A Novel, Multipurpose Organic Coating System, Part 1






Editor’s note: This is Part 1 of a two-part paper. Part 2 will be published in the January, 2018 issue.
Abstract
The concept of an organic coating system consisting of a hot-melt coating (also known as thermoplastic coating), overcoated with a water-thinned coating while in the molten state, was explored by the development of solvent-free shop primers for forest product-based exterior architectural components. These shop primers with and without commercially available finishes were compared to selected commercial coating systems on various substrates by weather exposure in multiple locations. The concept is in its infancy, but coatings developed are commercially practical with performance equal or superior to conventional coating systems of recognized quality. Suggested applications of the concept include road marking and interior trim. The field is open for exploitation.
Introduction
This article reports on the development of an innovative class of pollution-free, rapid-dry organic coatings suitable for multiple purposes, but investigated here for architectural exteriors. Other applications of the concept may hold as much or more promise. Every effort has been made to provide a foundation for a variety of possible uses including road marking, which will be discussed. The concept has aroused interest as a candidate to replace protective laminates for some purposes, and it may be useful for other applications not yet conceived. Similar coatings were more recently developed by others1 for interior trim. Part 2 of this paper, to be published separately, will report performance in the weather on challenging surfaces.
The first step toward the desired two-coat system is to apply a hot-melt coating on an industrial finishing line. It is a solid under ambient conditions, liquefied by heat for application and essentially free of volatiles. It is overcoated within seconds with a solvent-free, water-thinned coating that must adhere to the hot-melt surface, which it must not damage, and must quickly cure at a temperature that will not liquefy the solidified hot-melt. The close timing in application of the two coats is economically advantageous, but beyond that it utilizes the higher surface energy of the molten hot-melt to optimize wetting and adhesion by the water-thinned coat. This second coat is cured by heat absorbed from the hot-melt coating and by high-volume air and/or external heat. If the substrate is hot, as from a fabricating process, cooling will be assisted by the evaporative cooling effect of the water from the water-thinned coat. This second coat may be opaque, tough and tack free. The coated product, such as exterior trim or siding, may be stacked or packaged. The water-thinned coat may serve as the finish, or one or more additional water-thinned or solvent-thinned finishes may be applied, on the same finishing line or at a later time.
The contributions of the hot-melt coating include adhesion to the substrate, almost instant hardening, barrier properties and functional properties such as elasticity, for specific uses. It may be designed for subsequent polymerization to harden the film and prevent its softening in summer sun. Or it may penetrate a porous substrate and then polymerize to enhance adhesion and surface stability.
The water-thinned coating protects the hot-melt coating against damage in handling and prevents coated surfaces from sticking together when stacked (block resistance). It also protects the hot-melt coating against attack by solvents in finish coats that may be applied later, and separates anti-oxidant in the hot-melt from subsequently applied finish coats that cure by oxidation. Opacity in an exterior water-thinned coating can protect the hot-melt and the substrate from photochemical damage by sunlight. Accidental damage to the primed surface is readily repairable in the field.
This composite coating, formed by near-simultaneous application of two coats of very different composition, offers several advantages. It is well suited to forest product surfaces because on an industrial coating line it does not require high substrate temperatures. Its relative impermeability is enhanced because film formation by solidification through cooling forms no channels through the film as are formed when volatiles evaporate. Yet it has been shown to be sufficiently permeable to cause no condensation in exterior walls (see Part 2 of this paper, to be published in PCI's January 2018 issue). As a shop primer, it protects building components from weather from the time of manufacture so that photochemical surface damage does not degrade the performance of subsequently applied coatings. Additionally, the durability of the latex coat permits its alternative use as a finish when formulated and applied for the purpose. As a general rule, solvents - sources of pollution, flammability and toxicity - may be omitted from the coating system, with latex coalescence provided by the heated cure.
The coating system proposed here is believed to be economically competitive on an equal thickness basis, but more importantly, this coating concept is largely unexplored and open to innovation. No limits can yet be placed on it in terms of either cost or performance. Substitution for protective laminates for some purposes, if found feasible, would offer considerable economic latitude. Proposed ingredients are readily available, manufacturing and packaging are by standard methods, and stability meets customary requirements.
