Copper in Antifoulings: Going from Strength to Strength
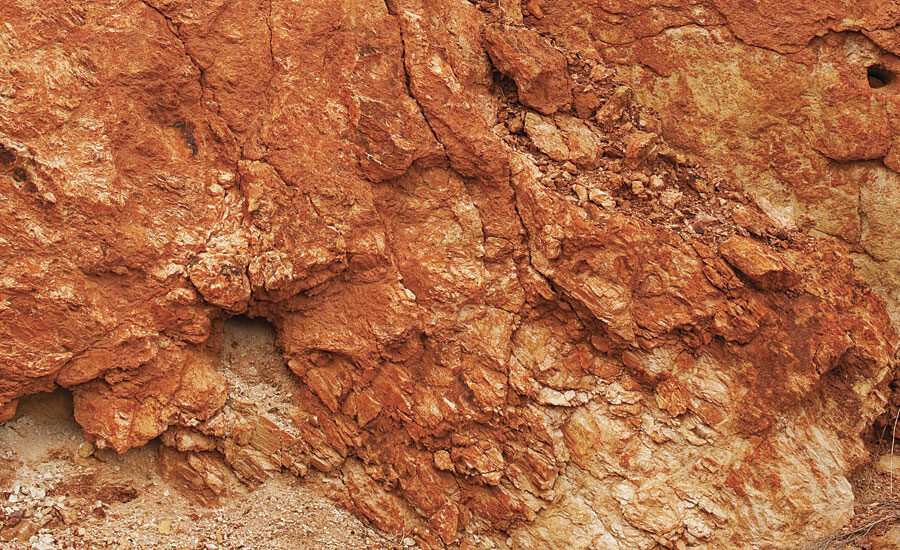
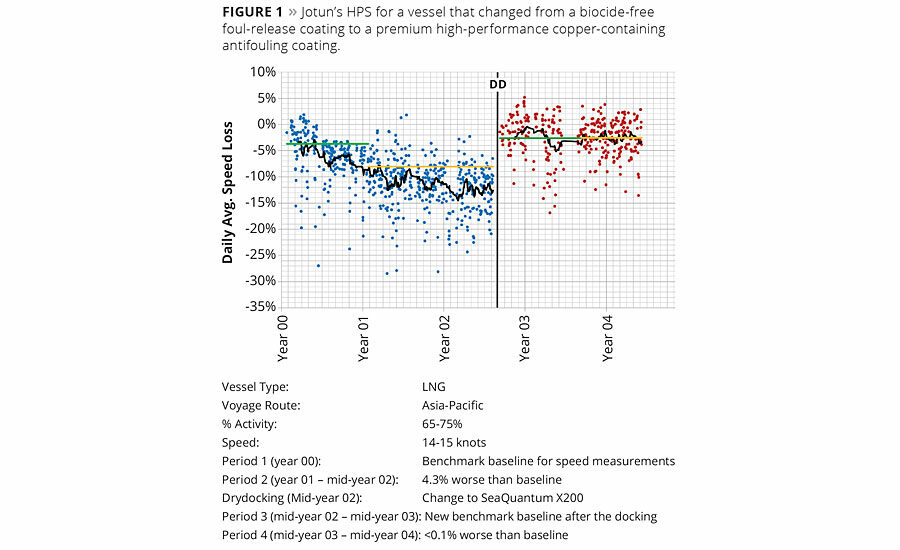
Figure 1
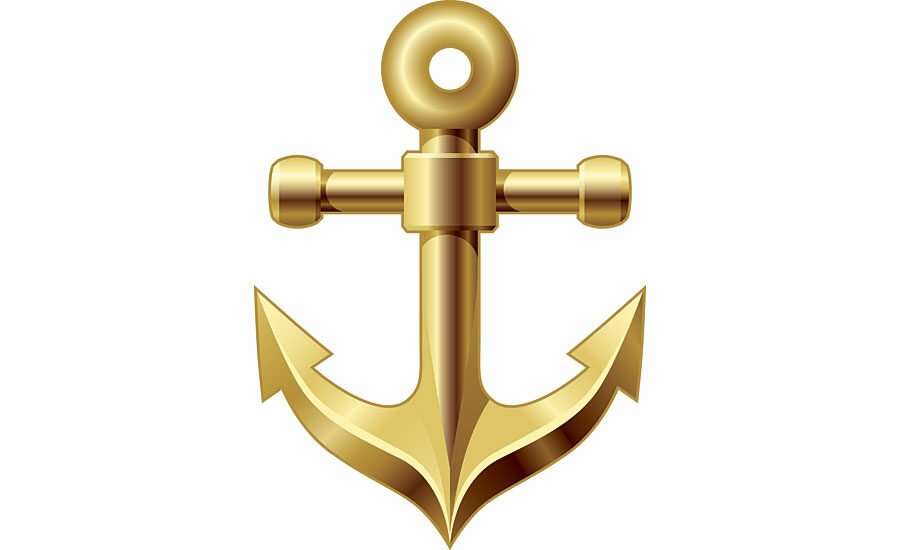
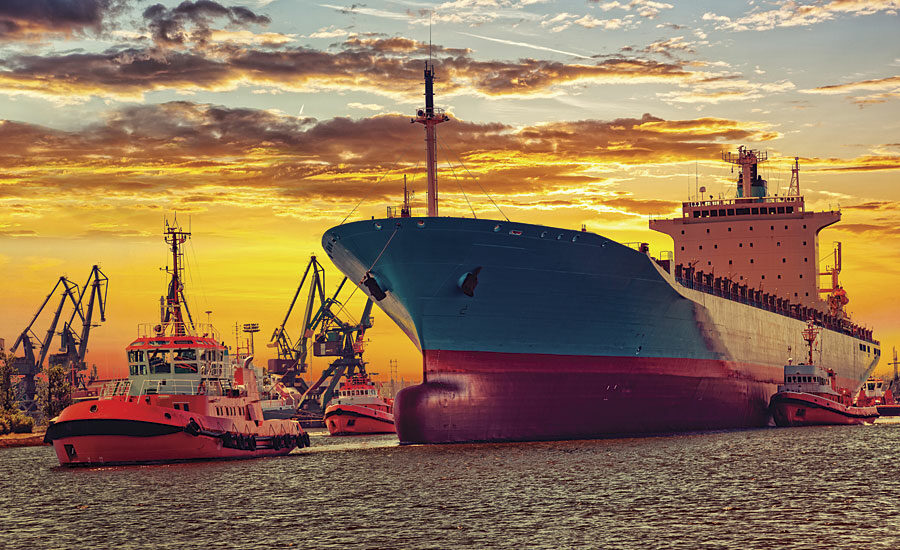




This article gives an updated overview of the use of copper in antifouling paints. In the first part, the worldwide regulatory status is summarized, for both commercial vessels and pleasure craft, based on the results from the detailed scrutiny of copper that has been undertaken by regulators in recent years in countries such as the United States, Australia, New Zealand and the EU. Ship performance data is then presented that shows the economic and environmental benefits that use of a premium copper-based antifouling can deliver. The increasingly sophisticated monitoring systems that are now being deployed on ships for measuring energy efficiency are able to isolate hull and propeller effects, and thus show the benefits of having a hull fully protected from fouling.
Regulatory Status of Copper in Antifouling Coatings
Every country in the world allows or has formally approved the use of copper antifouling coatings in their waters, and whenever a complete scientific risk assessment has been conducted, the use of copper has been approved. A complete risk assessment is appropriate for a complicated issue such as this because fouled vessel hulls have serious consequences, and the benefits of effective antifouling coatings that use safe and approved biocides such as copper have significant environmental benefits. Copper is still the largest, most successful, environmentally sound method used worldwide to prevent biofouling: some recent positive decisions are highlighted below.
• EU: After an extensive EU-wide review, the use of copper in antifouling coatings has been approved. The EU Biocidal Product Committee opinions on the antifouling copper compounds have recently been published by the European Chemicals Agency (Product Type 21, Antifouling) and recommended their approval for both commercial and yacht products, professional and nonprofessional applications. In addition, Sweden has overturned its local ban on copper in the ecologically sensitive Baltic region and is now authorizing copper antifouling paints there. Copper is now the only biocidal active substance that Sweden allows in the Baltic Sea. The exception is the Gulf of Bothnia, where all antifouling substances on pleasure craft are banned, due to the particular sensitivity of the region.
• New Zealand: A full scientific risk assessment for antifouling biocidal active ingredients was conducted in New Zealand in 2012-2013.1 Copper was re-approved as the principal biocidal component in antifouling paints because any risks are outweighed by the specific and significant benefits of copper, and of antifouling coatings in general. Several other active ingredients were banned as a result of this risk assessment study.
