Researchers To Develop Coatings For Nuclear Fuel Cladding
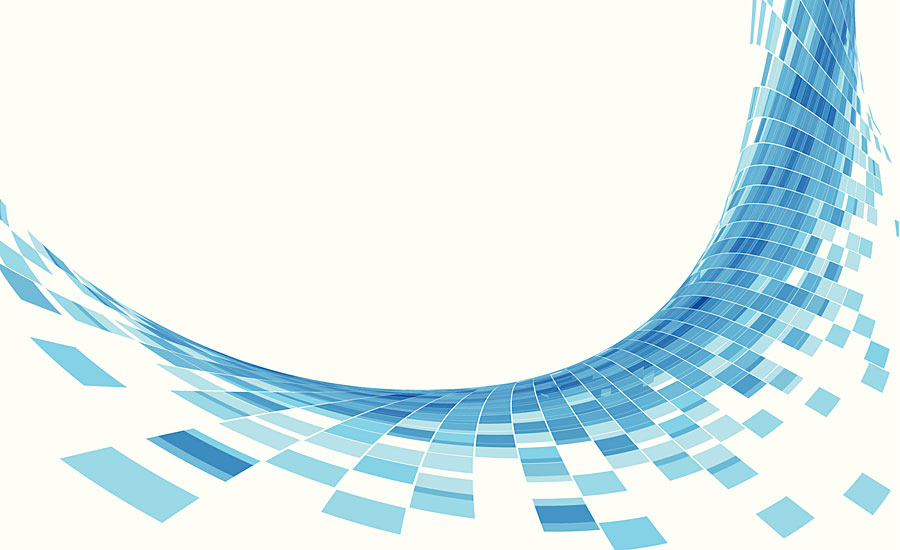
CAMBRIDGE, MA - Assistant Professor of Nuclear Science and Engineering Michael Short and collaborators — Professors Bilge Yildiz, Matteo Bucci, and Evelyn Wang, as well as the MIT Nuclear Reactor Laboratory and the Westinghouse Electric Co. — have received funding from Exelon Generation to support research to develop coatings technology that could transform the performance of the fuel cladding in light water reactors (LWRs).
Four known issues can impact the safe and reliable operation of LWR fuel cladding. They include fretting and wear from grid-to-rod-fretting and foreign material; the buildup of porous corrosion deposits; hydrogen absorption; and boiling crisis. Fretting can wear through the fuel cladding, while deposits and hydrogen absorption can lead to corrosion-based fuel failure, respectively. Finally, a “boiling crisis” is when the normally bubbly mode of coolant boiling, called sub-cooled nucleate boiling, transitions to film boiling, insulating the fuel with a layer of steam and worsening heat transfer.
All four issues can and have caused failure of fuel cladding, leading to radioactive releases into the coolant and costing reactor operators over $1 million per day of downtime to fix the problem. The goal of the MIT project is to address all four issues at once by developing a viable solution, consisting of engineered cladding surface coatings and micro/nano geometric modifications to reduce or eliminate all four problems, within three years. The team will design a set of coatings and surface modifications for Zircaloy-based fuel cladding currently in use. The combination will simultaneously:
- Minimize or prevent buildup of unidentified deposits and hydrogen pickup, which in turn will increase the lifetime, stability, and power density of the fuel;
- Improve hardness to prevent grid-to-rod fretting, which occurs when the spacer grid (a metal piece which separates the fuel rods) and the rods themselves vibrate and wear holes into the metal; and
- Maximize critical heat flux (critical heat flux describes the thermal limit of a phenomenon where a phase change occurs during heating) to improve heat transfer.
This targeted three-year development time from lab-scale tests to commercial reactor implementation is unprecedented. The normal process for most new reactor components is between 10 and 15 years.
The MIT team will work with fuel vendor Westinghouse Electric Co. and the nation’s largest nuclear operator Exelon Generation to test and identify the best coating for commercialization and use in a commercial U.S. reactor by 2019. The project brings together MIT researchers from the departments of Nuclear Science and Engineering, Materials Science and Engineering, Mechanical Engineering, and the MIT Nuclear Reactor Lab.
The funding will support research in the Center for Advanced Nuclear Energy Systems, one of the MIT Energy Initiative’s eight Low-Carbon Energy Centers, which Exelon joined as a member in 2016 to advance key enabling technologies for addressing climate change.
Looking for a reprint of this article?
From high-res PDFs to custom plaques, order your copy today!