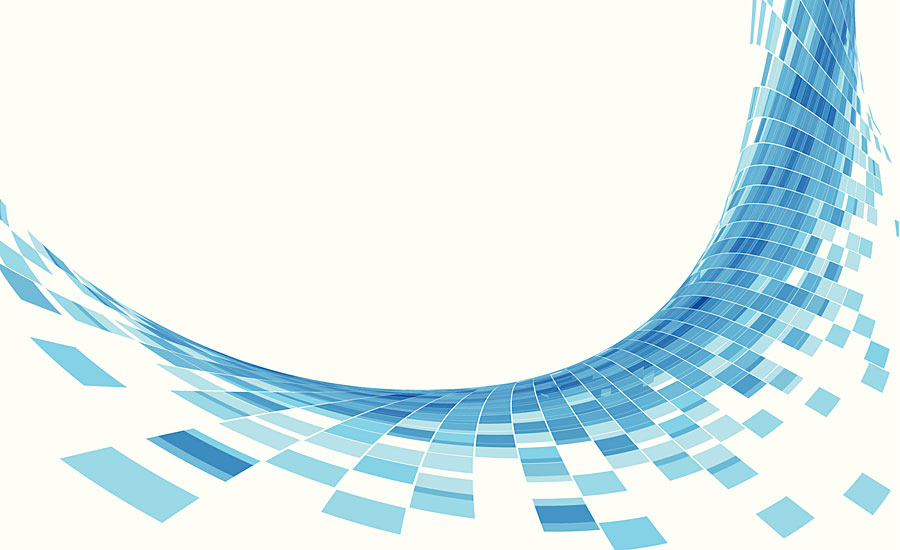
AMHERST, MA – Commuters, skiers, crossing guards and others who endure frozen fingers in cold weather may look forward to future relief as manufacturers are poised to take advantage of a new technique for creating electrically heated cloth developed by materials scientist Trisha Andrew and colleagues at the University of Massachusetts Amherst. They have made gloves that keep fingers as warm as the palm of the hand.
In a new paper in Applied Materials & Interfaces, the scientists describe how they use a vapor deposition method for nano-coating fabric to create sewable, weavable, electrically heated material. The demonstration glove they made can keep fingers toasty for up to eight hours. The three-layered glove, with one layer coated by the conducting polymer poly(3,4-ethylenedioxytiophene), also known as PEDOT, is powered by a button battery weighing 1.8 grams. A dime weighs just under 2.27 grams.
The authors point out, “Lightweight, breathable and body-conformable electrical heaters have the potential to change traditional approaches to personal thermal management, medical heat therapy, joint pain relief and athletic rehabilitation.”
Andrew says, “We took a pair of cotton gloves and coated the fingers to allow a small amount of current to pass through, so they heat up. It’s regular old-fashioned cotton cloth. We chose to make a pair of gloves because the fingers require a high curvature that allows us to show that our material is really flexible. The glove is powered by a small coin battery and they run on nano-amps of current, not enough to pass current through your skin or to hurt you. Our coating works even when it’s completely dunked in water, it will not shock you, and our layered construction means the conductive cloth does not come into contact with your skin.”
She adds, “We hope to have this reach consumers as a real product in the next few years. Maybe it will be two years to a prototype, and five years to the consumer. I think this is the most consumer-ready device we have. It’s ready to take to the next phase.”
Until recently, textile scientists have not used vapor deposition because of technical difficulties and high cost of scaling up from the laboratory. But recently, manufacturers are finding that the technology can be scaled up while remaining cost-effective, the researchers say. Using the vapor deposition method described in their paper, Andrew and colleagues also coated threads of a thick cotton yarn commonly used for sweaters. It performed well and offers another avenue for creating heated clothing, the authors state.
Experimenting with different variables in the vapor nano-coating process, they found that adjusting temperature and chamber pressure were important in achieving optimal surface coverage of the cloth. In a test of the fabric’s ability to resist cracking, creasing or other changes when heated, they generated a temperature of 28 degrees °C (82.4 °F) with connection to a 4.5-V battery and 45 degrees C° (113 °F) connected to a 6-V battery for an hour, and found “no dramatic morphology changes,” indicating that the PEDOT-coated cotton textile was rugged and stable enough to maintain its performance” when used as a heating element.
Funding for this work came from the U.S. Air Force Office of Scientific Research and partial support from the David and Lucille Packard Foundation. Andrew, who is director of wearable electronics at the Center for Personalized Health Monitoring in UMass Amherst’s Institute of Applied Life Sciences (IALS), says her lab is also developing a wearable heart rate monitor with electrodes embedded in a fitness bra. They plan to test that soon with volunteers on a treadmill at the IALS human movement facility.
Looking for a reprint of this article?
From high-res PDFs to custom plaques, order your copy today!