• USA: The U.S. Environmental Protection Agency is currently conducting a review for the uses of copper in numerous biocidal applications. The EPA conducts this type of review for all biocides on a regular basis. At this time it appears that all uses of copper, including antifouling coatings, will be reapproved in the next year or two.
• Washington State: Washington in the United States has passed legislation restricting the use of copper in antifouling coatings to a maximum 0.5%, but this is only for recreational vessels. It will not be phased in until 2018 and then only after further review. It is worth noting that this was a political decision: a scientific risk assessment was not conducted.
• California: The Department of Pesticide Registration (DPR) has carried out an extensive survey to determine the level of copper in marinas in California2 and, based on the results of this survey, has introduced copper leaching rate limits for pleasure craft antifouling coatings. The DPR objective is to keep the levels of copper in marinas below the EPA-approved safe limit of 3.1 ppb. For commercial shipping, there is no restriction on copper-containing antifoulings in California. The California State Lands Commission is currently drafting a regulation requiring appropriate biofouling control and limited biofouling on vessels entering California waters. This is part of the California Marine Invasive Species Program, which is charged with preventing or minimizing the introduction of non-indigenous species to California Waters from vessels over 300 gross registered tons.3 There are, however, strict guidelines in place for in-water cleaning of any biocidal antifouling in California, under the U.S. Environmental Protection Agency’s 2008 and 2013 Vessel General Permits, which prohibit in-water hull cleaning unless conducted using Best Available Technology (BAT).4
• Canada: After the final phase of re-evaluation of copper pesticides, Health Canada’s Pest Management Regulatory Agency, under the authority of the Pest Control Products Act and Regulations, has proposed continued registration of products containing cuprous oxide, copper hydroxide, metallic copper and copper present as mixed copper ethanolamine complexes, for sale and use in Canada. Based on a scientific study of the environmental fate characteristics of copper (free cupric ion is highly reactive in aquatic environments and binds tightly to sediment and organic matter), risks to aquatic organisms from antifouling uses are not expected to be of concern.5
The Benefits of Using a Premium Copper-Based Antifouling
Reduced Fuel Consumption
Due mainly to the rising cost of fuel and concerns about emissions of greenhouse gases, both the International Maritime Organization (IMO) and ship owners and operators have been taking renewed interest in ship energy efficiency.6 A fouled hull leads to increased frictional resistance, resulting in either a loss of speed or an increase in fuel consumption in order to maintain speed. Biofouling reduces the maneuverability of the vessel and may also cause deterioration to, or damage of, the coating system, leading to premature corrosion of the hull. This, together with an increased frictional drag, has both an economic and environmental impact on shipping operations.
According to the IMO, the world’s trading ships were estimated to burn 369 million tonnes of fuel in 2007 and are estimated to burn 486 million tonnes in 2020.7 As a result, the IMO has mandated that ship owners and operators undertake hull husbandry and ship performance monitoring in order to minimize greenhouse gas emissions. Chapter 4 of IMO’s MARPOL Annex VI now includes requirements mandating the Energy Efficiency Design Index for new ships and the Ship Energy Efficiency Management Plan for all ships. This requirement entered into force on 1 January 2013.8
In order to comply with this IMO legislation, increasingly sophisticated monitoring systems are being deployed on ships, using continuous analysis of voyaging data. These systems now have the ability to isolate hull and propeller effects, and are able to detect performance loss from fouling settlement.9 An ISO standard that recommends methods for measuring hull and propeller performance, and defines performance indicators for maintenance, repair and retrofitting, is currently going through the approval process.10
Whereas previously micro-fouling (slime) on commercial shipping was not considered detrimental to performance, with the main concern being prevention of macro-fouling (weed or animal), which has a very significant impact on fuel consumption and speed, recent upgrades in hull performance monitoring systems have shown that there can be a significant negative effect on performance even from micro-fouling slime. It has been reported that fuel efficiency can be improved by up to 10% through regular removal of micro-fouling slime by in-water cleaning.11, 12 Use of a high-performance copper-containing antifouling coating will minimize or eliminate the need for cleaning, but for some commercial vessels, especially those slow-steaming or after lay-up, in-water cleaning can be advantageous, and it is not unusual for in-water cleaning of micro-fouling slime to be undertaken before any macro-fouling occurs, and well before speed or fuel consumption are markedly affected. The removal of micro-fouling (slime) is relatively easy, and can be carried out with minimal damage to the antifouling coating since only gentle “grooming” is required, compared to the aggressive surface scouring necessary if barnacles or other types of macro-fouling are present.13, 14 Cleaning schedules for commercial vessels can vary greatly, but usually cleaning only starts one year or more after a new coating is applied, and then only once or twice a year thereafter, until the coating is too badly damaged or exhausted and has to be replaced.