History
A digression to the history of this investigation is necessary to disclose work otherwise unreported but forming the basis of the present undertaking. The initial investigation of the concept was in the 1960s and included weathering tests, but written records had been lost before ownership of the intellectual property devolved to me, as inventor. The present account is from my memory. The original impetus was the search then being undertaken by the wood siding industry, for an industrial shop primer to improve the paintability of siding cut from some species of wood.
The latex coating in the hot-melt/latex system tested in the 1960s was a white acrylic house paint typical of the day. The hot-melt coating employed a then-newly-available ethylene-vinyl acetate copolymer (EVA). This particular EVA contained 28% vinyl acetate, with a melt index of 43. It was chosen for toughness, adhesion and extensibility; for compatibility with drying oil, and to increase surface energy for better intercoat adhesion of the latex overcoat. Polychlorinated triphenyl was a major binder ingredient included to reduce melt viscosity for application. This material has since been withdrawn from the market as a pollutant akin to polychlorinated biphenyl. The balance of the binder was tung oil, with cobalt drier present, providing potential for limited crosslinking to prevent softening in summer sun. The hot-melt coating was pigmented to an opaque off-white with no filler.
Test application was to about 20 pieces each of redwood and southern yellow pine siding about 1.2 m by 15 cm (4 ft. by 6 in.). A double-headed pressure-type curtain coater was used, with the first coater head equipped to apply hot-melt and a conventional head for the latex paint positioned downstream over the same conveyor to apply the second coat within about one second. Appearance and uniformity of the coating system were excellent, except that the unsanded siding raised a few small splinters so that the high conveyor speed caused a small “shadow”, or bare spot, upstream of each splinter. This was fortuitous, as described below. The application temperature of 120 °C (250 °F) was low for a hot-melt coating but suitable for the composition used. No record of film thickness survives.
Weathering tests, south vertical, were continued for five years at a suburban location in central Alabama. Some panels were exposed without an additional coat. Others were brushed with a single finish coat of a white alkyd house paint, and the balance received a single brushed coat of white latex house paint. Backs and edges were coated, with no panel backing.
Five years of exposure produced no failure of any kind on any of the 40-odd wood panels. Southern yellow pine is considered a poor surface to paint, but even on pine panels coated only with the two-coat primer, there was no failure, even at the edges of the small “shadow” areas that remained uncoated.
Although results were favorable, the lumber industry lost its siding market during the time required for testing, so the perceived opportunity was gone. My then-employer was averse to the risk of attempting to open other markets. Testing was concluded until 30 years later when I undertook a more extensive investigation of the potential value of the invention. In that effort I worked alone, so personal considerations including advancing age sometimes influenced decisions in planning and execution. Thus the decision to use an “unpaintable” grade of plywood to accelerate test results in weathering.
Experimental
For brevity, coating systems consisting of a hot-melt coating overcoated while in the molten state with a latex coating will hereafter be referred to as “hybrid” systems.
Formulation and Preliminary Testing of Hot-Melt Coatings Intended for Weathering Tests
Several features of the hot-melt coatings were determined before beginning experimental work. I could not re-test a formula like that tested in the 1960s, having no detailed record of its composition and no source of polychlorinated triphenyl. However, the use of drying oil was still an attractive idea to increase hardness by providing crosslinking. An oil-free hot-melt coating was also to be prepared for comparison. Both were to employ an EVA with high vinyl acetate content, as successfully used in the 1960s for compatibility with drying oil and to maximize surface energy and thus enhance intercoat adhesion. Ultimately, EVA with very high (40%) vinyl acetate was needed because intercoat adhesion suffered when overall EVA molecular weight was reduced to meet a viscosity requirement. A departure from the 1960s composition was omission of opaque pigmentation in the hot-melt coating, in confidence that the opacity of the latex coating would suffice.
Compatibility of all components would be imperative since multiple phases could separate, form a weak layer and destroy intercoat adhesion. This was likely to require the exclusion of the waxes commonly used to reduce the viscosity of hot-melt compounds but often incompatible. Hydrocarbon resins, another group of common hot-melt ingredients, were also excluded. They were compatible but detracted seriously from reverse impact performance (method in Appendix 1), seen as a proxy for grain crack resistance and tested before and after exposure in a QUV cabinet.
