What is the Level of Confidence in Measuring Gloss?




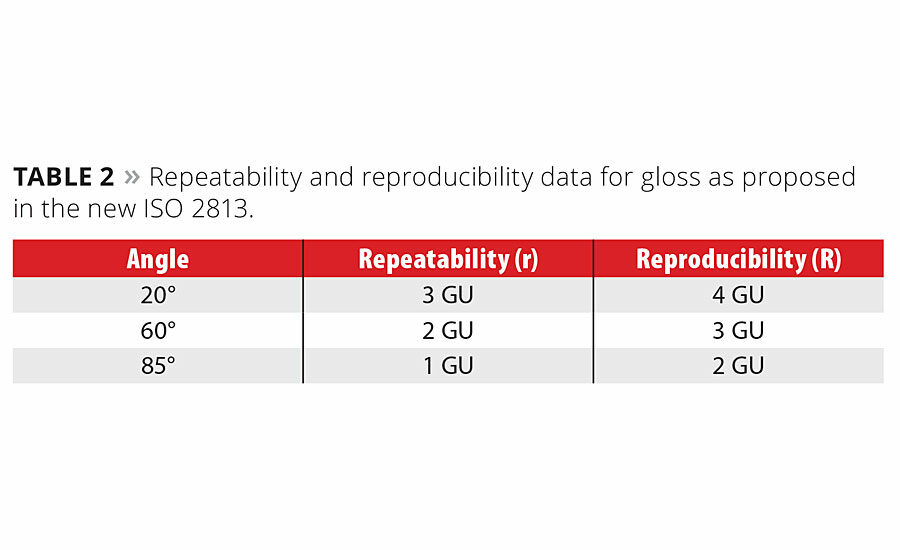





Gloss meters became popular in the 1970s. German equipment manufacturers started to mass-produce gloss gauges and standards at affordable prices that were suitable for use in production lines. These instruments were based on laboratory instruments used in the paper industry at that time. Due to the evolution of technology and more stringent esthetic demands, the tolerances of gloss unit (GU) specifications were significantly reduced. Some instrument manufacturers claim an accuracy of their gloss meters to within 0.1 GU, and application specifications often state a bandwidth of just 1 GU as acceptance criteria. Are these criteria realistic? In order to answer this question we will have to look at the definition of gloss as stated in the international (ISO and ASTM) standards and as measured by the reference laboratories.
Defining Gloss
To define a unit like gloss, we need to define some reference points. The defined gloss reference points in the standards are a 0 GU and a 100 GU reference. The 0 GU reference is a full, dull matte surface with zero reflection. For 100 GU the reference is based on black or quartz glass. The refractive index, a derivate of the change in angle when light passes from one media into another at a specific wavelength, is used to calculate the reflectivity of a surface. This is done using the Fresnel equation. This seems pretty robust, but there is a flaw in the definition of the used wavelength. ASTM and ISO do not agree on the wavelength of the spectral line to be used for the reference of 100 GU. ISO uses the d-line (helium) and ASTM refers to the D1-line (sodium). This is in reality a difference of only 1.7 nm, but in terms of standardization is an important deviation that may lead to unexpected results.
In general, the use of only two reference points is a very thin basis for a standard. Moreover, the linearity between these two points is just an assumption. There are no means to verify this assumed linearity, as more reference points have not been defined and are thus not available.
Surface Roughness
A second non-specified parameter has been observed. The surface roughness of the calibration standard tiles is not part of the Fresnel equation, nor is roughness taken into account in relevant standards. Some standards specify flatness, but roughness is specified, at its best, as “highly polished” (how high is high?). However surface roughness does affect the reflection of a surface. The gloss calibration tiles used by instrument manufacturers to validate linearity of their products are made of the same material for the entire gloss range, however with a varying surface finishing such as roughness and texture.
Strictly speaking these tiles should all have the same gloss value due to Fresnel’s equation and the definitions of the standards. However, when measured by a reference lab (NIST or BAM) they all produce different values. So the question arises, “Does the surface roughness affect the gloss value?” The answer is clear: Yes it does, and the effect is significant.
Table 1 shows the main parameters used in several global standards. The variance in gloss value caused due to this difference can add up to several gloss units.
Figure 1 shows the relation between gloss and roughness. The rougher the surface the less glossy it is. The graph is the gloss correlation to Ra-value (arithmetic mean surface roughness). All data is obtained on black glass tiles of the same material with the same refractive index.
Lack of Harmonization
These two issues, surface roughness and wavelength of the spectral line, are both a systematic problem in the harmonization of the gloss standards, making it impossible to work in compliance to multiple standards simultaneously. The design and geometry of gloss meters is often suitable for operation within multiple standards. However the calibration of the gloss gauge on the currently defined standards causes a problem, as shown in Table 1. Even the two main reference laboratories, NIST and BAM, are not in line with each other. NIST refers to the ASTM standard and BAM to the ISO standard.
The reason for the lack of harmonization between the standards is hard to explain. Literature studies do not show any important research on gloss/reflection versus the surface roughness. Work has been done on the coatings, but usually in the context of looking at haze, distinctness of image and orange peel – all important parameters but all without a defined reference-standard value. It seems the standard for gloss is, mildly speaking, at least questionable.
Some scientific studies have been done on the behavior of light on rough surfaces, like the Beckman – Kirchhoff scatter theory. However there is no unified theory linking this theory and the Fresnel equation. A scientific study researching if both theories can be combined could create a final and unambiguous definition on the gloss calibration tiles to determine an absolute value for ISO and ASTM to unite on.