The situation is different for recreational vessels, where speed and/or fuel consumption are less critical and so removal of micro-fouling slime by in-water cleaning is not generally necessary, except for racing yachts. Indeed, most yacht paint companies do not recommend any in-water cleaning be carried out on their products. There is serious environmental concern regarding in-water cleaning of recreational vessels in enclosed waters, especially if all the arisings from the cleaning cannot be collected and safely removed from the water. It has been proven that in-water cleaning of copper-based antifouling coatings results in a significant increase in dissolved copper, over and above that which occurs by steady state leaching.15 If cleaning is deemed necessary, it is recommended that recreational vessels be lifted out of the water for this, where the wash water and any other arisings can be readily treated to remove any chemical or other materials contained therein.
Comparing the relative effectiveness of different antifouling products requires an accurate knowledge of the surface preparation and the coating application, and then the ship’s subsequent operations. The operational history requires not just the service speed(s) and a list of port arrival and departure dates, but for any port visit greater than two days it is also necessary to ascertain where in that port the ship was stationary. Knowing where a vessel is anchored, moored or berthed for >48 hrs in any large sprawling hub port is especially important. Fouling settlement pressure and growth conditions are not uniform in a port, and vary widely between offshore port limits, inner anchorages, estuary terminals, enclosed basins, minor upstream berths, creek moorings, etc.16
It is also essential to have a full record of any hull and/or propeller cleaning event. The commercial diving report is not necessarily the end of the story: many reports are poorly if not misleadingly compiled by back-office juniors, who are given the supervisor’s notes and an SD photo card containing digital photos for extracting into a pre-formatted report. These formats contain no information or pictures of the specific brush types used, nor any reliable account of the actual areas where these were applied, with too few pictures added to the report for a reader to gauge the true pre- and post-clean appearance, surface roughness, remaining barnacle bases, etc. on the main areas. It is not uncommon for a commercial report to show two to three pictures captioned ‘Flat Bottom, Before Cleaning’ - which are close up examples of the worst fouled docking-block marks - followed by two to three pictures captioned ‘Flat Bottom, After Cleaning’ - which are wider-angle views of the true flat bottom that before cleaning had been lightly fouled by slime, bryozoa and the occasional goose, acorn barnacle or scattered juvenile tube worm.16
Jotun’s Hull Performance Solutions (HPS) are designed to make it easy to maximize hull performance and thereby reduce both fuel cost and greenhouse gas (GHG) emissions. The solutions combine state-of-the-art antifouling and application technologies with reliable performance measurements and high-performance guarantee. They offer substantial fuel cost and GHG emission savings, combined with a short payback period and limited risk.17
Figure 1 shows an illustration of Jotun’s HPS for a vessel that changed from a biocide-free foul release coating to the premium high-performance copper-containing antifouling SeaQuantum X200. The graph shows % speed loss over time. Additional notes about the figure include the following:
- The average additional speed loss in Period 2 (18 months) with the foul release coating was 4.3%, compared to the benchmark established in the first 12 months.
- After drydocking and replacing the foul release coating with SeaQuantum X200 in mid-year 02 there was a performance loss of less than 0.1% in speed compared to the benchmark established in the first 12 months.
- In the figure, the black lines indicate the one month moving average trend over the speed loss, the green lines indicate the level of the 12 months benchmark periods and the yellow lines the averages over the period after the benchmark period.
Prevention of Transfer of Aquatic Invasive Species
The introduction of invasive aquatic organisms can threaten freshwater, brackish and marine environments, human, animal and plant life, and economic and cultural activities.18 Examples of events causing alarm include invasions of the North American Great Lakes by the zebra mussel (Dreissena polymorpha), the Black Sea by the North American ctenophore (Mnemiopsis sallei), and inshore waters of south-eastern Australia by the Northern Pacific sea star (Asterias amurensis). Transfer of harmful aquatic species was initially attributed to the uptake, carriage and discharge of ballast water, and the initial focus of legislation by the IMO was on ballast water management.18 However it has since been suggested that more than 50% of non-indigenous species have been introduced to new environments as a result of fouling on the outer hull of vessels, or within niche areas such as sea chests, thruster tunnels and internal seawater pipework, with less than 50% coming from ballast water.19, 20 The IMO has published guidelines for ship owners and operators as to how to minimize the translocation of NIS resulting from biofouling on commercial vessel hulls,21 and has also made similar proposals for pleasure craft.22 Jurisdictions including Australia, New Zealand and California are enacting or planning to enact mandatory biofouling requirements, and a key recommendation common to these guidelines and requirements is the use of safe and effective antifouling coatings.