Need for anti-oxidant was anticipated for stability, but in a coating system intended as a primer this additive must be minimized lest it migrate and interfere with drying of oxidizing-type finish coats. Another necessary additive would be calcium carbonate as an acid acceptor to remove destructive products of decomposition of vinyl acetate. Discretion was again required because it could leave white deposits, or “frosting”, on an exterior coating after evaporation of acid rain.
An essential requirement was to formulate hot-melt coatings suitable for application by direct roll coater, which was the equipment available. Maximum hot-melt viscosity acceptable for roll coating is about 25,000 mPa.s at application temperature. To meet this limit, a compromise with film strength and extensibility was necessary, replacing some of the higher-molecular-weight EVA with EVA of lower molecular weight, and with oxidized polyethylene. The latter was fully compatible but was less efficient for viscosity reduction than incompatible waxes and polyethylenes.
A major concern was potential failure of other coatings applied over hot-melt coatings or over hybrid systems, due to softness of the underlying hot-melt. This can occur in exposure of dark colors to summer sun, which can generate temperatures estimated from published data2,3 to be as high as 121 °C (250 °F). Hardness at high temperatures was best maintained by crosslinking with drying oil. Molten stability could be maintained by care in the addition of drier. The required crosslinking time of several days was acceptable because it was less than the inevitable delay between commercial coating and exposure to the weather. Success with tung oil in earlier work and its shorter time to cure recommended it as the choice over other oils tested. Polymers such as alkyd resins contributed too much viscosity.
Drying oil in a hot-melt coating contributed to intercoat adhesion and reduced viscosity. Consequently, the drying-oil-free hot-melt coating required additional oxidized polyethylene to reduce viscosity, which diminished intercoat adhesion. This created a need for a compatible low-viscosity binder ingredient that could contribute to higher surface energy and thus to intercoat adhesion. Hence the inclusion of an EVA terpolymer further described in Table 1. Properties of oil-modified and oil-free hot-melts were not distinguishable by touch or appearance.

TABLE 1
The most critical aspect of hot-melt coating application is control of application temperature. It must be high enough for satisfactory adhesion but low enough for the necessary stability of the molten coating. Attention to well-chosen temperature limits, in applying the coating, assures adhesion and thus prevents failure that could be catastrophic. The application temperature of the oil-free hot-melt coating provided a comfortable margin of error; however, the drying-oil-modified hot-melt coating required an application temperature close to its lower limit, lest it skin on the coater. This called for considerable caution in coating board for test panels, but in commercial practice an inert gas blanket is often used to permit increased temperature and a higher factor of safety.
During storage, drying-oil-modified hot-melt coatings increased in molten viscosity to an unacceptable degree. Stability was achieved by a two-component approach, with drying oil in one component and cobalt drier in the other, each formulated to remain solid in storage. Granules of the two components were blended to provide the desired molten composition.
Tendency to penetrate wood was estimated by testing on filter paper (see Appendix 1). Penetration of drying oil was of interest because it has been reported that “improved penetration - [would result in] better surface stabilization, which [might] be a key to extended performance of exterior painted wood.”4 However, penetration has been reported to damage adhesion if the penetrant acts as thinner for polymers in the coating and does not subsequently polymerize.5 I was uncertain whether a hot-melt coating would remain hot enough, long enough for penetration. In fact, hot-melt coatings were found to penetrate almost instantaneously at hot-melt application temperatures, provided the coating contained a very low-molecular-weight polymer or a drying oil. In the absence of such ingredients there was no penetration.
Greater hardness could be achieved, as would be expected, by using binder ingredients with high softening points and by the inclusion of inorganic filler. The filler was a fly ash product with mostly spherical particles, and diameter in the higher acceptable range, achieving low binder demand through minimum surface area. For uniform composition in thin films, I used a high-speed disperser to incorporate filler into molten polymer, although for other applications particulates are often mixed into hot-melts using considerably less energy.
The composition of the drying-oil-free hot-melt coating selected for weather testing is provided in Table 1 and of the drying-oil-modified hot-melt in Table 2. For compositions of each of the two components of the drying-oil-modified coating, see Tables 3 and 4.

