Color-Changing Nanocoatings Offer Energy Savings
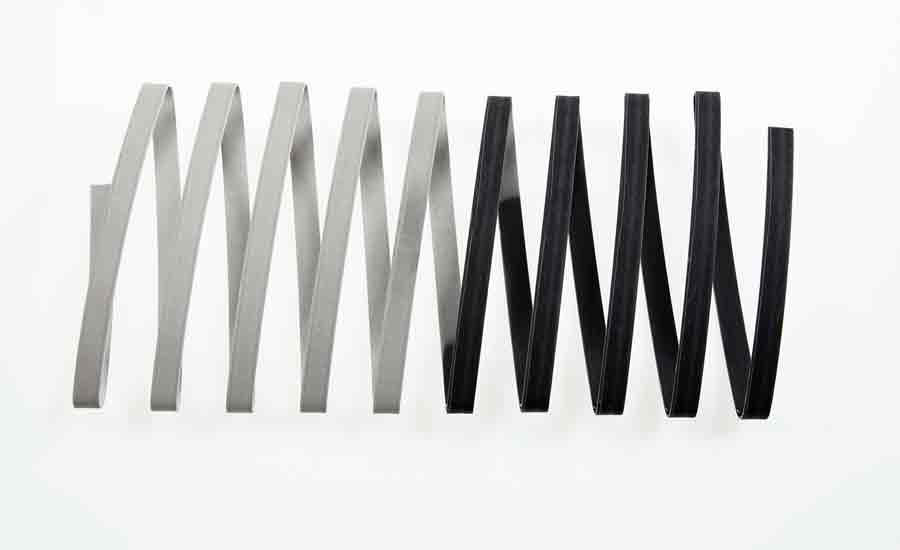
MUNICH - Thermochromic nanocoatings employed appropriately can help reduce energy usage and generate savings. The coatings either absorb heat or permit its reflection, depending on their temperature. Researchers from the Fraunhofer Institute demonstrated this phenomenon using samples of coated metal strips at the Hanover Trade Show in April of this year.
Nanoparticles possess an especially large surface-area-to-volume ratio. This makes them extremely efficient and reactive. Tiny amounts are sufficient to produce large effects. Researchers of the Fraunhofer Institute for Chemical Technology ICT in Pfinztal near Karlsruhe, Germany, are utilizing this characteristic to create novel coatings. They are incorporating active nano-materials into polymer systems. These coatings can be applied easily like paint or varnish.
“However, the special properties of nano-composites only become apparent if the particles do not clump so that an agglomeration is avoided,” explains Helmut Schmid from Fraunhofer ICT. The scientist together with colleagues at the institute developed a process through which the nanoparticles are distributed uniformly in the polymer matrix. “In addition, integrating the nanoparticles in the plastic system provides extra safety. The binding forces prevent the uncontrolled release of individual nanoparticles,” explains Schmid. “We can prove this using analytical techniques able to detect extremely small concentrations of substances.”
The process is highly adaptable and suited to processing quite varied nanomaterials. An additional advantage is that small amounts of substances can be bound in environment-friendly, water-based systems of plastics that release hardly any VOCs. These coatings can be applied directly without first requiring a primer coat – experts refer to this property as "direct-to-metal." In addition, the layers prevent oxygen from reaching the metal and thereby protect against corrosion.
Researchers at Fraunhofer ICT worked together with partners in industry under a project funded by the German Federal Ministry of Education and Research (BMBF) on novel nanocoatings for metallic wire and strip. The experts developed thermochromic coatings during the project that change color depending on their temperature. The coatings thereby either absorb heat or become transparent and permit its reflection “Metal strip possesses very special properties when coated in this way. If temperatures are below 30 °C (about 86 °F), the black coating absorbs heat. If it is warmer, the color changes. The varnish, which has now become transparent, allows the infrared radiation to be reflected,” Schmid explains. Strip and wire coated like this are useful in architectural applications. They can be interwoven and used as exterior self-regulating thermal cladding for walls and façades to help cool buildings passively and thereby reduce operating costs. The researchers are continuing to work on additional nano-systems such as coatings with luminescent properties, for instance. These kinds of effects are useful for safety markings and signage. The coatings can also help clearly differentiate branded products from pirated copies, since pirates do not have these kinds of luminescent nanocoatings at their disposal.
Researchers with the Application Center for Plasma and Photonics of the Fraunhofer Institute for Surface Engineering and Thin Films IST in Braunschweig, Germany, have also become involved in nanotechnology. They are designing particle surfaces with beneficial properties by applying, for example, carbon or metallic nanocoatings. Specific particles surrounded by a 1-2 nm carbon nanocoating become more electrically conductive, and this leads to an enhanced performance of lithium-ion batteries.
Nanocoated micro-particles have other advantages as well: if you apply titanium nitride or copper to stainless steel particles, for example, the substance no longer agglomerates. A powder treated in this way can then be used to metalize temperature-sensitive materials like plastic or paper. But how can layers of thin metal be homogeneously applied to even three-dimensional surfaces? The IST scientists employ plasma spraying for this purpose. For example, nano-shaped particles of stainless steel are thermally activated using an atmospheric-pressure plasma process and are deposited as a metal film onto the material to be coated.
Looking for a reprint of this article?
From high-res PDFs to custom plaques, order your copy today!