More than 4000 species have been recorded as fouling organisms, but not all become introduced to new environments as NIS, and an even smaller percentage cause harmful effects. For example, only 53 species of around 1600 global macrofouling NIS were designated as IMS of concern and, in Port Phillip Bay in southern Australia, of 160 non-native species only eight were considered to be of concern. While not “of concern”, many more NIS can be considered nuisance species because of their propensity to heavily colonize vessel hulls and artificial structures but not to invade natural environments. Micro-fouling organisms are commonly referred to as a biofilm or “slime”, such as the diatom Amphora coffeaeformis, and are individually much smaller organisms that are of global occurrence and unknown origin. These have not been considered to be NIS.23
There are many chemicals that are beneficial in small doses, but which when used in excess in the wrong place can cause considerable harm, and with the increase in use of copper in antifoulings since the mid-1980s marine scientists have been looking for any negative effects resulting from this increase. It has been proposed that use of copper in antifouling coatings can lead to an increase of NIS because some species are able to resist copper better than others.24, 25 The studies suggest that copper-tolerant NIS can be transported on copper antifouling paints, and thus displace the less copper-tolerant species in enclosed locations such as marinas, where the copper concentration in the water can be elevated. However other characteristics common in harbors and marinas can also promote the establishment of NIS, including the abundance of artificial substrates, shading and physio-chemical perturbation. Copper-tolerance can be considered a risk, but far from enhancing the transport of NIS, modern high-performance copper-based antifoulings, when used correctly and in line with IMO guidelines, are very effective at preventing growth of biofouling on all vessel types, and thus are an essential tool in preventing the transfer NIS.
As has been observed by Hadfield,26 the marine world of 10,000 years ago was not characterized by ships, barges, docks, floats and pilings, and most of the invertebrate species typical of the fouling community were never found elsewhere. Today’s fouling communities comprise species selected from environments throughout the world that have the characteristics to be able to colonize and survive on moving vessels. With the use of copper-based antifouling coatings on vessels through the past two centuries, it is not surprising that some widely spread fouling organisms show higher tolerance of copper than non-fouling species. Some species of bryozoan, such as Watersipora subtorquata and Bugula neritina,27, 28 and the tubeworm Hydroides elegans,29 are particularly noted for their resistance to copper antifouling paints. An effect known as “hormesis” has also been reported for a broad range of marine organisms in which growth is stimulated by sub-inhibitory levels of toxic agents including copper, but also other heavy metals and unrelated agents such as reduced salinity.30, 31
It is fortuitous for ship owners that compliance with the two pieces of IMO legislation referred to above (one concerned with ship energy efficiency and the other with prevention of transport of NIS) can both be achieved by use of an effective copper-based antifouling coating on the underwater hull, along with careful in-water cleaning when necessary, based on vessel type, usage and coating schedule.
References
1 http://www.epa.govt.nz/Publications/Antifouling_manufacturers_and_importers.pdf.
2 Singhasemanon, N.; Pyatt, E.; Bacey. J. Monitoring for Indicators of Antifouling Paint Pollution in California Marinas. California Environmental Protection Agency, Department of Pesticide Regulation, Environmental Monitoring Branch, EH08-05. Available at http://www.cdpr.ca.gov/docs/emon/pubs/ehapreps/eh0805.pdf, 2009.
3 http://www.slc.ca.gov/Programs/MISP.html.
4 In-Water Vessel Hull Cleaning Best Management Practice, California Regional Waterboard, July 2013, http://www.waterboards.ca.gov/sanfranciscobay/publications_forms/documents/In-water_vessel_hull_cleaning_fact_sheet.pdf.
5 PRVD2016-14 Copper Pesticides Environmental Assessment of Wood Preservatives, Material Preservatives and Antifouling Uses, May 2nd, 2016.
6 Eliasson, J. Hull Resistance Management in the New Era of Ship Energy Efficiency, Journal of Protective Coatings and Linings, Nov 2012.
7 IMO MEPC 60-4-21 Prevention of Air Pollution from Ships, The Importance of Using Effective Anti-Fouling Coatings in Relation to Greenhouse Gas Emissions from Shipping, Submitted by the International Paint and Printing Ink Council (IPPIC), Jan 2010.