TABLE 2

TABLE 3
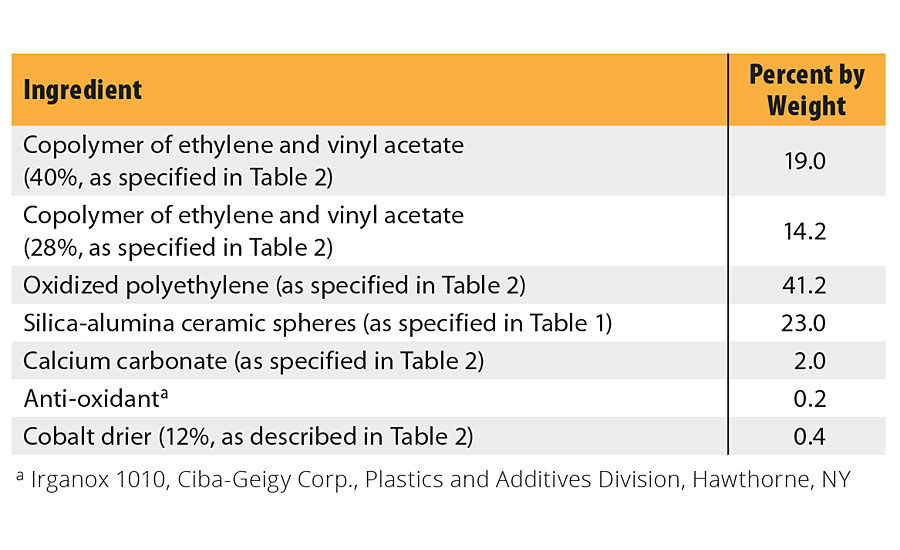
TABLE 4
Formulation and Preliminary Testing of Latex Coatings Intended for Weathering Tests
A critical property of the latex primer was block resistance to permit prompt stacking and/or packaging of the coated product. The hardboard industry, still enjoying a sizable siding market at that time, was a source for blocking tests developed for a purpose similar to mine, but there was no standard test. After a study of tests used in that industry, I decided to test under a pressure of 14 kg/cm2 (200 lb/in2) for 16 hrs. For details see Appendix 1.
When several otherwise satisfactory latex emulsions were tested, the best performer was marginal for block resistance, even when near its critical pigment volume concentration (CPVC). Using this latex, I formulated above CPVC, expecting that when the latex primer was adhered to a coating having the high film integrity of the hot-melt, porosity would not seriously detract from the weather resistance of the two-coat system. This did improve block resistance, with further improvement achieved by addition of an aziridine crosslinking agent. This highly pigmented coating is easily recoated when applied at 25 µm thickness or less over a hot-melt coating, but in thicker films or over other surfaces its porosity makes it difficult to recoat by brush. It was selected as the principal latex primer for weathering tests. Its composition is provided in Table 5.

TABLE 5
Preliminary Testing of Hybrid Primer Systems
A performance requirement influencing formulation of hot-melt coatings and latex primers was that the hybrid film be recoatable with a solvent-thinned paint that required oxidation to cure. The solvent in the coating must not attack the hot-melt, and anti-oxidant from the hot-melt must not retard drying of the finish coat. These requirements were met by addition of a selected anti-oxidant in a critical concentration, and by a latex primer film 12 to 25 µm thick separating the hot-melt film from the finish coat. When oxidizing finishes were applied directly to the hot-melt surface, drying was seriously retarded, thus demonstrating the protective function of the latex primer. Prevention of anti-oxidant migration depended more on spacial separation of the hot-melt and the oxidizing paint than on any barrier effect, since porous and nonporous latex films had similar effect. The latex coat also successfully protected the hot-melt film from defects in appearance and adhesion, potentially caused by the solvent contained in the oxidizing finish.
Proposals not Extensively Investigated for Employing Hybrid Coating Systems
Alternative Method of Application
A compromise in hot-melt coating composition was necessitated by the viscosity limit imposed by roll coater application and may have led to performance inferior to what otherwise might have been attained. Increased content of higher-molecular-weight EVA would have been preferred but could not be accommodated. It is recommended that in any further investigation of the proposed concept, hot-melt application by extruder6,7 be considered for a less-restricted range of composition.