In addition to uncertainty on the definitions of the gloss standards there are other concerns. The traceability that everybody wants for their methods is in serious danger. All certified laboratories need their standards to be sent in for calibration on a regular basis and need firm traceability to the reference standards. A reference standard should be at least of a higher level of certainty than the calibration standard. This would imply annual regular verification of the reference standard in use.
Many ISO 17025-certified calibration laboratories calibrate user tiles, as supplied with each commercial gloss meter, by means of a verification with another commercial gloss meter. This gloss meter itself is calibrated on BAM-certified tiles. In the relevant 100 GU range BAM states an uncertainty of up to ±1 GU. Combining this with the reproducibility and accuracy of the commercial gloss meter that is used for the verification, easily adds up to an error of several gloss units.
The main reference standards at BAM and NIST should be checked according to their refractive index. In the last 15 years there has never been a cross check between these two main laboratories. Many aspects regarding the gloss reference are unclear and need to be sorted out, such as correlation between roughness and gloss, wavelength of the spectral line and the assumed linearity of the calibration line.
The current situation has been one of the motivations of ISO to rework the ISO 2813 gloss standards. In order to lift the standard to an official next-level working document, ISO required a round robin or inter laboratory study (ILS). A selection of the leading brands of commercial gloss meters was used for this study. The study proved that the repeatability and reproducibility values as stated in the datasheets of the instruments used in the ILS were far from being realistic. Furthermore it was found that the data these repeatability and reproducibility values were based upon was lost over time. Based on the outcome of the round robin test, ISO has decided to state new levels of reproducibility (R) and repeatability (r) in the upcoming version of ISO 2813. These levels reflect what is currently feasible with high-end professional gloss meters (Table 2).
Conclusion
ISO has made the first step by renewing ISO 2813, however this solves just a part of the problem. The main issue is with the primary standard. All data is currently derived from just one reference, a quartz-glass wedge with no proof for the assumed linearity. Ideally a series of reliable reference materials would be developed and defined to prove and secure gloss references over a range of values rather than just one or two points. A series of references would also prove or disprove the assumed linearity of the calibration line. Thorough scientific research seems to be required to define the effects of roughness and wavelength in order to develop a primary standard that puts ISO and ASTM in-line and that leaves no room for questions. Ideally these primary standards are of an accuracy level at least tenfold better than those of today’s commercial gloss meters.
Scientific research on a global definition of gloss would be of great use to the industry. All specifications on gloss should be checked for feasibility and correctness. Although gloss is a general accepted appearance criteria for quality control in many industries, recent revelations on gloss standards require us to rethink the way we consider the accuracy of our obtained results.
References
1. ISO 2813:1994 Paints and varnishes - Determination of specular gloss of non-metallic paint films at 20 degrees, 60 degrees and 85 degrees (1994).
2. ASTM D523 - 14 Standard Test Method for Specular Gloss (2014).
3. ISO 7668:1986 Anodized aluminium and aluminium alloys - Measurement of specular reflectance and specular gloss at angles of 20 degrees, 45 degrees, 60 degrees or 85 degrees (1986).
4. IS Z 8741:1997 Specular glossiness -Methods of measurement (1997).
5. ASTM C584 - 81(2011) Standard Test Method for Specular Gloss of Glazed Ceramic Whitewares and Related Products (2011).
6. ASTM D1455 - 87(2008) Standard Test Method for 60° Specular Gloss of Emulsion Floor Polish (2008).
7. ASTM D2457 - 13 Standard Test Method for Specular Gloss of Plastic Films and Solid Plastics (2013).
8. V001-8.6E0078 BAM-Aktenzeichen von Reflektometerwerten zur Glanzbeurteilung (BAM).
9. Nadal, M.E.; Early, E.A.; Thompson, A. NIST Special Publication SP250-70 Specular Gloss.
10. NA 002-00-07 AA N 1322 EN ISO 2813 (D) Manuskript für prEN ISO 813 (deutch) – Überarbeitung.
11. NA 002-00-07 AA N 1451 Auswertung Ringversuch ISO 2813 Glanz Messungen Teil 1.
12. NA 002-00-07 AA N 1452 Auswertung Ringversuch ISO 2813 Glanz Messungen Teil 2.
13. ISO TC 35/SC 9/WG 31 N147 Round robin, Gloss measurement of coatings with ISO 2813 (January 2011) Evaluation, statistics, summary.
14. Lide, D.R. Handbook of Chemistry and Physics 75th edition, CRC Press.
15. Yonehara, M.; Matsui, T.; Kihara, K.; Isono, H.; Kijima, A.; Sugibayashi, T. Experimental Relationships between Surface Roughness, Glossiness and Color of Chomatic Colored Metals, The Japan Institute of Metals, 2014.
16. O’Brien, W.J.; Johnston, W.M.; Fanian, F.; Lambert, S. The Surface Roughness and Gloss of Composites, School of Dentistry, University of Michigan, Ann Arbor, Michigan 48109, 1984.
17. Farrier, L.M. Influence of Surface Roughness on the Specular Reflectance of Low Gloss Coatings Using Bidirectional Reflectance Measurements, AFRL-ML-WP-TM-2007-4019.
Looking for a reprint of this article?
From high-res PDFs to custom plaques, order your copy today!