8 http://www.imo.org/en/MediaCentre/HotTopics/GHG/Pages/default.aspx.
9 http://www.jotun.com/aa/en/b2b/paintsandcoatings/ships/Hull-Performance-Solutions.aspx.
10 ISO 19030 http://www.motorship.com/news101/regulation-and-classification/hull-performance-standard-reaches-draft-stage.
11 Kane, D. What the Hull is Happening: the Influence of Spotblasting and Fouling on Ship Performance, SNAME San Diego section, December 2012.
12 http://www.forcetechnology.com/en/Menu/Products/Maritime-onboard-systems/SeaTrend-performance-monitoring.htm.
13 Swain, G.; Tribou, M. Journal of Ocean Technology, Vol 9, No 4, 102-103, 2014.
14 https://maritimecyprus.files.wordpress.com/2016/02/intertanko-biofouling.pdf.
15 Earley, P. J.; Swope, B. L.; Barbeau, K.; Bundy, R.; McDonald, J. A.; Rivera-Duarte, I. Biofouling: Life Cycle Contributions of Copper from Vessel Painting and Maintenance Activities, http://dx.doi.org/10.1080/08927014.2013.841891, 2013.
16 Hilliard, R. Intermarine Consulting, Australia, Personal Communication.
17 http://www.jotun.com/aa/en/b2b/paintsandcoatings/ships/Hull-Performance-Solutions.aspx.
18 IMO International Convention for the Control and Management of Ships’ Ballast Water and Sediments, 2004.
19 Shipping World and Shipbuilder, Nov. 2013, p 7.
20 Morrisey, D.; Gadd, J.; Page, M.; Floerl, O.; Woods, C.; Lewis, J.A.; Bell, A.; Georgiades, E. In-Water Cleaning of Vessels: Biosecurity and Chemical Contamination Risks, New Zealand Government Ministry for Primary Industries, MPI Technical Paper No: 2013/11.
21 Guidelines for the Control and Management of Ships’ Biofouling to Minimize the Transfer of Invasive Aquatic Species. Annex 26: Resolution MEPC.207(62), Adopted 15th July 2011.
22 IMO Guidance for Minimizing the Transfer of Invasive Aquatic Species as Biofouling (Hull Fouling) for Recreational Craft, MEPC.1/Circ.792 12 November 2012.
23 Lewis, J.A. Chairman of IMarEST Biofouling Management Expert Group, Personal Communication.
24 Piola, R. F.; Dafforn, K. A.; Johnston, E. L. The Influence of Antifouling Practices on Marine Invasions, Biofouling, Vol 25, No. 7, 633–644, October 2009.
25 McKenzie, L.A.; Brooks, R.C.; Johnston, E.L. A Widespread Contaminant Enhances Invasion Success of a Marine Invader, Journal of Applied Ecology, 49, 767–773, 2012.
26 Hadfield, M.G.; Carpizo-Ituarte, E.; Holm, E.; Nedved, B.; Unabia, C. Macrofouling Processes: a Developmental and Evolutionary Perspective. Paper presented at 10th International Congress on Marine Corrosion and Fouling, Melbourne, Australia, 8-12 February 1999.
27 Ryland, J.S. Catalogue of Main Marine Fouling Organisms (found on ships coming into European waters). Volume 2. Polyzoa. O.E.C.D. Publications, Paris, 1965.
28 Piola, R.; Johnston, E. Differential Tolerance to Metals Among Populations of the Introduced Bryozoan Bugula neritina. Marine Biology 148 (5), 997-1010, 2006.
29 Lewis, J.A.; Smith, B.S. Hydroides Settlement in Sydney Harbour (Australia) and its Control in Sea-Water Cooling Systems. p.. 464-466. In, Rossmoore, H.W. (ed.), Biodeterioration and Biodegradation. Elsevier Applied Science, London, 1991.
30 Stebbing, A.R.D. Hormesis – Stimulation of Colony Growth in Campanularia flexuosa (hydrozoa) by Copper, Cadmium and Other Toxicants. Aquatic Toxicology 1 (3-4), 227-238, 1981.
31 Stebbing, A.R.D. Hormesis – the Stimulation of Growth by Low Levels of Inhibitors. The Science of the Total Environment 22, 213-234, 1982.
Looking for a reprint of this article?
From high-res PDFs to custom plaques, order your copy today!