Pavement Marking Systems
In deference to terminology used in the road marking industry, coatings described as “hot-melt” up to this point will now be termed “thermoplastic”.
There are considerations that recommend the hybrid coating system for investigation for road marking purposes. First, consider the limitations of the types of coatings that make up a hybrid system - latex marking paints and thermoplastic markings - when they are used separately. Jiang8 reports that latex marking paints are widely used because of their low cost, but tend to flake from asphalt surfaces with a service life of one year or less, and are not satisfactory on heavily traveled roads. Thermoplastic markings, also widely used, are more durable but tend to erode, and hence do not provide long-term retention of drop-on reflective beads. In anticipation of erosion, they are commonly applied at thicknesses of 1.5 to 3 mm (about 60 to 120 mils) and often contain matrix beads in addition to drop-on beads, so that beads are exposed as the stripe erodes. This high thickness is costly, as is frequent replacement of latex striping. Effective control of erosion in thermoplastic striping would have significant commercial value, as would extension of latex striping life. A hybrid road striping system may offer both.
Analysis of data comparing the durability of road marking in lane lines versus edge lines applied at the same time9 has established that weather, and not road wear, is primarily responsible for erosion. Suggestions offered here for further investigation into the use of a thermoplastic/latex two-coat striping system will assume the predominance of weather erosion.
Extensive weather testing of hybrid coatings on wood, to be reported in Part 2 of this paper, shows opaque pigment to be unnecessary in the thermoplastic coat of a hybrid system. Indications are that a properly pigmented and reflectorized latex stripe could provide the desired visibility and retro-reflection, while protecting the underlying thermoplastic stripe from damage by UV radiation. Consequently, the thermoplastic layer need not be colored or opacified, nor contain glass beads.
Trials seem warranted to confirm whether an opaque latex stripe of the desired color, applied over and protecting an adherent thermoplastic stripe, will enhance bead retention and extend pavement marking life. Many latex films do have exceptional resistance to erosion, as illustrated by an exterior exposure test that I once examined. Assorted kinds of exterior house paint had been applied in a checkerboard pattern to a large square panel so that every possible sequence of application of the several paints was represented by a square on the checkerboard, with several coats on each square. After nine years of exposure, every square had eroded down to the top layer of latex paint on that particular square, and there the erosion had stopped. All of the latex paints tested were far more erosion resistant than any of the oil or alkyd paints applied along with them. A highly erosion-resistant opaque latex striping paint, applied over nonopaque thermoplastic striping chosen for its adhesion, may provide this same advantage in road marking, hopefully translating into bead retention.
The weathering tests to be reported in Part 2 of this paper have established that adhesion of latex paints to hot-melt coatings can be excellent and long lasting if both coatings are properly designed and applied. Thus the application of a latex striping paint to molten thermoplastic striping will create a very different situation from that which causes latex striping paint to flake from a road surface. The latex need only adhere to the thermoplastic marking, which is far superior in its adhesion to asphalt pavement. Investigation seems worthwhile.
Application of the latex stripe while the thermoplastic stripe is in the molten state will require a single truck to apply thermoplastic marking, latex marking and beads. It appears that the thickness of the thermoplastic stripe need only be sufficient for good adhesion to the road surface at the prevailing surface and air temperatures. A thin stripe would be more economical and could be helpful in minimizing stripe removal by snow plows. Alternatively, if greater thickness were applied to elevate the beads and thus enhance wet night retro-reflectivity, the omission of pigment from the thermoplastic stripe would make an even greater contribution to economy.
A hybrid stripe could also simplify quality control in the marking process, a major problem for many organizations that mark roads. The depth of immersion of a glass bead in a coating matrix determines its retro-reflective efficiency, and rheology is an important factor that governs depth of immersion. The control of bead immersion must contend in a thermoplastic stripe with rapidly changing viscosity, presenting a challenge to the marking crew. A latex film is relatively stable in viscosity, and so less challenging, and a latex-over-thermoplastic stripe would put all beads into the latex layer. If a higher proportion of the beads were efficiently retro-reflective, both driver safety and road marking economy would be enhanced.
