Radiation Curing: A Key Partner in 3D Printing
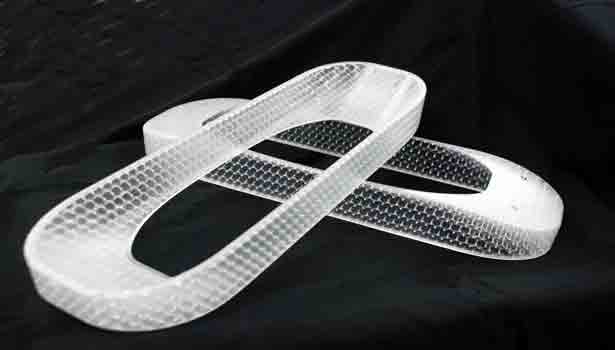
3D printing – or additive manufacturing – has come a long way in a very short time, aided in no small measure by the capabilities of UV and EB curing. In this article, the Secretary General of RadTech Europe, the European association for the radiation curing technologies, reviews the current status in the dynamic 3D printing market.
The UV and EB technologies have been around for many years, enabling speedy and efficient curing of, for example, wooden flooring/panels and architectural coatings, and – more recently – the fast curing of printing inks, especially for labels and packaging, to deliver higher press speeds. Using UV/EB technology today, 3D objects can be created in plastic from a digital file. This is the new focus for a much wider range of industries, from medical devices to toys, custom jewelry, electronics and automotive components. All these new applications involve radiation curing.
According to a newly published report from U.S.-based MarketsandMarkets, the global 3D printing/additive manufacturing market – embracing 3D print machines, printing materials and solutions providers – is growing very fast. It is expected to reach a value of $8.43 billion by 2020, at a consolidated annual growth rate of 14.37% between 2014 and 2020.
Traditional industrial coatings – particularly wood coatings (the biggest overall end-use market for UV-cured coatings) – remain UV curing’s fastest-growing sector, followed by electronics. The UV resins themselves provide the properties for the final product, and coatings technology laid the foundations for radiation curing’s advance into the realms of the new 3D printing arena, which is creating new opportunities that transcend the simple improved speed, efficiency and significant cost-reduction factors that first attracted those who embraced the technology in its various forms.
Process Choice
The actual process selected for 3D printing/additive manufacturing depends on the method to be used to add different materials to build a 3D structure, whether liquids or solids. Liquid systems are most often polymerized using UV energy, with the liquid formulation deposited via jetting, followed by UV curing, and the pattern repeated until the object is complete. LED UV curing is another current development of interest, which offers higher cure speeds although still a limited power output. Laser curing is another choice.
Stereolithography (SLA), the oldest established 3D technology base, builds a product vertically layer-by-layer – cured by a laser beam – in a vat of liquid polymer. DLP, digital light projection, uses a projector similar to those used for business presentations to project the image of the desired cross-section of an object into a vat of light-reactive plastic (photopolymer). The light selectively hardens only the area specified. The newest option, material jetting or 3D inkjet printing, directs ultra-thin layers of polymer from a multiple-nozzle print head on to a platform, and each layer is individually UV cured. This creates a complete cross-linked plastic structure, which is supported by a gel-like material that allows the creation of complex structural geometries and overhangs, and delivers a very hard and strong result that can combine different materials and different colors in the same product construction. A small, rigid, plastic model car, for example, may be furnished in-line with soft rubber tires. These physical attributes are particularly suitable for 3D inkjet printing, with an appropriate material mix, for rapid prototyping across a wide range of industries and applications.
Medical Markets
3D printing is already reshaping the medical device industry, especially in the hearing aid, orthopedic (prostheses) and dental fields. It is also driving new product development, thanks to its ability to facilitate rapid prototyping and the creation of medical models. Human tissue engineering is just one area where there is active progress, and experiments in additional innovations continue apace. Naturally, however, the materials used must be approved and declared safe for both limited skin exposure and for implantable applications. Only a handful, such as nylon 11 and PLA (polylactic acid) for limited skin exposure and titanium and stainless steel for implantable use are currently approved. Further progress here depends on successful tests results with materials such as magnesium, ceramics and super alloys.
Aerospace and Automotive Markets
The aerospace industry is also benefiting from UV-cured additive manufacturing. As it requires very small quantities of components, the technology can be very cost effective and offers fast product delivery without the high costs and time delays associated with precision molds and other physical manufacturing. 3D printing is also enjoying increasing popularity in the automotive industry. A good example is Opel’s creation of 3D-printed custom assembly tools and jigs to aid accurate placement of its OEM vehicle parts and accessories. Even Formula One cars today sport 3D-printed protective body trim.
Consumer Goods
The consumer markets are keen adopters of a technology that delivers professional, high-quality 3D-printed products that can even be customized. Today, we see model cars, sports goods, costume jewelry, luggage, promotional giveaways and many other 3D-printed items on the retail sales shelf. The consumer market also has its own production stream: home 3D printers, mainly based on thermoplastic extrusion technology, are now high-fashion items in the technology goods market, but lack the resolution accuracy and speed of professional 3D printers.
Trends and Innovation
The desire to achieve better quality and the machines’ ability to print a wider range of materials are still key drivers for innovation. There is much activity in the development of software (scanning capabilities), and in resins and equipment for 3D inkjet printing. The industry is also focused on matching manufacturing technology to key new materials; on multi-material machines that use the least possible quantity of resources, with no waste; on-demand manufacturing of customized products and short-run products; light-weighting products and exploiting freedom of design in both material composition and geometries; and even 3D print implementation in conventional processing chains in industry. UV curing is a key enabler in innovation in the technology, because it offers easier tool path creation and smaller files, a wider variety of materials and chemistries than other options, and higher detail. As the cost of consumer electronics reduces, the versatility of UV-based systems will continue to expand the market for 3D printing.
Sustainability
There are also important initiatives today to create a sustainable platform for 3D printing, both for collecting plastics for recycling and re-use in 3D printing and for turning recycled plastics into a major source for 3D-printable filament. The technology’s growing success means that there is now also a real need to establish international and European standards for additive manufacturing. Here, the EU project SASAM, the Support Action for Standardization in Additive Manufacturing, has built a pioneering roadmap for standardization activities. The international 3D Printing Association is also drawing together the threads of an industry infrastructure, and RadTech Europe’s members are key partners in this fast-growing market for the skills and benefits of radiation curing, providing up-to-the-minute chemistry, consumables, and equipment that meet requisite regulatory and safety standards.
A Dynamic Future?
Whether 3D printing/additive manufacturing will in time become a full-scale competitor to traditional manufacturing techniques in the mass markets remains in question. However, the industry’s technical supply chain is continuing to develop its capability for creating products, such as laptop computers, tablets and other digital devices, which involve complex multiple-material components and low-cost, speedy manufacturing. UV curing is the key enabler. As in many major sectors, radiation curing certainly has a dynamic future.
Looking for a reprint of this article?
From high-res PDFs to custom plaques, order your copy today!