Whether a hybrid striping system for evaluation is chosen from existing thermoplastic and latex marking materials, or is formulated for the purpose, attention must be paid to complete compatibility of the ingredients in the thermoplastic marking, lest an incompatible phase should separate, form a weak layer on the surface and interfere with intercoat adhesion. Furthermore, surface energy of the thermoplastic layer must be sufficient to permit wetting and adhesion by the water-thinned layer. Latex striping paints used for this purpose may require coalescing solvents and consequently not be entirely solvent free as has been suggested for other applications.
Very limited experimental work has confirmed that at least some existing latex marking paints and some existing thermoplastic markings are suitable for durability testing as a two-coat striping system. It has further confirmed that the commonly employed high temperatures and high thicknesses of thermoplastic stripes will not cause the latex stripe to boil or otherwise interfere with formation of the striping system. Heat from the thermoplastic layer does significantly accelerate latex film formation.
Summary
In the 1960s a coating system formed by overcoating a molten hot-melt coating with a latex paint was conceived as an answer to a search by the wood siding industry for a primer to improve paint performance on its product. Performance testing including weather exposure had a positive outcome, but circumstances prevented commercialization. Thirty years later, as the originator of the concept, I undertook upon retirement a more thorough investigation. I now make public a report on coating system composition and performance. It describes extensive testing including weathering and suggests the use of this coating system for road striping and other applications far afield from the original purpose. Solutions are described for several problems that a coatings system of this kind may bring to mind.
Acknowledgment
I thank Dennis Nie for many hours devoted to a generous assist in recording this work. I thank Thad Broome and Ed Lowrey for critique and editing.
References
1 Lizotte, J.R., et al, (to Eastman Chemical Co.), U.S. Patent Application 20100015456 (Jan 21. 2010).
2 Stoloff, A. Weathering of Vinyl Siding, J. Vinyl Technology, Vol. 15, No. 4 (1993).
3 www.ncdc.nooa.gov and telephone 828-271-4800.
4 Nussbaum, R.M.; Sutcliffe, E.J.; Hellgren, A.C. Microautoradiographic Studies of the Penetration of Alkyd, Alkyd Emulsion and Linseed Oil Coatings into Wood, J. of Coatings Technology, Vol. 70, No. 878, 49 (1998).
5 Meijer, van de Velde and Mility. Rheological Approach to the Capillary Penetration of Coating into Wood, J. of Coatings Technology, Vol 73, No. 914, 39 (2001).
6 Greenlee, W.S., et al, (to BF Goodrich Co.), U.S. Patent 5,198,303 (Mar. 30, 1993).
7 Curtiss, B.J., et al, U.S. Patent Application 20050106406 (May 19, 2005).
8 Jiang, L. Durability and Retro-reflectivity of Pavement Markings, Joint Transportation Research Project, Indiana Department of Transportation (2008).
9 Agent, K.R., et al, “Evaluation of Durable Lane Delineation Materials”, Kentucky Transportation Center (1989).
APPENDIX 1
Test methods – laboratory methods of coating application.
Methods for Hot-Melt Coatings as Components of Hybrid Coating Systems
Preparation of a smooth, plane surface suitable for use of a Bird-type applicator on wood
Use planed wood or AC-grade plywood panels free of “fuzz”. Using a frame constructed for the purpose, tightly stretch a #150 grit abrasive cloth over plate glass and perform 200 firm back and forth strokes of the plywood panel surface against the abrasive. Planarity is evaluated by applying a white latex paint to an abraded panel, using a Bird-type applicator with 25 µm (1 mil) gap, and examining the partially opaque film for uniformity.
Laboratory application
Using a Bird-type applicator, closely control the temperature of every material, tool and surface. To briefly maintain the temperature of metal objects, set them on steel block heat sinks, preheated to the desired temperature. Handle hot objects with insulated gloves. High viscosity of many hot-melt coatings pushes material under the feet of the applicator, causing uncontrolled increase in film thickness. To avoid this, use an applicator with a gap considerably wider than the film to be deposited.
Film thickness measurement
For smooth films on thin wood panels or on paper, follow ASTM D1005, Standard Test Method for Measurement of Dry-Film Thickness of Organic Coatings Using Micrometers. Reproducibility is enhanced by cooling the coated material to -18 ºC (0 ºF). Where a micrometer is impractical or the film is textured, use gravimetric measurement with thickness estimated from calculated film density. For steel surfaces, follow ASTM D7091, Standard Practice for Nondestructive Measurement of Dry Film Thickness of Nonmagnetic Coatings Applied to Ferrous Metals and Nonmagnetic, Nonconductive Coatings Applied to Ferrous Metals.
Viscosity
Follow ASTM D3236 Standard Test Method for Apparent Viscosity of Hot-Melt Adhesives and Coating Materials.
Compatibility
Hold a homogenous, particulate-free sample of a mixture of coating ingredients at application temperature in a transparent container for three hours and inspect it for evidence of separation. This is a generally satisfactory test, in the absence of equipment for determination of glass transition temperature.
Penetration
Use Method 4421, Federal Test Method Standard 141C, modified for use with hot-melt coatings. This obsolete test was developed to estimate penetration of paint vehicles into plaster or drywall. The spread of components of a coating film, by absorption into filter paper, is visually measurable in millimeters.
Stability in the molten state
Follow ASTM D4499 Standard Test Method for Heat Stability of Hot-Melt Adhesives.
Method for Latex Coating Components of Hybrid Coating Systems
Film thickness
Follow ASTM D4138 Standard Practices for Measurement of Dry Film Thickness of Protective Coating Systems by Destructive Cross-Sectioning Means.
Methods for Hybrid Coating Systems
Adhesion to substrate, also used for intercoat adhesion
Follow ASTM D3359-92a method B. The method provides for a scale on which 5 denotes maximum adhesion, but on plywood panels it was not possible to distinguish a rating of 5 from one of 4.
Hardness at elevated temperature
Expose a hybrid coating, on plywood, to heat from an infrared device, at a measured distance. Decrease the distance between panel and heat source stepwise, at predetermined intervals of two or more hours each. Using a surface pyrometer, measure the panel surface temperature after equilibration at each step until it reaches 121 ºC (250 ºF), and observe the panel for blistering of the latex coating. If blistering occurs, record the temperature.
Blocking
Place pairs of 5.1x5.1 cm (2x2 in) square plywood panels under a pressure of 14 kg/cm2 (200 lb/in2), with identically coated sides facing, and maintain the pressure for 16 hrs at 54 ºC (130 ºF) and 90% relative humidity. The pass/fail criteria require that pairs of panels separate without damage to the coatings and without noticeably sticking together. Panels coated with hybrid systems tend to adhere to each other at the extreme edges, but only at the edges. This was not judged to constitute failure, because the pressure caused the hot-melt coating to exude slightly at the panel edges, and exuded coating from one panel adhered to that from the other. If the panels separated freely after the exuded coating was cut away without disturbing the contact between them, the pair was considered to pass. The logic was that face-to-coated-face positioning of the panels, and the small panel size in this test, caused the problem, whereas commercial practice is to stack much larger board face-to-back.
To apply the desired pressure, drill a hole in the center of each of four pairs of panels and assemble them in a stack, paired as above. Insert a threaded stainless steel rod though the stack and through a spring of known spring constant, the rod fitted at each end with a nut and washer, and with a stainless steel plate of the same dimensions as the panels. Tighten the nuts, measuring spring travel, until the calculated force produces the desired pressure on the panels. If the plywood is partially crushed during early hours of the test, re-tighten the nuts to maintain constant pressure.
Reverse impact
Use a test device of the type in which the hemispherical impact tool is part of the dropped weight. Test on steel Q panels, with hot-melt film thickness of either 50 or 75 µm (2 or 3 mils) and latex primer dry film thickness of 12 -25 µm (1/2 to 1 mil), at a panel temperature of -18 ºC (0 ºF), and at an impact of 162 cm-kg, (115 in-lb.). Examine the impacted area for cracks in the coating, using 7x magnification. Evaluate intercoat adhesion by scraping with a pen knife.
Looking for a reprint of this article?
From high-res PDFs to custom plaques, order your copy today!